AEM 30-71XX Infinity Stand-Alone Programmable Engine Mangement System Full Manual User Manual
Page 287
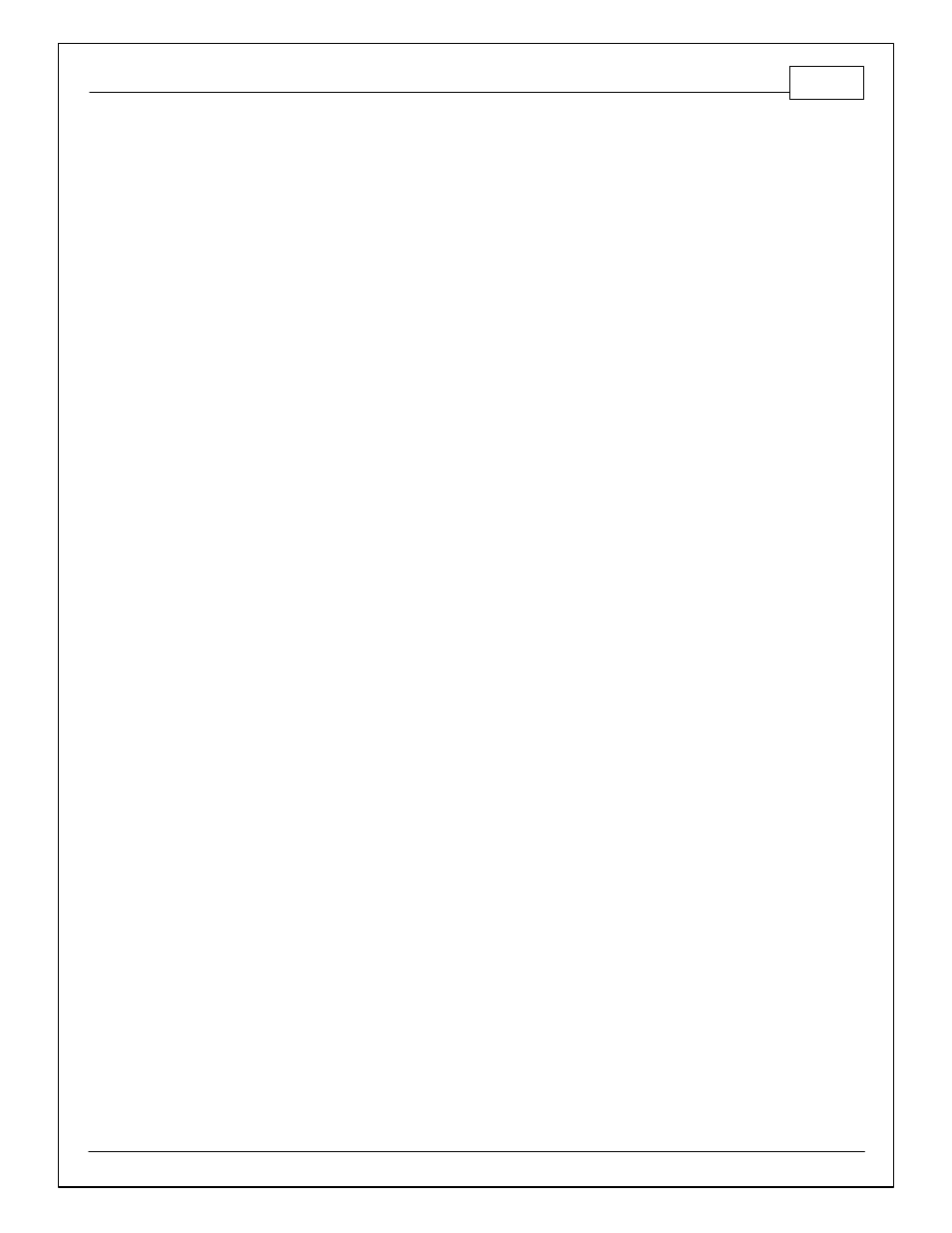
EFI Components
281
© 2014 AEM Performance Electronics
When ignition occurs, a flame kernel starts at the spark plug electrode and expands across the
combustion chamber. As the front progresses across the chamber, the hot expanding gas
compresses and heats the end gasses and mixture at the opposite end of the chamber. If the
pressure, and consequently temperature, inside the chamber increases beyond the flash point of
the end gas, auto ignition occurs. Because the pent roof type of chamber has a spark plug that is
nearer to the geometric center of the chamber, the flame travels more evenly across the
combustion chamber, leaving very little end gas that can be compressed or ignited by the
advancing flame front. Thanks to the short distance the flame front has to travel in pent roof type
chambers, ignition timing usually does not have to be as advanced as much as a wedge type
chamber, to achieve maximum torque. We find that there is usually about five to eight degrees
less timing required for pent roof combustion chambers than for wedge types.
Charge motion, which is comprised of intake swirl and squish; increase combustion speed when
compared to a standard combustion chamber. The combination of these factors increases the
mean effective pressure (MEP), lowers fuel consumption, and delivers smaller cycle-to-cycle
variations at full throttle operation.
In addition to the performance benefit of effective charge motion, the resulting factors reduce Hc
emissions, with a slightly increased Nox component. At partial load the benefits of charge motion
vs. a standard combustion chamber are similar, but due to the decrease in density of the intake
charge, not very.
The combination of swirl and squish is greater than either squish or swirl alone. Swirl improves
mixture preparation and is mostly responsible for reducing ignition delay and cycle-to-cycle
variations. Swirl is accomplished through the inlet port design or by using shrouded valves in the
combustion chamber. As engine speed increases, the swirl motion increases along with it.
Cycle-to-cycle variations decrease with increasing swirl action.
Squish is accomplished via a small gap between the head deck and the piston top. The
decrease of this gap drives the inlet charge toward the spark plug electrode. An additional
benefit of having this small gap is the reduction of end gas volume at the extreme edges of the
cylinder. This reduces the tendency for spark knock and leads to a reduction of Hc emissions.
Cycle-to-cycle variation refers to a situation where an engine operates on the threshold of
knocking or detonation throughout the engine cycles and is based on the average peak pressure
of all of the cycles. The cycles with lower peak pressures may not be prone to detonation, while
those with higher peak pressures may detonate with increasing intensity as peak pressure
increases. Increasing this cyclic variation will increase the number of cycles that detonate, and
decreasing the number leads to less cycles that detonate.
Ignition Delay is the point at which perceptible inflammation of the mixture and a pressure rise in
the combustion chamber occurs. The time between when spark occurs at the spark plug and
when inflammation of the mixture occurs is the delay time. This delay is caused by the chemical
reactions that take place when the rate of reaction after the delay accelerates to an extent that