Lambda feedback tuning – AEM 30-71XX Infinity Stand-Alone Programmable Engine Mangement System Full Manual User Manual
Page 138
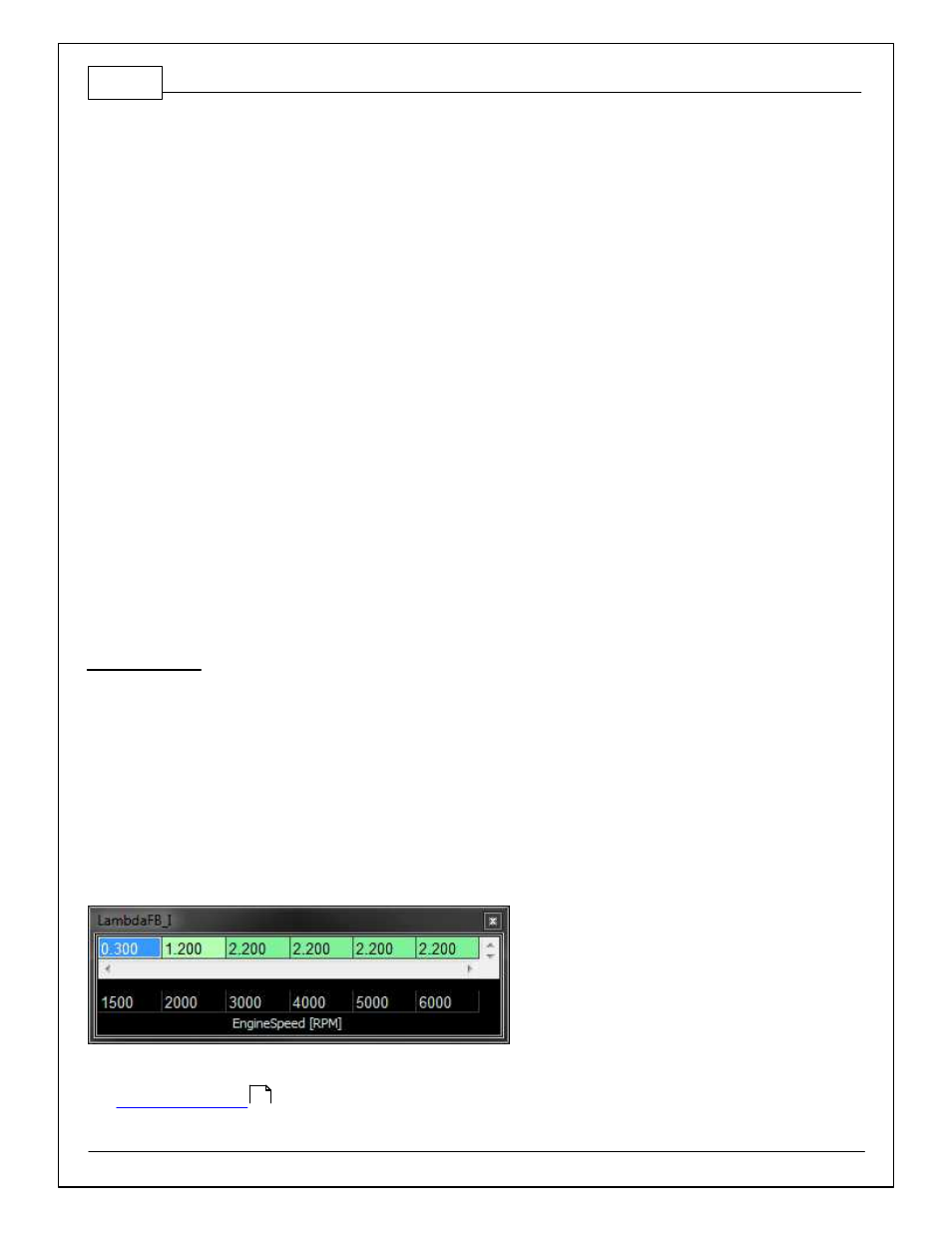
132
© 2014 AEM Performance Electronics
Infinity User Manual
disabled, such as DecelFuelCut or rev limiters (including the 2 Step limiter, 3step limiter and any
fuel/spark cuts calculated by Traction Control). The ECU's channel LambdaFB_Disabled can
be viewed or datalogged to see if feedback is disabled. After lambda feedback has been
disabled, the activation conditions must be met for 750ms before lambda feedback will turn back
on.
Lambda Feedback tuning:
The ECU uses PID feedback to make fuel corrections based on the measured lambda signal.
When tuning the PID gains, it helps to understand how the O2 sensor measures the oxygen
content of the exhaust gas. The sensing element is protected by a metal shield, and this shield
has small holes which allow exhaust gas to flow across the sensing element. At low engine
speeds, exhaust gas travels relatively slowly so the sensor will take more time to detect the air/
fuel ratio of the exhaust. The sensor's distance from the exhaust ports is also a factor in response
time. The sensor response time for your setup can be observed by datalogging the fuel injector
pulsewidth Inj1Pulse [ms] and the Lambda1 signal, then making a large change to the values in
the VETable or LambdaTargetTable. Observe how the sensor's response time will be faster at
higher RPM, especially at higher engine loads. Because of this slight delay in detecting the
oxygen content of the engine's exhaust, Lambda feedback gains must be set to lower values at
low RPM. If the feedback gains are too high at idle, the feedback will make corrections more
quickly than the sensor can measure O2 changes in the exhaust and the engine RPM may 'hunt'
due to fluctuating air/fuel ratios. At high engine speeds, the sensor detects changes in exhaust
air/fuel ratio more quickly so the Lambda feedback gains should be increased for quicker
feedback response.
LambdaFB_I
Units: Integral Gain vs RPM
Description: This table sets the feedback's Integral gain as a function of Engine Speed.
Integral control uses an integrator or 'accumulator' method, essentially checking if the Lambda
target error is positive or negative and then taking one step up or one step down every 10ms to
reduce the target error. The advantage of integral response for Lambda control is the fuel trim will
be smoothly adjusted until the measured Lambda value reaches the target, and then remain at
whatever feedback value reached the target. Note: Although Integral gain is less likely to cause
hunting or fluctuations than Proportional or Derivative gains, excessively high Integral values will
take steps that are too large which can result in instability.
Min value = 0.000, Max value = 6.375
The Proportional and Derivative gains for Lambda feedback can be adjusted in the wizard. See
the
section of the wizard for more details.
198