IAI America PCON-SE User Manual
Page 121
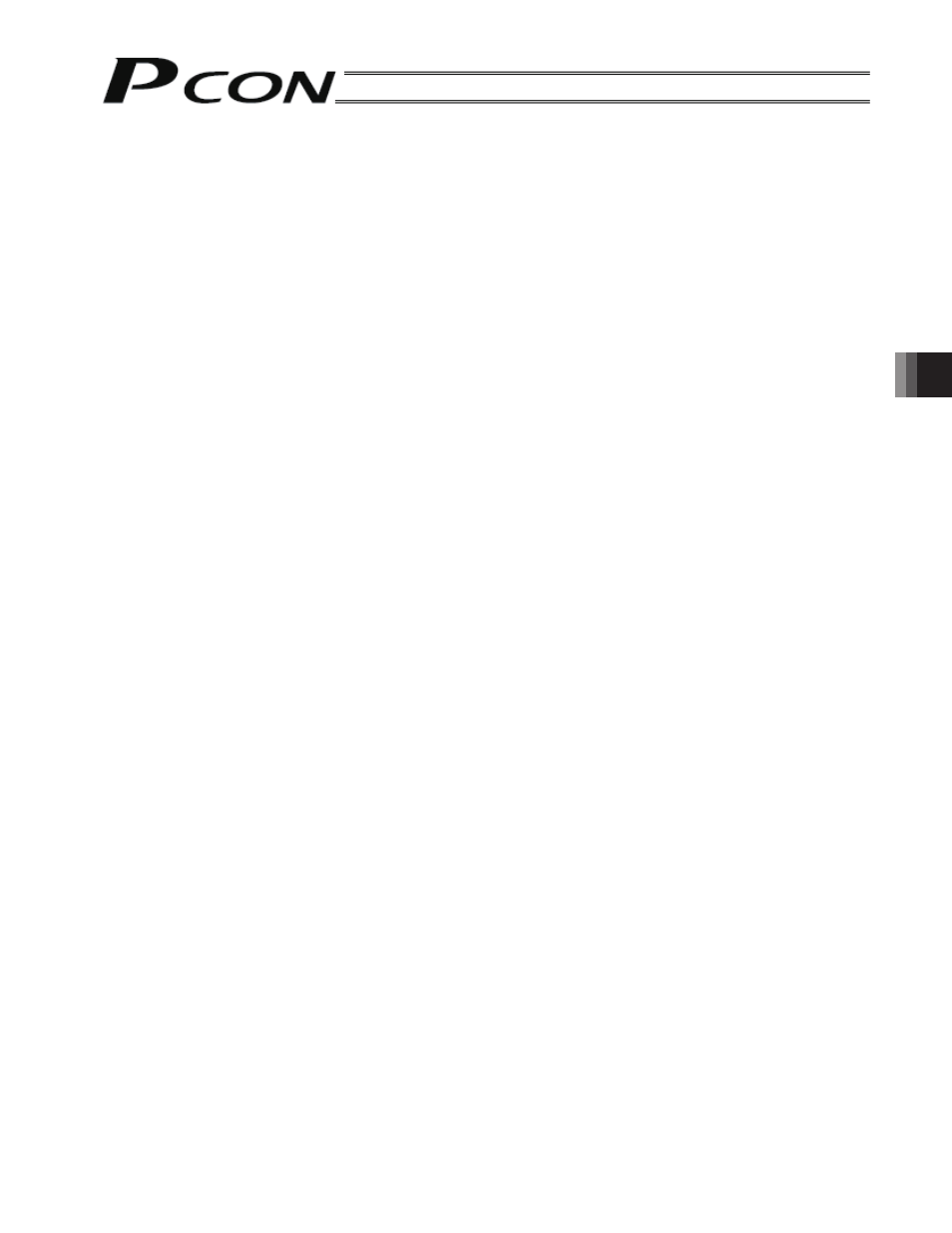
109
6. T
roubleshooting
• Home return ends in mid-process in a vertical application.
Cause: [1] The loading mass exceeds the rating.
[2] The ball screw is receiving torsional stress due to the affixing method of the actuator, tightening of
bolts only on one side, etc.
[3] The slide resistance of the actuator itself is large.
Action: If [1] is the case, increase the value set in user parameter No. 13 (current-limiting value during home
return).
Increasing this value increases the home return torque. As a guide, the set value should not exceed 75%.
[2] Loosen the fixing bolts and check that the slider moves smoothly.
If the slider moves smoothly, review the affixing method and bolt tightening condition.
[3] If the slide resistance of the actuator itself is large, please contact IAI.
• Noise occurs during downward movements in a vertical application.
Cause: The loading mass exceeds the rating.
Action: [1] Decrease the speed.
[2] Decrease the value set in parameter No. 7 (servo gain number).
Do not decrease the parameter setting below “3.”
• Vibration occurs while the actuator is at standstill.
Cause: The slider is receiving an external force.
Action: If the external force cannot be removed, increase the value set in user parameter No. 12 (current-limiting
value at standstill after positioning).
Increasing this value increases the holding torque at standstill. As a guide, the set value should not
exceed 70%.
• The actuator overshoots when decelerated to a stop.
Cause: The load inertia is high due to an inappropriate balance between load and deceleration.
Action: Decrease the acceleration/deceleration setting.
• The home and target positions sometimes shift.
Cause: [1] The encoder waveform is disturbed by the effect of noise.
[2] In the case of a rod-type actuator, the non-rotation precision increased due to application of rotating
moment to the rod.
Action: [1] Check if the grounding is implemented correctly. Also check for any equipment being a potential
noise source.
[2] The actuator may have to be replaced in some cases. Please contact IAI.
• The actuator is slow during push-motion operation.
Cause: The setting of current-limiting value is low relative to the loading mass or slide resistance.
Action: Increase the setting of current-limiting value during push-motion operation.
• The actuator moves only half of the specified distance or twice.
Cause: [1] The combination of the controller and actuator is incorrect.
Since the lead length of the ball screw varies depending on the actuator type, incorrect combination
changes the moving distance and speed.
[2] IAI’s error before shipment.
Action: [1] If there are multiple actuators of different types, check them for adequacy before connecting them
with the controller by the attached seal labels, etc.
[2] Please
contact
IAI.