IAI America PCON-SE User Manual
Page 106
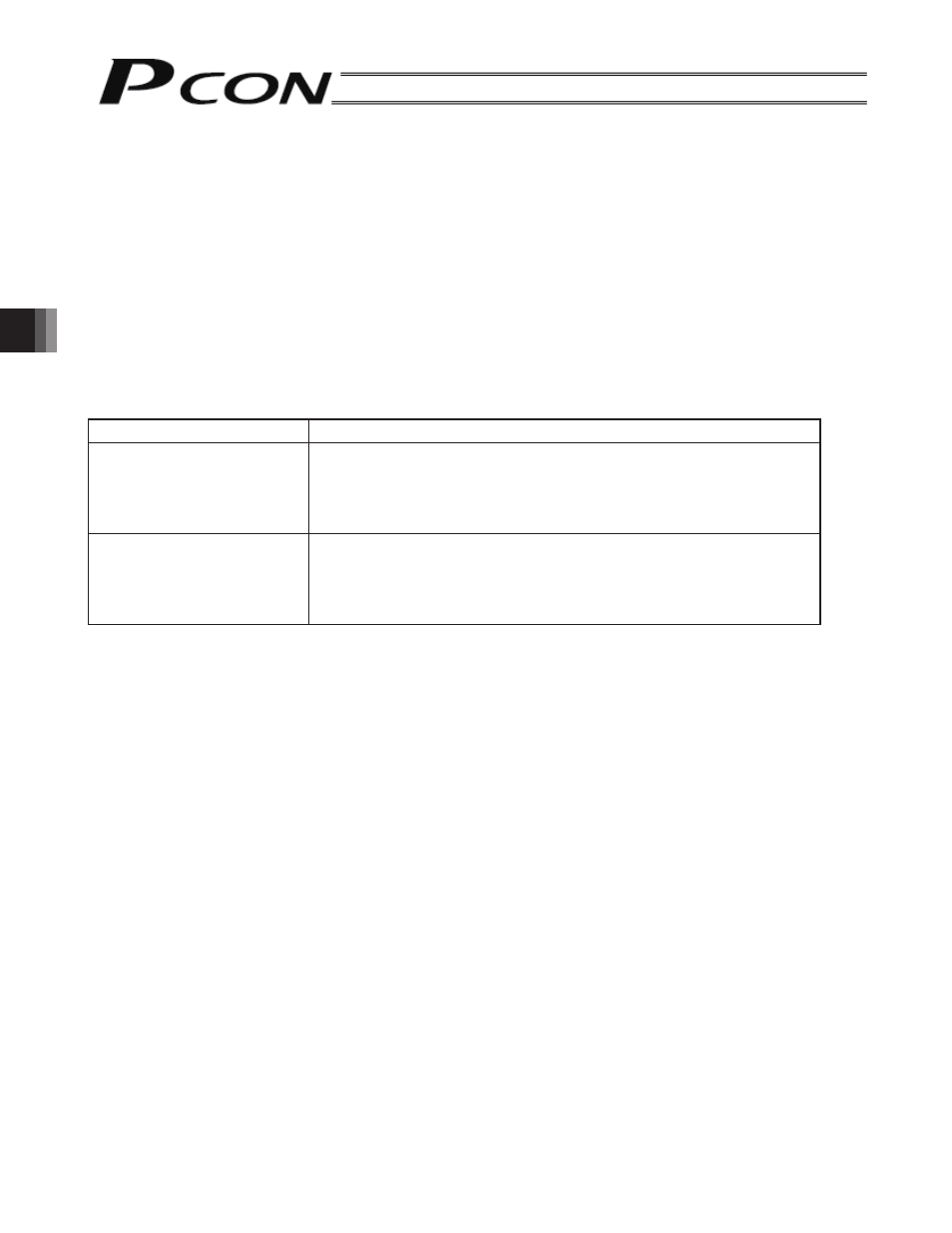
94
5. Parameter Settings
5.2.3
Parameters Relating to the External Interface
• Position complete signal output method (No. 39 FPIO)
Parameter No. 39 defines the condition of the position complete signal when the servo OFF condition or
“deviation” occurs while the actuator has stopped under the positioning completed state.
From the viewpoint of the contents, this parameter is divided into the following two cases:
[1] Where the current position deviates from the set “positioning band” value due to an external force applied
during servo ON
[2] Where the current position deviates from the set “positioning band” value due to an external force applied
during servo OFF
The above is intended to offer flexibility to how the “position complete condition” is monitored in accordance with
the equipment characteristics or the method of building a sequence circuit on the PLC side.
Especially when this parameter is used as is the case with the auto switch of the air cylinder, it is recommended to
set 1 [INP].
The ON/OFF condition of the position complete signal becomes as follows in accordance with the setting in
parameter No. 39:
Setting in Parameter No. 39
Description
0 [PEND]
[1] Servo ON condition
The servo will remain ON even if the current position is outside the
“positioning band” value range set with respect to the target position.
[2] Servo On condition
The servo will be OFF regardless of where the current position is.
1 [INP]
The parameter will be ON if the current position is inside the “positioning
band” value range set with respect to the target position, and will be OFF
if the current position is outside the range, regardless of whether the
servo is ON or OFF.
* It is like an auto switch of the air cylinder.
The factory setting is 0 [PEND].
• Serial communication speed (No. 16 BRSL)
Set the communication speed to be used when the control is performed via serial communication using the PLC’s
communication module.
Set an appropriate value in parameter No. 16 in accordance with the specification of the communication module.
One of 9600, 19200, 38400, 115200, and 230400 bps can be selected as the communication speed.
The factory setting is 38400 [bps].
• Minimum delay time for slave transmitter activation (No. 17 RTIM)
This parameter defines the minimum delay time until the controller’s transmitter will be activated after completion
of command reception, when serial communication is performed using the PLC’s communication module.
The factory setting is 5 msec, but another necessary delay time must be set in parameter No. 17 if the
specification of the communication module exceeds 5 msec.