IAI America PCON-SE User Manual
Page 113
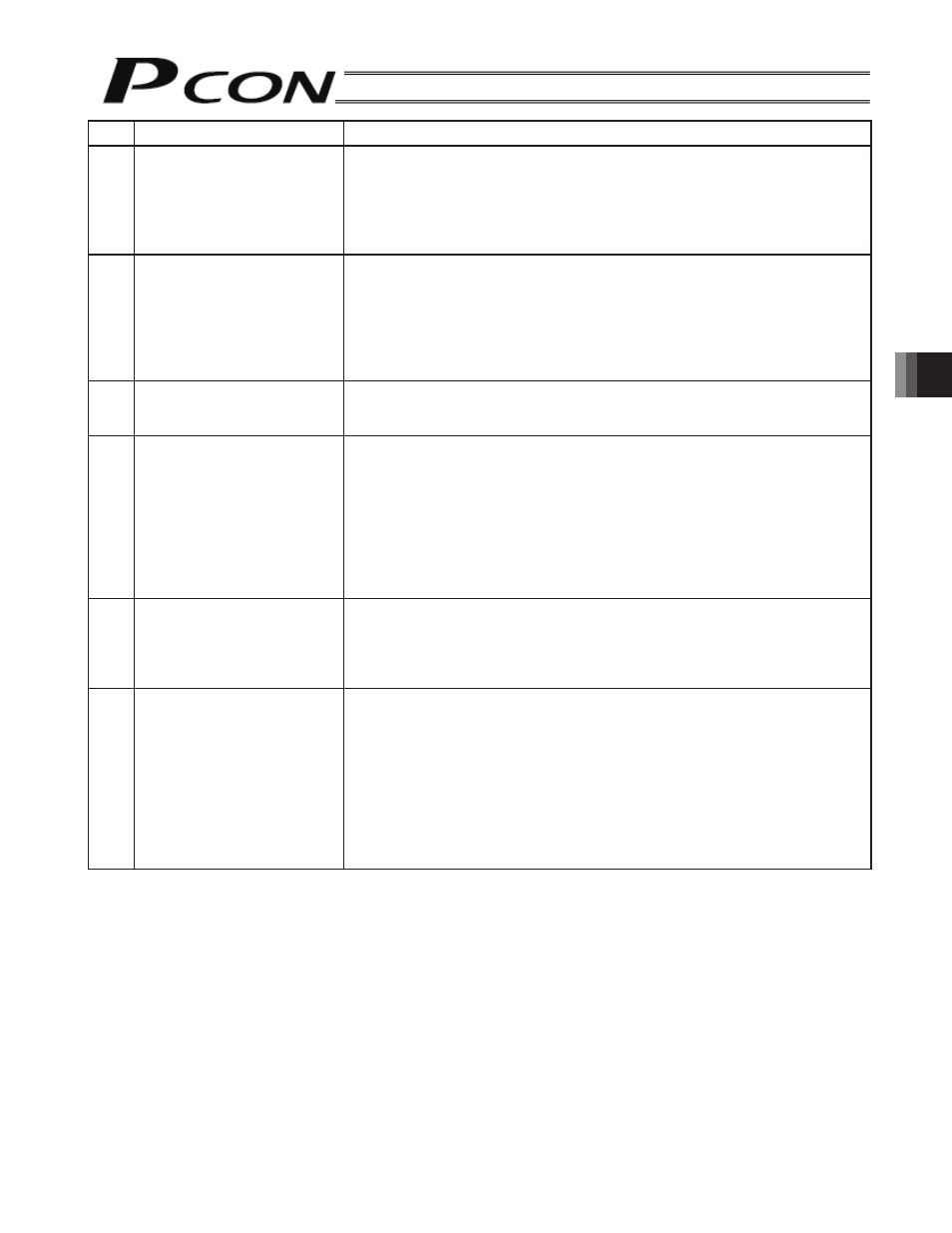
101
6. T
roubleshooting
Code Error
name
Cause/Action
0A1 Parameter data error
Cause: The data input in the parameter area is not in an appropriate range.
(Example) This error generates when there is a clear contradiction
in magnitude correlation such as when 300 mm is
entered by mistake for the value of soft limit- when the
set value of soft limit+ is 200.3 mm.
Action: Change the data to an appropriate value.
0A2 Position data error
Cause: [1] A movement command was issued when no target command
was set in the “Position” field.
[2] The value of the target value in the “Position” field exceeded the
soft limit set value.
Action: [1] Set the target position first.
[2] Change the value of the target position to one within soft limit
set values.
0A3 Position command data error Cause: The speed or acceleration/deceleration value during numeric
specification exceeded the maximum set value.
Action: Change the value to an appropriate one.
0BA Home
sensor
non-detection This
alarm indicates that the actuator with a home sensor used did not
normally complete home return operation.
Cause: [1] Work is interfering with peripheral equipment in the middle of
home return.
[2] The slide resistance of the actuator is locally high.
[3] Installation failure, breakdown or disconnection of the home
check sensor
Action: If the work is not interfering with peripheral equipment, the cause of
[2] or [3] is suspected. Please contact IAI.
0BE Home return timeout
Cause: Home return is not completed within the period set in the applicable
system parameter after the start of home return operation.
(This alarm will not be generated in normal operation.)
Action: The combination of the controller and actuator may be incorrect.
Please contact IAI.
0C0 Excessive actual speed
Cause: This alarm indicates that the motor speed exceeded the maximum
speed set in the applicable system parameter.
This alarm will not be generated in normal operation, but may occur
in the following condition:
[1]
The slide resistance of the actuator is locally high.
[2]
Instantaneous increase in load due to application of external force,
which may cause the load to decrease and actuator to move rapidly
before a servo error is detected.
Action: Check the assembly condition of mechanical parts for abnormality.
If the actuator itself is suspected to be the cause, please contact IAI.