Notes on various calibration methods – HEIDENHAIN iTNC 530 (60642x-04) Cycle programming User Manual
Page 488
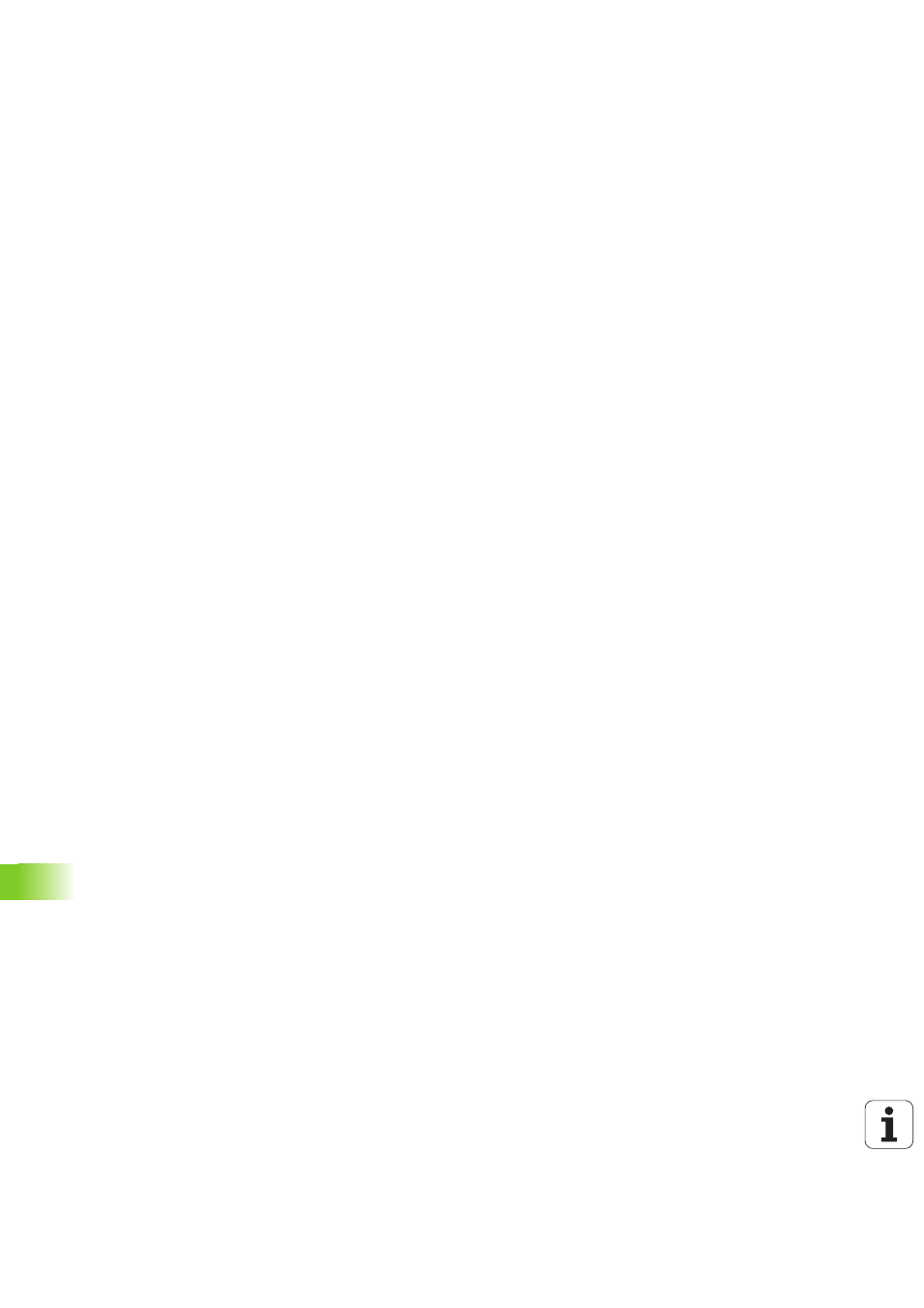
488
Touch Probe Cycles: Automatic Kinematics Measurement
1
8
.4 MEA
S
URE KINEMA
TICS (Cy
c
le 451, DIN/ISO:
G451; Option)
Notes on various calibration methods
Rough optimization during commissioning after entering
approximate dimensions.
Number of measuring points between 1 and 2
Angular step of the rotary axes: Approx. 90°
Fine optimization over the entire range of traverse
Number of measuring points between 3 and 6
The start and end angles should cover the largest possible
traverse range of the rotary axes.
Position the calibration sphere on the machine table so that on
rotary table axes there is a large measuring circle, or so that on
swivel head axes the measurement can be made at a
representative position (e.g. in the center of the traverse range).
Optimization of a specific rotary axis position
Number of measuring points between 2 and 3
The measurements are made near the rotary axis angle at which
the workpiece is to be machined.
Position the calibration sphere on the machine table for calibration
at the position subsequently intended for machining.
Inspecting the machine accuracy
Number of measuring points between 4 and 8
The start and end angles should cover the largest possible
traverse range of the rotary axes.
Determination of the rotary axis backlash
Number of measuring points between 8 and 12
The start and end angles should cover the largest possible
traverse range of the rotary axes.