Tool-tip radius compensation (trc), Milling cutter radius compensation (mcrc), 8 tool dimensions – HEIDENHAIN SW 68894x-02 User Manual
Page 48
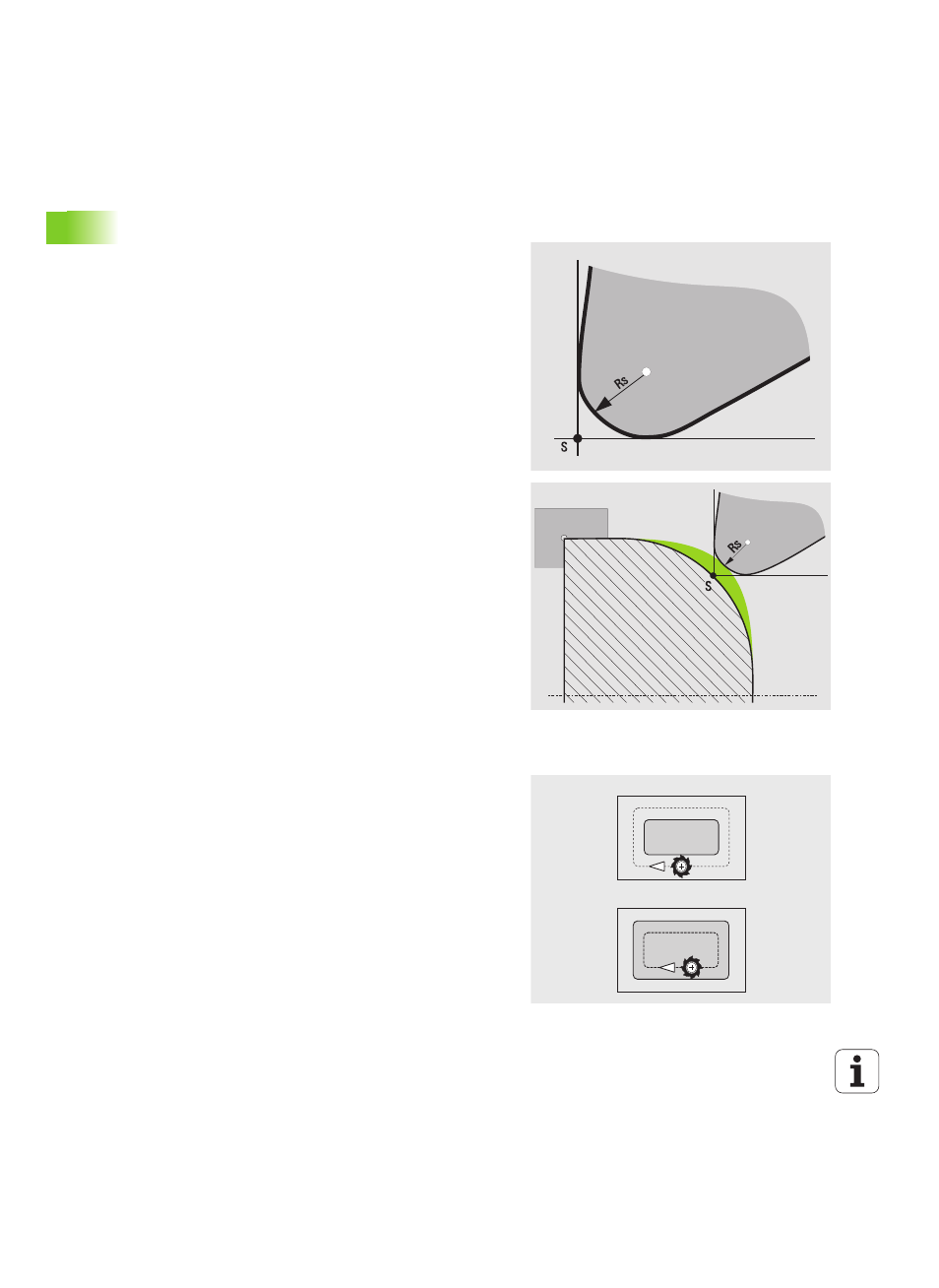
48
Introduction and fundamentals
1.
8
Tool
dimensions
Tool-tip radius compensation (TRC)
The tip of a lathe tool has a certain radius. When machining tapers,
chamfers and radii, this results in inaccuracies which the CNC PILOT
compensates with its cutting radius compensation function.
Programmed paths of traverse are referenced to the theoretical tool
tip S. With non-paraxial contours, this will lead to inaccuracies during
machining.
The TRC function compensates for this error by calculating a new path
of traverse, the equidistant line (see figure).
The CNC PILOT calculates the TRC for cycle programming. The
smart.Turn and DIN programming feature also takes the TRC for
clearance cycles into account. During DIN programming with single
paths, you can also enable/disable TRC.
Milling cutter radius compensation (MCRC)
In milling operations, the outside diameter of the milling cutter
determines the contour. When the MCRC function is not active, the
system defines the center of the cutter as reference point. The TRC
function compensates for this error by calculating a new path of
traverse, the equidistant line.