7 fundamentals, Position encoders and reference marks, Axis designations – HEIDENHAIN SW 68894x-02 User Manual
Page 43: 7 fundamentals 1.7 fundamentals
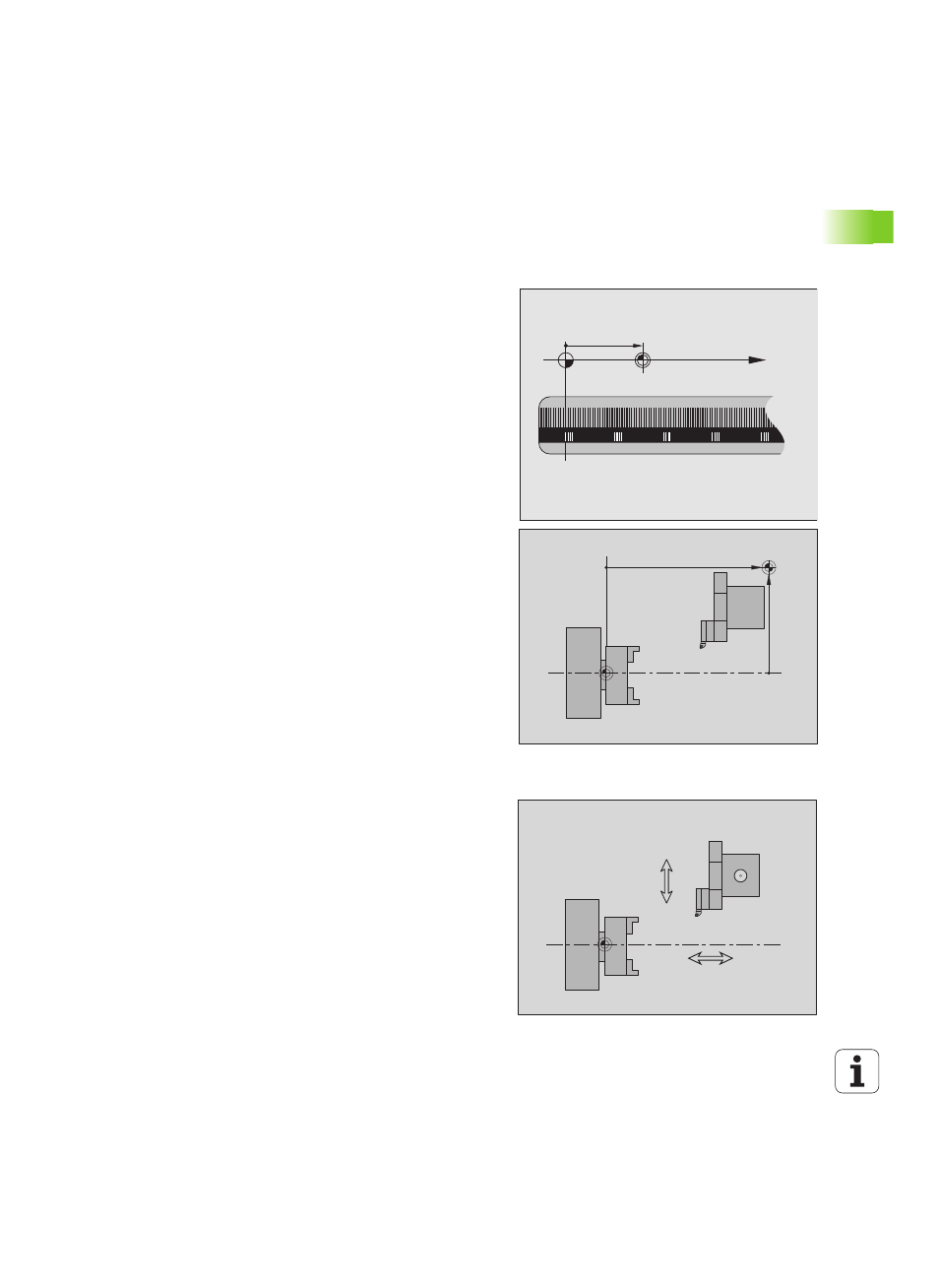
HEIDENHAIN CNC PILOT 640
43
1.
7
Fundamentals
1.7 Fundamentals
Position encoders and reference marks
The machine axes are equipped with position encoders that register
the positions of the slide or tool. When a machine axis moves, the
corresponding position encoder generates an electrical signal. The
control evaluates this signal and calculates the precise actual position
of the machine axis.
If there is a power interruption, the calculated position will no longer
correspond to the actual position of the machine slide. To recover this
association, incremental position encoders are provided with
reference marks. The scales of the position encoders contain one or
more reference marks that transmit a signal to the control when they
are crossed over. This enables the CNC PILOT to re-establish the
assignment of the displayed position to the current machine position.
For linear encoders with distance-coded reference marks, you only
need to move each axis a maximum of 20 mm (0.8 in.) for these, and
a maximum of 20° for angle encoders.
If incremental encoders are without reference marks, fixed reference
positions have to be traversed after switch-on. The control knows the
exact distance between these reference points and the machine
datum (see figure).
With absolute encoders, an absolute position value is transmitted to
the control immediately upon switch-on. In this way the assignment
of the actual position to the machine slide position is re-established
directly after switch-on.
Axis designations
The cross slide is referred to as the X axis and the saddle as the Z
axis.
All X-axis values that are displayed or entered are regarded as
diameters.
Lathes with Y axis: The Y axis is perpendicular to the X axis and Z axis
(Cartesian system).
When programming paths of traverse, remember to:
Program a positive value to depart the workpiece.
Program a negative value to approach the workpiece.
X (Z,Y)
X
MP
Zref
Xref
M
M
Z
Z+
Y+
X
X+