AMETEK ASD Series User Manual
Page 67
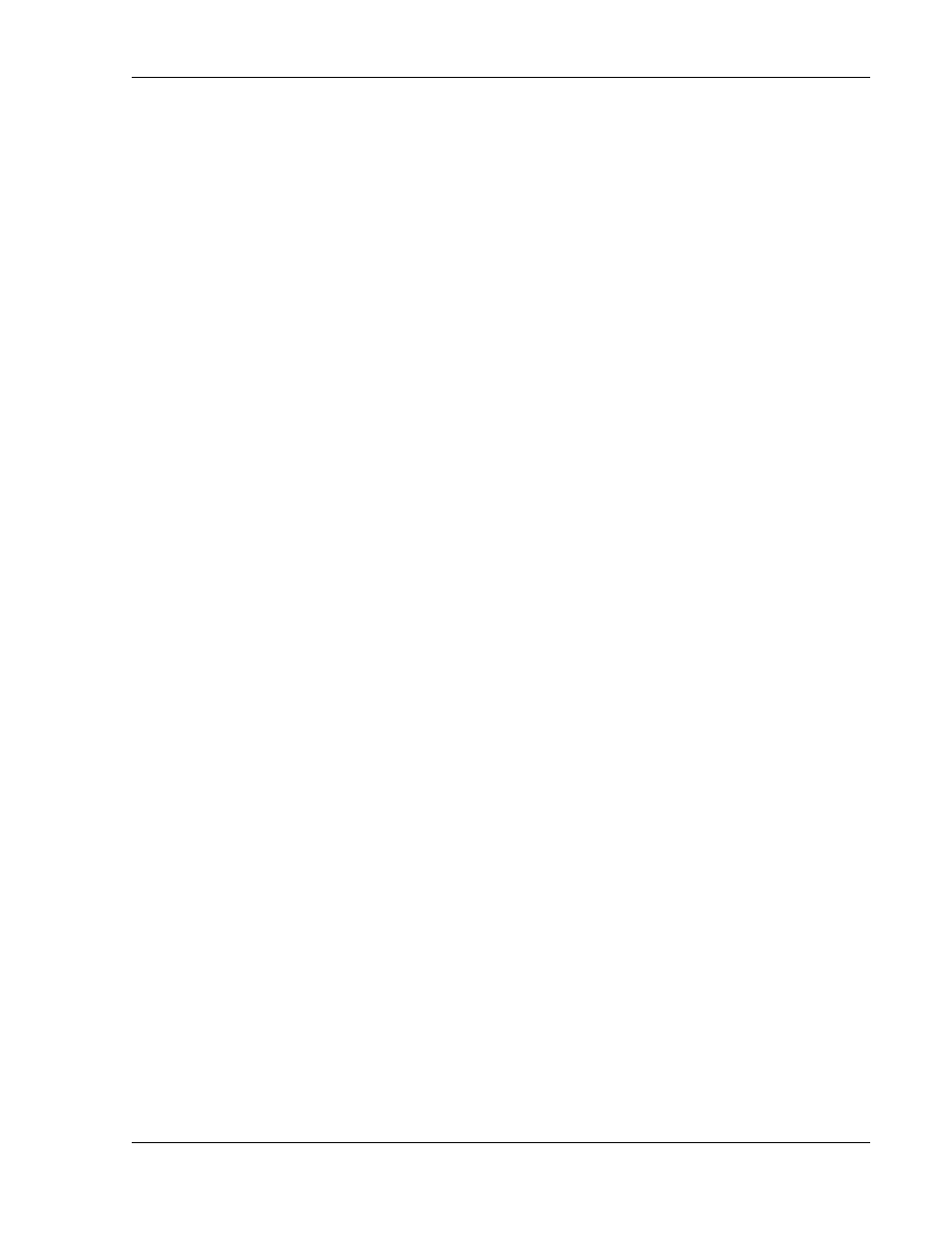
Sorensen ASD Series
Programming: Digital Interface Control
M551177-01 Rev A
4-9
4.3.7 PROGRAMMABLE FAULT BEHAVIOR
Fault behavior can be programmed to either report a specific fault and
shut down the power supply output, or report the fault and continue
running
the
power
supply
output.
A
32-bit
register
called
“Fault_Shutdown_Config_HI/LO” defines this behavior. See Table 4-11 for
bit descriptions of the Fault Bits Register.
If a given bit is set to “1”, this means that the particular fault described in
the “Fault_Bits register bit description” will produce a unit shut down.
Some faults are not editable and will always produce a unit shut down
(writing zeros does not change their behavior), because they are related
to hard faults that may affect the integrity of the system.
4.3.8 EXTERNAL PROCESS CONTROL
ASD power supplies have the capability of controlling external variables,
such as temperature or pressure, by using an internal PID compensator
and an analog input for the feedback. Figure 4-1 shows a block diagram of
an ASD unit controlling an external process. The main parts are:
Feedback
The feedback of the controlled variable comes from the external
process and is fed to the ASD controller by using one of the
analog inputs (the power programming input). With the right
transducer, any external variable can be controlled by the power
supply, such as temperature, pressure, current, voltage,
position, etc. The only requirement is that the transducer has to
produce an analog signal compatible with the analog inputs of
the ASD interface (0-10V or 4-20mA).
Setpoint
The setpoint of the process controller can be taken from the
digital interface (Psetpoint register) or from the analog interface
(Vprog input), depending on the configuration in the
“Process_config” register. See Table 4-7 for more details.
Compensator
The calculated error between the setpoint and the feedback
feeds a compensator, which is implemented as a discrete 2-pole
2-zero stage. The most common way to calculate these
coefficient is starting from a PID (proportional-integral-
derivative) stage, and calculating the 2-pole 2-zero coefficients
based on it. The five coefficients (Process_coef_0 thru 4) can
be programmed by using write registers 51 to 60 (see Table
4-4). The compensator is executed by the master controller at a
sampling rate of 125Hz. The feedback and setpoint variables
have a range of 0 to 1.0.
Command
The compensator generates a command that can be configured
to control the output voltage or current of the power supply. This
is configured by a bit in the “Process_config” register. See Table
4-7 for more details.