Electronic gear ratio output section, Electronic gear ratio – Rockwell Automation 20D PowerFlex 700S AC Drives with Phase II Control Reference Manual User Manual
Page 83
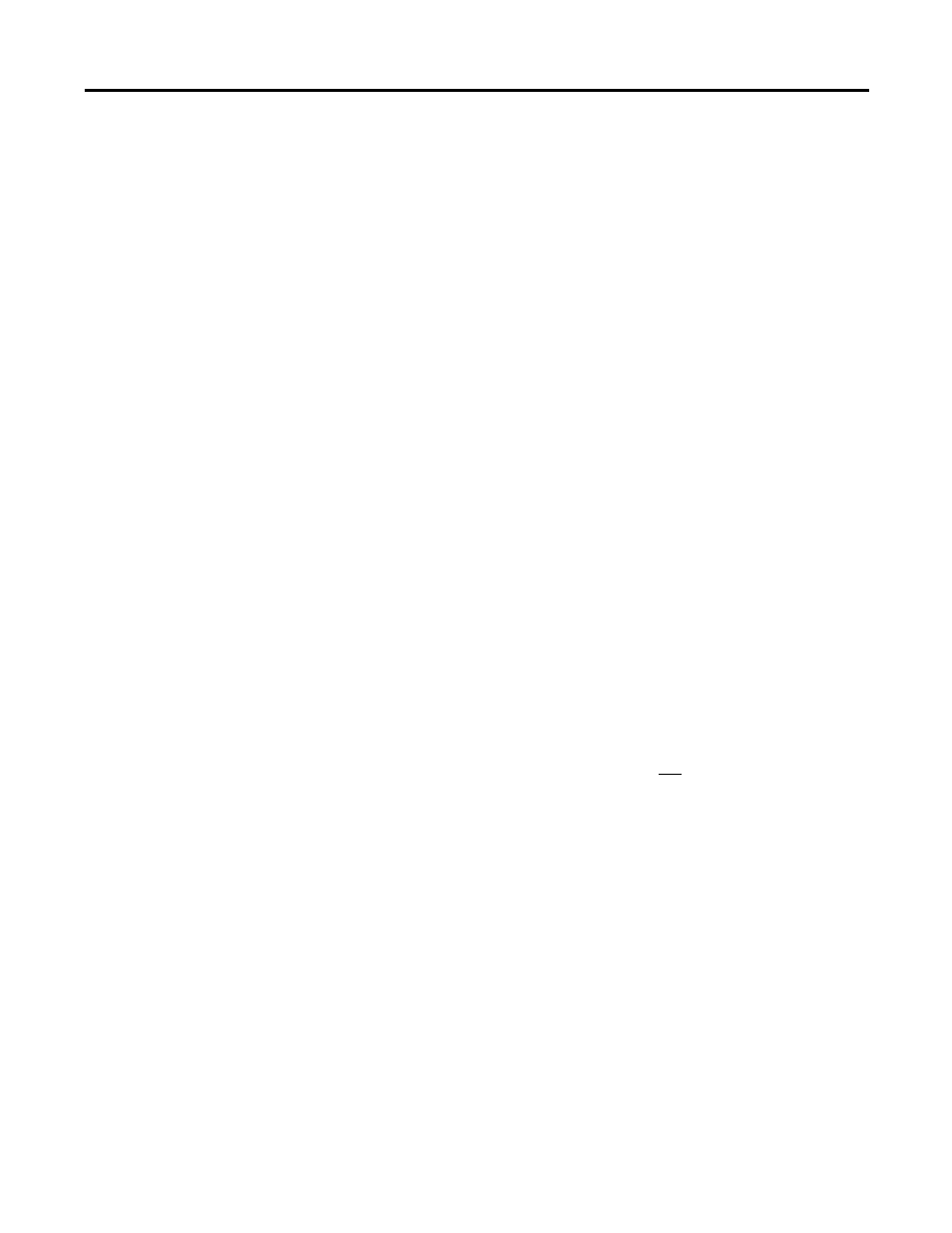
Rockwell Automation Publication PFLEX-RM003E-EN-E - January 2011
83
Detailed Drive Operation Chapter 1
Base RPM Scaling
The PLL, in addition to providing position reference, provides a speed reference
to the drive as a feed forward. This is normal operating practice to secure zero
position error and optimal tracking of the follower drive. The RPM setting in
parameter 727 [PLL VirtEncdrRPM] determines 1 per unit speed output from
the PLL. The setting should be logical, i.e. represent either base line speed or base
motor speed.
Counts Per Revolution
Parameter 726 [PLL EPR Output] sets the output counts per revolution. This
can be any value with the stipulation that is compatible with the slave drives’
feedback resolution. In general, resolution will not decrease as long as the EGR
ratio is less than 1. It is better to allow the PLL to generate a high encoder count
than to use a ratio to make up the difference in the slave drive.
Electronic Gear Ratio
The EGR is used to scale the PLL input to the PLL output.
Parameters 723 [PLL Rev Input] and 724 [PLL Rev Output] set the ratio
between the number of revolutions of the input encoder to the desired number of
revolutions of the PLL output. The [PLL Rev Input] and [PLL Rev Output]
parameters are Dint values and should typically be reduced to the least common
integer.
The encoder EPR value set in parameter 725 [PLL EPR Input] must be specified
for the feedback device used. Parameter 726 [PLL EPR Output] sets the output
counts per revolution. These parameters should not be reduced to the least
common integer.
The drive internally multiplies [PLL Rev Input] by [PLL EPR Input] to calculate
the EGR numerator. The drive multiplies [PLL Rev Output] by [PLL EPR
Output] to calculate the EGR denominator.
Output Section
Parameter 731 [PLL Posit Out] should be linked to the position reference in the
local drive. The local drive implements the PLL and transmits the PLL data over
SynchLink to the other drives. Parameter 734 [PLL Speed Out] should be linked
to the speed reference in the master drive.
Parameter 732 [PLL Posit OutAdv] provides a position reference that is
advanced by one scan time of the drive’s control loop. The value of [PLL Posit
OutAdv] should be sent over SynchLink to the follower drives and linked into