Integral gain droop speed regulator output limits, Integral gain, Droop – Rockwell Automation 20D PowerFlex 700S AC Drives with Phase II Control Reference Manual User Manual
Page 157: Speed regulator output limits
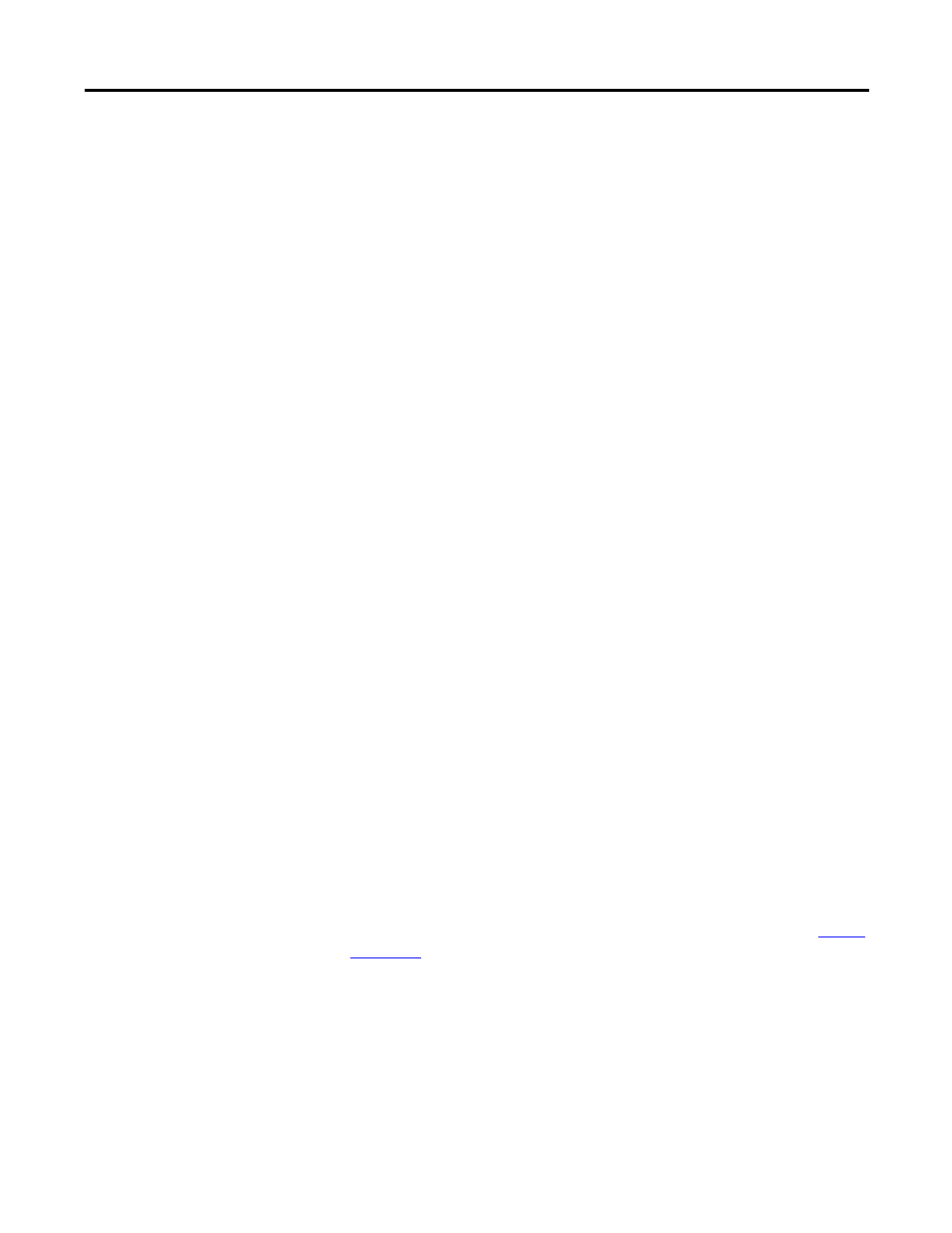
Rockwell Automation Publication PFLEX-RM003E-EN-E - January 2011
157
Detailed Drive Operation Chapter 1
Integral Gain
The speed droop is subtracted from the filtered speed error (after the servo lock is
added and the anti-backup is subtracted). This signal is then sent to the integral
gain block. The integral gain block outputs a torque command relative to the
error integrated over a period of time.
Parameter 82 [Spd Reg I Gain] sets the integral gain of the speed regulator. It's
value is automatically calculated based on the bandwidth setting in [Spd Reg
BW] and the inertia of the system in [Total Inertia]. Integral gain may be
manually adjusted by setting [Spd Reg BW] to a value of zero. Units are (per unit
torque/sec) / (per unit speed). For example, when [Spd Reg I Gain] is 50 and the
speed error is 1%, the integral output will integrate from 0 to 50% motor rated
torque in 1 second.
When parameter 153 [Control Options], bit 12 “Jog-NoInteg” is turned on, this
tells the speed regulator not to use the integral gain during jog commands.
When parameter 151 [Logic Command], bit 5 “SReg IntgHld” is turned on, the
Integrator holds its output at the present level until the bit is turned off again.
When parameter 151 [Logic Command], bit 6 “SReg IntgRst” is turned on, the
output of the integrator is set to 0. When bit 6 is turned back off, the integrator
output starts integrating up again from 0.
When parameter 153 [Control Options], bit 18 “SpdRegPreset” is turned on, the
value in parameter 303 [Motor Torque Ref ] is added to the integrator output.
When bit 18 “SpdRegPreset” is turned off, parameter 87 [SReg Trq Preset]
(default of 0 per unit) is added to the integrator output.
Parameter 101 [SpdReg Integ Out] contains the value of the torque output from
the integrator. This parameter is in per unit so that a value of 1 equals rated motor
torque.
Droop
Droop is used to “shed” load and is usually used when a soft coupling of two
motors is present in an application. For more information on droop, see
Speed Regulator Output Limits
The outputs from the proportional block and integrator block are summed
together, creating a torque reference. This torque reference is limited by
parameter 102 [Spd Reg Pos Lim] and parameter 103 [Spd Reg Neg Lim].