Speed pi regulator, Speed trim – Rockwell Automation 20D PowerFlex 700S AC Drives with Phase II Control Reference Manual User Manual
Page 152
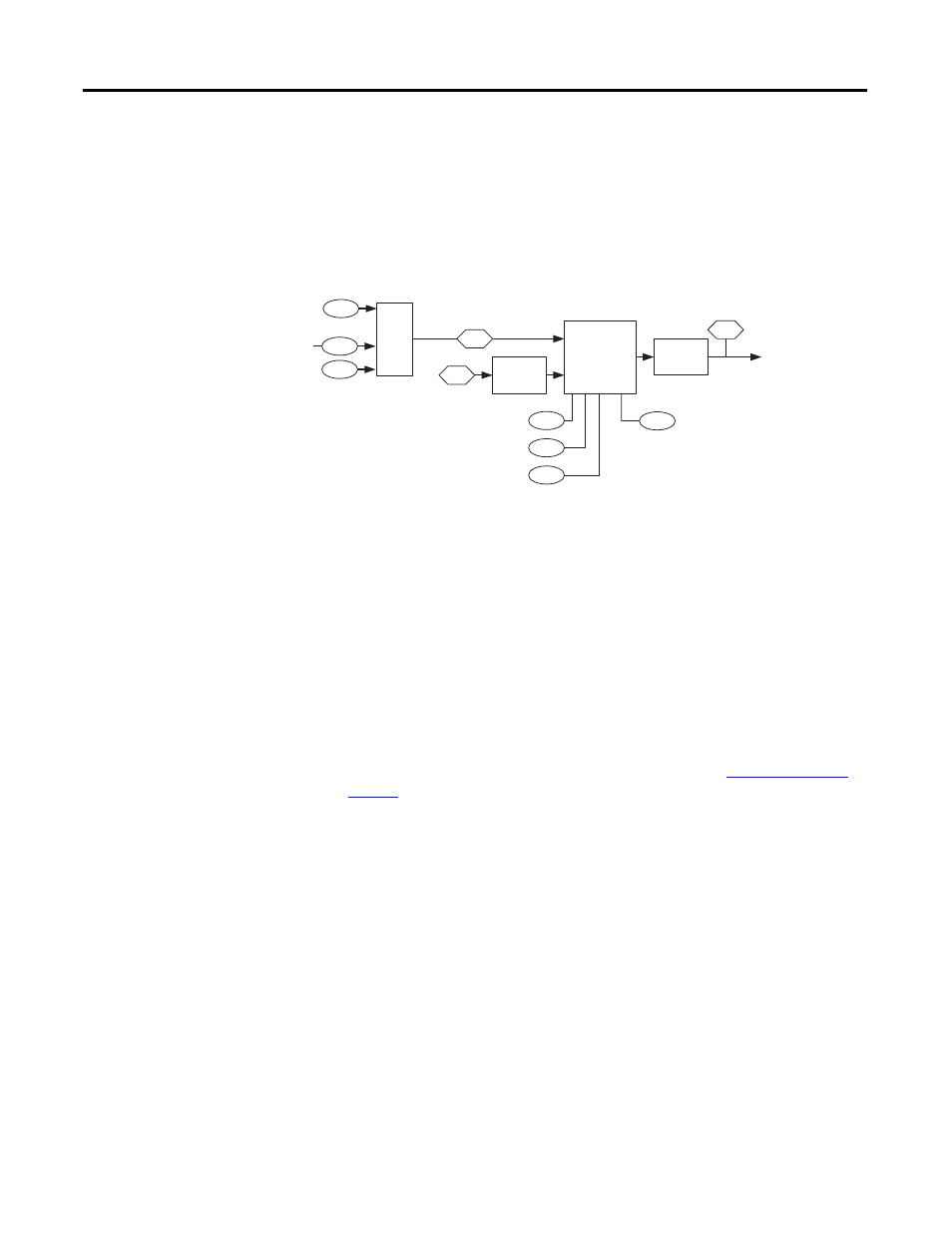
152
Rockwell Automation Publication PFLEX-RM003E-EN-E - January 2011
Chapter 1 Detailed Drive Operation
Speed PI Regulator
The drive takes the speed reference specified by the speed reference control loop
and compares it to the speed feedback. The speed regulator uses proportional and
integral gains to adjust the torque reference sent to the motor. This torque
reference attempts to operate the motor at the specified speed. This regulator also
produces a high bandwidth response to speed command and load changes.
Figure 24 - Overview of the Speed PI Regulator Loop
The main purpose of the speed PI regulator is to produce a torque reference for
the current regulator block. The following sections describe each portion of the
speed PI regulator.
Speed Trim
The speed trim blocks are used to sum the speed reference from the speed
reference control loop with speed trim values from other sources.
Parameter 22 [Speed Trim 2] provides a trim value with a lead/lag filter. By
default, it is linked to the output of the position loop (parameter 318 [Posit Spd
Output]). For more information on lead/lag filters refer to
.
Parameter 23 [Speed Trim 3] provides a scalable speed trim value. The speed
reference value for [Speed Trim 3] is multiplied by the scaling parameter 24
[SpdTrim 3 Scale]. [SpdTrim 3 Scale] is a linkable parameter. This allows speed
trim 3 to be scaled “dynamically” with an input signal if desired. An example
would be to have an analog input linked to the scale parameter. The speed trim
and the scale would then affect the value sent to the summation block.
PI Regulator
81
82
Lead Lag
Lead Lag
300
Motor Spd Fdbk
302
Spd Reg PI Out
To
Torque Control
Motor Speed Ref
90
301
+
22
23
48
Speed Trim 3
Speed Trim 2
Spd Ref Bypass2
From
Speed Ref
86
Spd Reg Droop
Spd Reg P Gain
Spd Reg I Gain
Spd Reg BW