Warning – SkyTrak 6036 Service Manual User Manual
Page 205
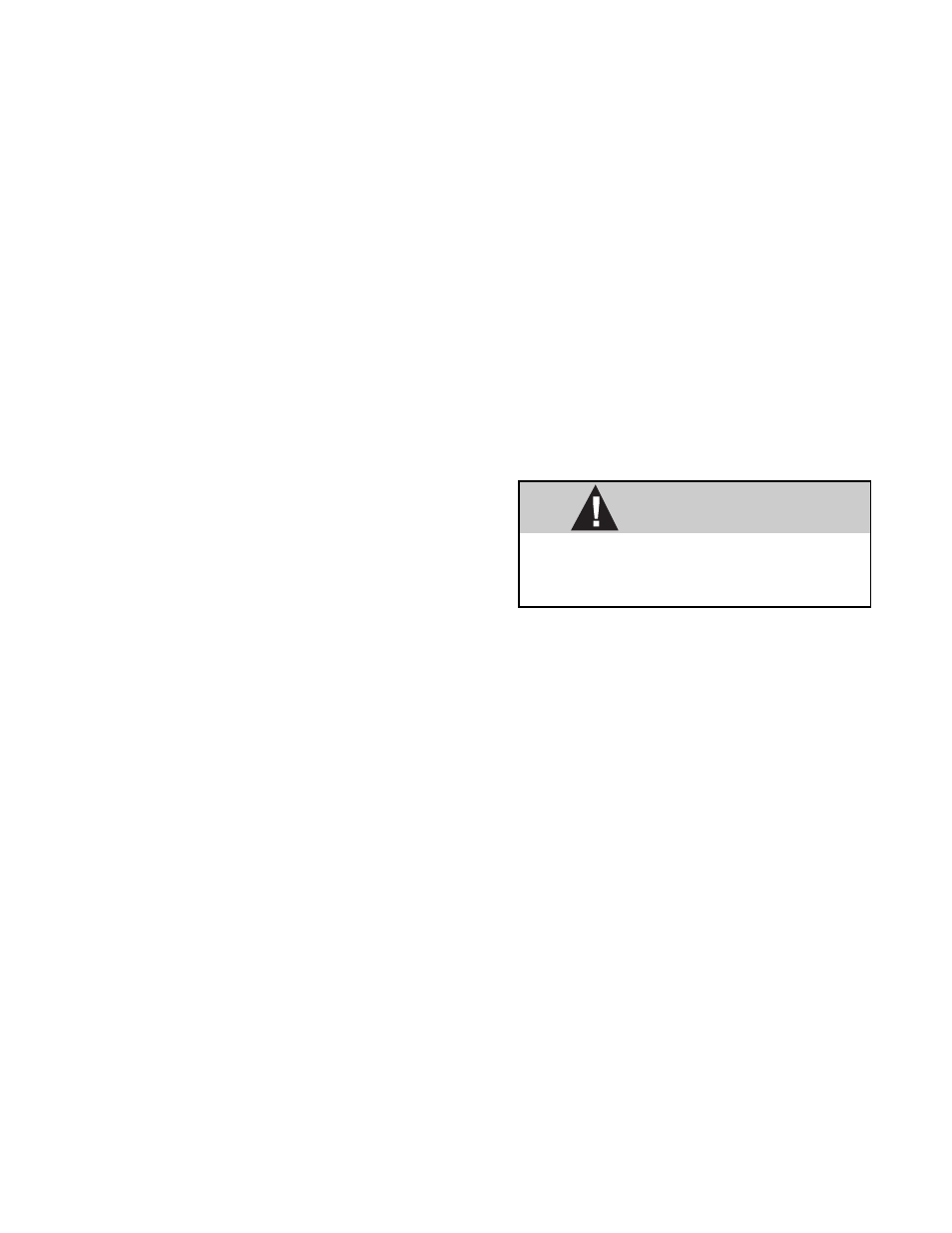
Section 9
Hydraulic System
Model 6036/6036T S/N 9B0500 thru 14833
9-55
NOTE: The wiper lip should be toward the outer
end of the gland and seal lips toward the inner end
of the gland. Use tools that will not damage the
seals. If the backup ring is not flat on both sides,
the side with the arc must be toward the O-ring.
3.
Fasten the eye of the rod in a soft-jawed vise
and put a padded support below the other end
of the rod to prevent damage to the rod.
4.
Push the assembled gland onto the rod (13).
If necessary, use a soft hammer to drive the
gland onto the rod.
5.
Install new O-ring (6) inside of the piston (5).
6.
Install the piston on rod.
7.
Apply Loctite
®
Primer T and Threadlocker
271
to the nut (2) in accordance with the manufac-
turer’s instructions. Install the nut on the rod
and torque to 400 to 450 lb-ft (542 to 610 Nm).
Stake the nut in four places.
8.
Install a new piston seal (7) on the piston.
9.
Fasten the cylinder tube (3) in a soft-jawed
vise or other acceptable holding equipment.
Be careful not to damage the tube.
10. Lubricate the inside of the tube, piston, and
gland O-ring (9) with clean hydraulic oil.
11. Apply a compression sleeve or other suitable
tool to the gland in order to compress the O-
ring (9) on the gland. Insert the assembled
piston, rod and the gland into the tube (3).
Remove the compression tool. Using a pin
spanner wrench, thread the gland into the
tube.
IMPORTANT: When sliding the rod and piston
assembly into the tube, be careful so that gland
threads in the tube do not damage the piston seal.
Keep the rod in line with the tube barrel to prevent
binding.
12. Install new O-rings (15) and backup rings (16)
on check valves (1). Use new valves if either
valve was removed for replacement. Lubri-
cate outside of the valves with clean filtered
hydraulic oil. Install the valves and torque to
30 to 35 lb-ft (40,7 to 47,5 Nm).
13. If removed, install plugs (2) and grease fittings
(14).
14. Following reassembly, test the cylinder at low
operating pressure (100 psi or 6,9 bar) to be
sure the piston and rod are moving freely in
both directions.
15. Increase the operating pressure to the maxi-
mum (4000 psi or 275 bar) for the cylinder and
check for external leakage and free movement
in both directions.
16. Prepare the cylinder for installation by retract-
ing the piston and capping or plugging the
ports.
f.
Installation
1.
Lubricate the frame tilt cylinder pivot pins with
multi-purpose lithium-based grease
2.
Using suitable lifting device, install the frame
tilt cylinder, Fig. 9.18, on the forklift securing
the rod end to the axle mounting block with
pivot pin and snap rings.
3.
Remove all plugs or caps from the hydraulic
lines and securely tighten the lines to the
cylinder.
Before starting the engine be sure all hydraulic
connections are tight and all tools are removed
from the forklift.
Warning
4.
Have a helper start the forklift engine.
5.
Position the frame tilt cylinder so that the base
end is aligned with the rod end mounting holes
in the frame as much as possible.
6.
Instruct the operator to extend or retract the
frame tilt cylinder slowly until the base end eye
is aligned with the frame mounting holes.
Secure the base end to the frame with pivot
pin and snap rings.
7.
Remove blocking from between axle and
frame.
8.
Using the fork and frame tilt control lever, tilt
the frame full right, then full left at least five
complete cycles or until operation of the frame
tilt circuit is normal (no jerking or spongy
feeling).
9.
Shut down the engine. Check the hydraulic oil
level and fill as described in the Owners/
Operators Manual.
10. Test frame tilt circuit operation as described in
paragraph 9.4.3.c.