Warning – SkyTrak 6036 Service Manual User Manual
Page 194
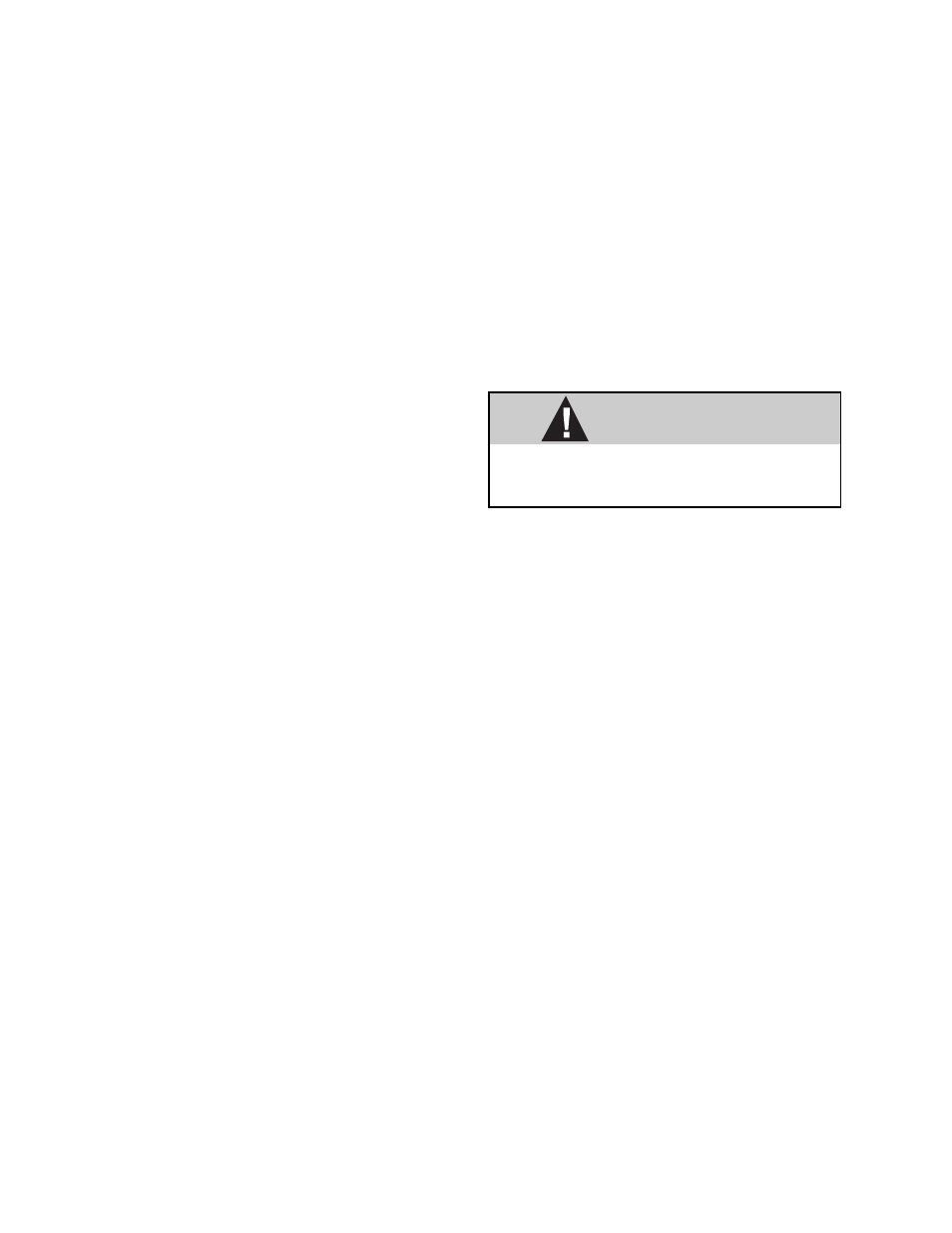
Section 9
Hydraulic System
9-44
Model 6036/6036T S/N 9B0500 thru 14833
Before starting the engine be sure all hydraulic
connections are tight and all tools are removed
from the forklift.
Warning
3.
Slide the assembled gland and seals onto the
rod. If necessary, use a soft hammer to drive
the gland on the rod.
4.
Slide the stop tube (9) onto the rod.
5.
Install new O-ring (8) inside internal groove on
inside of piston.
6.
Apply Loctite
®
Primer T and compound 609 to
inside threads of piston in accordance with
manufacturer's instructions. Carefully screw
piston completely onto rod.
7.
Apply Loctite
®
Threadlocker 242 to setscrews
(6 and 7) and install them in the piston.
8.
Install O-ring (8) inside the internal groove of
the stop tube and slide stop tube (9) down the
rod and against the piston.
9.
Install new piston seal (4) on piston.
10. Fasten cylinder tube (13) in a soft-jawed vise
or other acceptable holding equipment.
11. If removed, install two plugs (16) in the bottom
of the cylinder tube.
12. Lubricate inside of the tube and outside of the
piston and gland with clean hydraulic oil.
13. Apply a compression sleeve or other suitable
tool to the gland and piston in order to com-
press O-rings, backup rings and seals while
inserting the assembled piston, rod and gland
into the tube (13). Remove the compression
tool. Using a pin spanner wrench, thread the
gland into tube.
IMPORTANT: When sliding the rod and piston
assembly in the tube, be careful so that head
threads in the tube do not damage the piston seal.
Keep the rod in line with the tube barrel to prevent
binding.
14. Install new O-rings (18) and backup rings (19)
on the counterbalance valve (14) and pilot
check valve (15). Use new valves if either or
both valves were removed for replacement.
Lubricate outside of the valves with clean
filtered hydraulic oil. Install the valves and
torque them to 45 lb-ft (61,2 Nm).
15. Following reassembly, test the cylinder at low
operating pressure (100 psi or 6,9 bar) to be
sure the piston and rod are moving freely in
both directions.
16. Increase the operating pressure to the maxi-
mum (4000 psi or 275 bar) for the cylinder and
check for external leakage and free movement
in both directions.
17. Prepare the cylinder for installation by retract-
ing the piston and capping and plugging the
ports.
b. Installation
1.
Using suitable lifting device, install the boom
extend cylinder, Fig. 9.21, on the forklift
securing the base end of the extend cylinder
to the outer boom with a pin and retaining
rings and the rod end through the anti-buckle
bar.
2.
Remove all plugs or caps from the hydraulic
lines and securely tighten the lines to the
cylinder.
3.
Have a helper start the forklift engine.
4.
Position the extend cylinder so that the rod is
aligned with the rod end mounting holes as
much as possible.
5.
Instruct the operator to extend or retract the
cylinder slowly until the rod end eye is aligned
with the intermediate boom mounting holes.
Secure the rod end to the boom with pin and
retaining rings.
6.
Extend the boom as far as it will go; then the
retract it as far as it will go five times or until
the operation of the boom extend cylinder is
normal (no jerks or spongy feel).
7.
Shut down the engine. Check the hydraulic oil
level and fill as described in the Owners/
Operators Manual.
8.
Test boom extend/retract circuit operation as
described in paragraph 9.2.3.c.
9.5.6 “BHE” Boom Extend Cylinder
a.
Disassembly
1.
Remove all dirt and grease from the cylinder.
2.
Fasten the cylinder in a soft-jawed vise or
other acceptable holding equipment. Do not
damage the tube.
3.
Remove the counterbalance valve (19, Fig.
9.23), pilot check valve (20) and related O-
rings and backup rings (seal kits) from the
tube (16).