Sitrans p measuring instruments for pressure – Siemens SITRANS P User Manual
Page 30
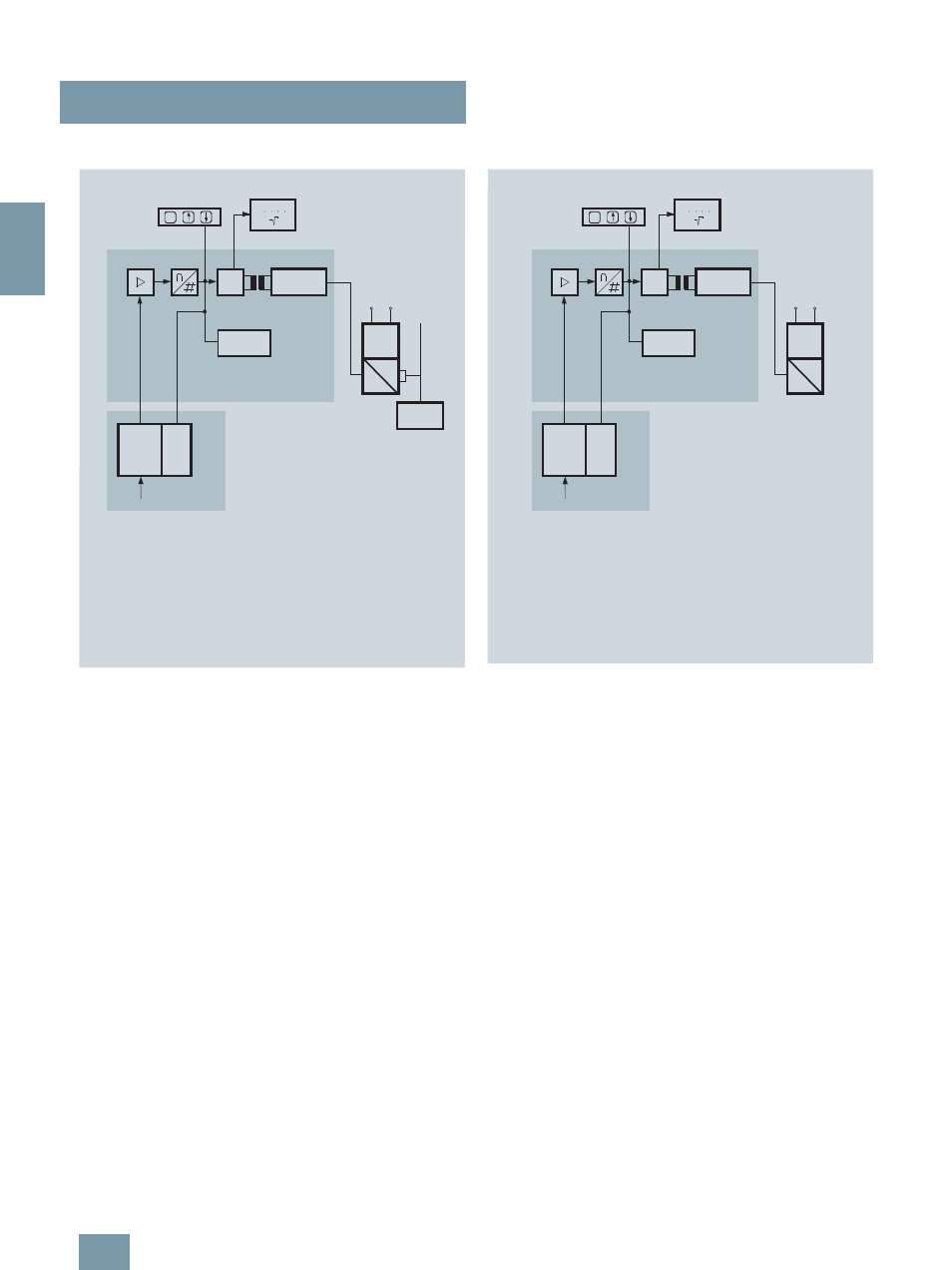
SITRANS P measuring instruments for pressure
Transmitters for food, pharmaceuticals and biotechnology
SITRANS P300 for gage and absolute pressure
2/30
Siemens FI 01 · 2009
2
Operation of the electronics with PROFIBUS PA communica-
tion
Function diagram of electronics
The input pressure is converted into an electrical signal by the
sensor (1). This signal is amplified by the measuring amplifier (2)
and digitalized in an analog to digital converter (3). The digital
signal is analyzed in a microcontroller (4) and corrected with re-
gard to linearity and thermal characteristics. It is then made
available at the PROFIBUS PA over an electrically isolated
PROFIBUS PA interface (7). The data specific to the measuring
cell, the electronic data and parameter settings are stored in two
non-volatile memories (6). The first memory is linked with the
measuring cell, the second with the electronics.
The buttons (8) can be used to call up individual functions, so-
called modes. If you have a device with a digital display (9), you
can use this to track mode settings and other messages. The ba-
sic mode settings can be changed with a computer over the bus
master (12).
Mode of operation of the FOUNDATION Fieldbus
electronics
Function diagram of electronics
The bridge output voltage created by the sensor (1, Figure
"Function diagram of electronics") is amplified by the instrument
amplifier (2) and digitized in the analog-to-digital converter (3).
The digital information is evaluated in the microcontroller, its lin-
earity and temperature response corrected, and provided on the
FOUNDATION Fieldbus through an electrically isolated
FOUNDATION Fieldbus Interface (7).
The data specific to the measuring cell, the electronics data, and
the parameter data are stored in the two non-volatile memories
(6). The one memory is coupled to the measuring cell, the other
to the electronics. As the result of this modular design, the elec-
tronics and the measuring cell can be replaced separately from
each other.
Using the three input keys (8) you can parameterize the pressure
transmitter directly at the point of measurement. The input keys
can also be used to control the view of the results, the error mes-
sages and the operating modes on the digital display (9).
The results with status values and diagnostic values are trans-
ferred by cyclic data transmission on the FOUNDATION
Fieldbus. Parameterization data and error messages are trans-
ferred by acyclic data transmission. Special software such as
National Instruments Configurator is required for this.
Mode of operation of the measuring cells
The process connections available include the following:
• G½
• ½-14 NPT
• Front-flush diaphragm:
- Flanges to EN
- Flanges to ASME
- NuG and pharmaceutical connections
6
8
pe
1
2
C
m
M
0 0 00 0
0 0
EEPROM
EEPROM
9
6
3
4
5
7
10
12
11
1
Measuring cell sensor
2
Instrument amplifier
3
Analog-to-digital converter
4
Microcontroller
5
Electrical isolation
6
One non-volatile memory
each in the measuring cell
and electronics
7
PROFIBUS-PA interface
Sensor
Electronics
Measuring cell
PA
interface
Bus-
Master
Power
supply
unit
Coup-
ler
Power supply
PROF
IBU
S-DP
PROF
IBU
S-PA
8
Three input keys
(local operation)
9
Digital display
10 Power supply
11 DP/PA coupler or link
12 Bus master
p
e
Input variable
6
8
pe
1
2
C
m
M
0 0 00 0
0 0
EEPROM
EEPROM
9
6
3
4
5
7
10
1
Measuring cell sensor
2
Instrument amplifier
3
Analog-to-digital converter
4
Microcontroller
5
Electrical isolation
6
One non-volatile memory
each in the measuring cell
and electronics
7
FF interface
Sensor
Electronics
Measuring cell
FF
interface
Power
supply
unit
Coup-
ler
Power supply
8
Three input keys
(local operation)
9
Digital display
10 Power supply
p
e
Input variable
© Siemens AG 2008