Sitrans p measuring instruments for pressure, Remote seals for transmitters and pressure gages, Technical description 2/156 – Siemens SITRANS P User Manual
Page 156
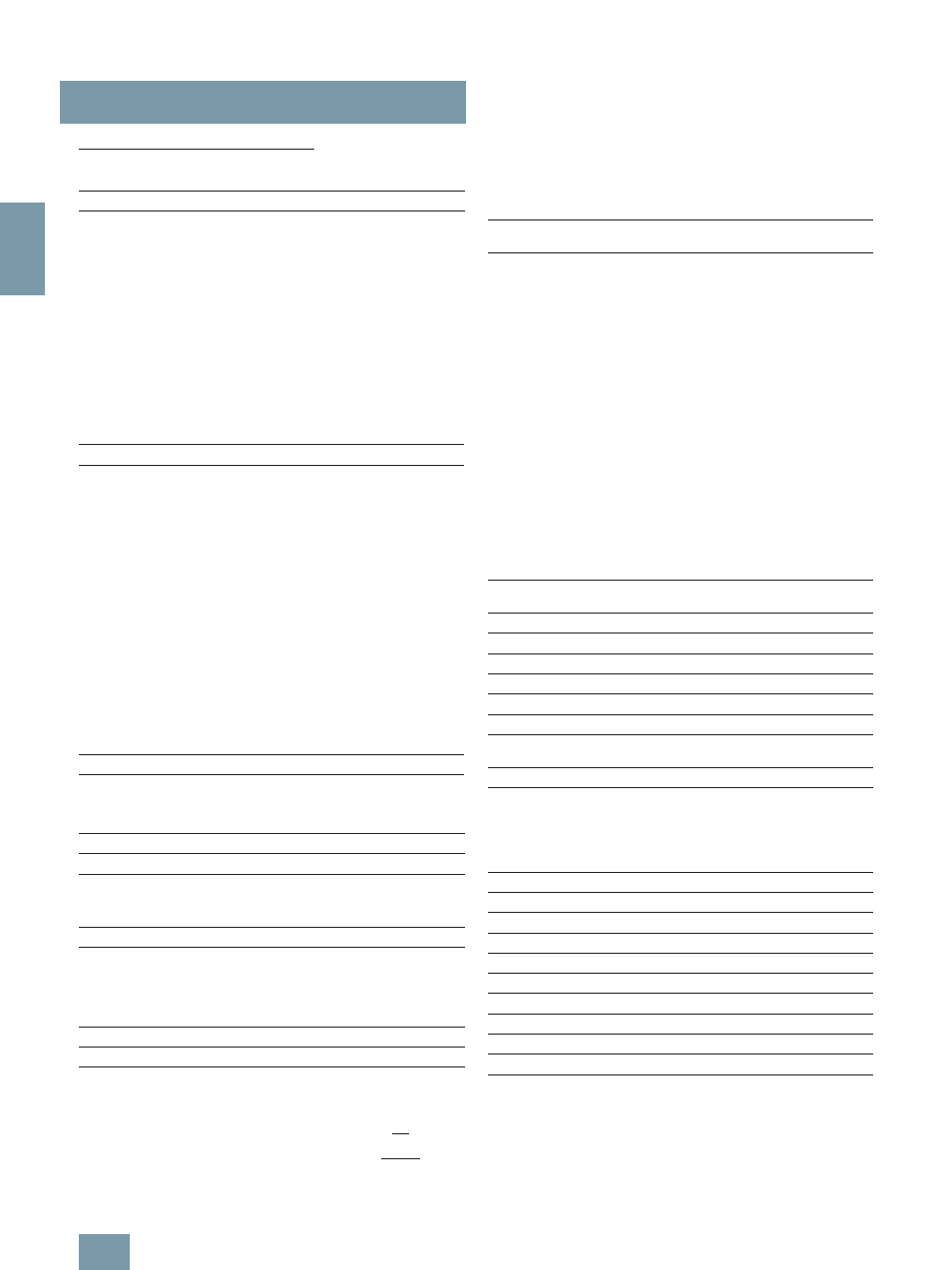
SITRANS P measuring instruments for pressure
Remote seals for transmitters and pressure gages
Technical description
2/156
Siemens FI 01 · 2009
2
Calculation of the temperature error
The following equation is used to calculate the temperature er-
ror:
Example of temperature error calculation
Dependence of temperature error on diaphragm material
The temperature errors listed in the previous table are based on
the use of stainless steel as the diaphragm material. If other dia-
phragm materials are used, the temperature errors change as
follows:
Maximum temperature of medium
The following maximum temperatures of the medium apply de-
pending on the material of the wetted parts:
Maximum capillary length for diaphragm seals (guidance
values)
dp = (
ϑ
RS
–
ϑ
Cal
)
⋅ f
RS
+ (
ϑ
Cap
–
ϑ
Cal
)
⋅ l
Cap
⋅f
Cap
+ (
ϑ
TR
–
ϑ
Cal
)
⋅ f
PF
dp
Additional temperature error (mbar)
ϑ
RS
Temperature on remote seal diaphragm (generally
corresponds to temperature of medium)
ϑ
Cal
Calibration (reference) temperature (20 °C (68 °F))
f
RS
Temperature error of remote seal
ϑ
Cap
Ambient temperature on the capillaries
l
Cap
Capillary length
f
Cap
Temperature error of capillaries
ϑ
TR
Ambient temperature on pressure transmitter
f
PF
Temperature error of the oil filling in the process
flanges of the pressure transmitter
Existing conditions
SITRANS P pressure transmitter for
differential pressure, 250 mbar, set
to 0 ... 100 mbar, with DN 80 remote
seal diaphragms without tube, dia-
phragm made of stainless steel,
mat. No. 1.4404/316L
f
RS
= 0.1 mbar/10 K
(0.0014 psi/10 K)
Capillary length
l
Cap
= 6 m (19.7 ft)
Capillaries fitted on both sides
f
Cap
= 0.07 mbar/(10 K
⋅ m
Cap
)
(0.001 psi/(10 K
⋅ m
Cap
))
Filling liquid silicone M5
f
PF
= 0.07 mbar/10 K
(0.001 psi/10 K)
Process temperature
ϑ
RS
= 100 °C (212 °F)
Temperature on the capillaries
ϑ
Cap
= 50 °C (122 °F)
Temperature on pressure transmit-
ter
ϑ
TR
= 50 °C (122 °F)
Calibration temperature
ϑ
Cal
= 20 °C (68 °F)
Required
Additional temperature error of
remote seals
dp
Calculation
in mbar
dp = (100 °C – 20 °C)
⋅ 0.1 mbar/10 K + (50 °C – 20 °C) ⋅ 6 m ⋅
0.07 mbar/(10 K
⋅ m) + (50 °C – 20 °C) ⋅ 0.07 mbar/10 K
dp = 0.8 mbar + 1.26 mbar + 0.21 mbar
in psi
dp = (212 °F – 68 °F)
⋅ 0.0014 psi/10 K + (112 °F – 68 °F) ⋅ 19.7 ft ⋅
0.001 psi/(10 K
⋅ 3.28 ft) + (112 °F – 68 °F) ⋅ (0.001 psi/10 K)
dp = 0.012 psi + 0.018 psi + 0.003 psi
Result
dp = 2.27 mbar (0.033 psi) (corresponds to 2.27% of set span)
Note
The determined temperature error only applies to the error resulting
from connection of the remote seal.
The transmission response of the respective transmitter is not included
in this consideration.
It must be calculated separately, and the resulting error added to the
error determined above from connection of the remote seal.
Diaphragm material
Change in temperature error of
remote seal
Increase in values by
Stainless steel
See previous tables
Hastelloy C4, mat. No. 2.4610
50%
Hastelloy C276, mat. No. 2.4819
50%
Monel 400, mat. No. 2.4360
60%
Tantalum
50%
Titanium
50%
PTFE coating on stainless steel dia-
phragm
80%
ECTFE coating or PFA coating on
stainless steel diaphragm
100%
Gold coating on stainless steel dia-
phragm
40%
Material
p
abs
< 1 bar
(14.5 psi)
p
abs
> 1 bar
(14.5 psi)
°C
(°F)
°C
(°F)
Stainless steel, 316L
200
(392)
400
(662)
PTFE coating
200
(392)
260
(500)
ECTFE coating
100
(212)
150
(302)
PFA coating
200
(392)
260
(500)
Hastelloy C4, mat. No. 2.4610 200
(392)
260
(500)
Hastelloy C276, mat. No.
2.4819
200
(392)
400
(662)
Monel 400, mat. No. 2.4360
200
(392)
400
(662)
Tantalum
200
(392)
300
(572)
Nom. diam.
Max. length of capillary
Diaphragm seal
Clamp-on seal
m
(ft)
m
(ft)
DN 25
(1 inch)
2.5
(8.2)
2.5
(8.2)
DN 32
(1¼ inch)
2.5
(8.2)
2.5
(8.2)
DN 40
(1½ inch)
4
(13.1)
6
(19.7)
DN 50
(2 inch)
6
(19.7)
10
(32.8)
DN 65
(2½ inch)
8
(26.2)
10
(32.8)
DN 80
(3 inch)
10
(32.8)
10
(32.8)
DN 100
(4 inch)
10
(32.8)
10
(32.8)
DN 125
(5 inch)
10
(32.8)
-
-
© Siemens AG 2008