0 controls (cont'd), 8 gas controls (cont'd), Wiring and service – Reznor RPBL Unit Installation Manual User Manual
Page 50: 4 optional electronic modulation (cont'd)
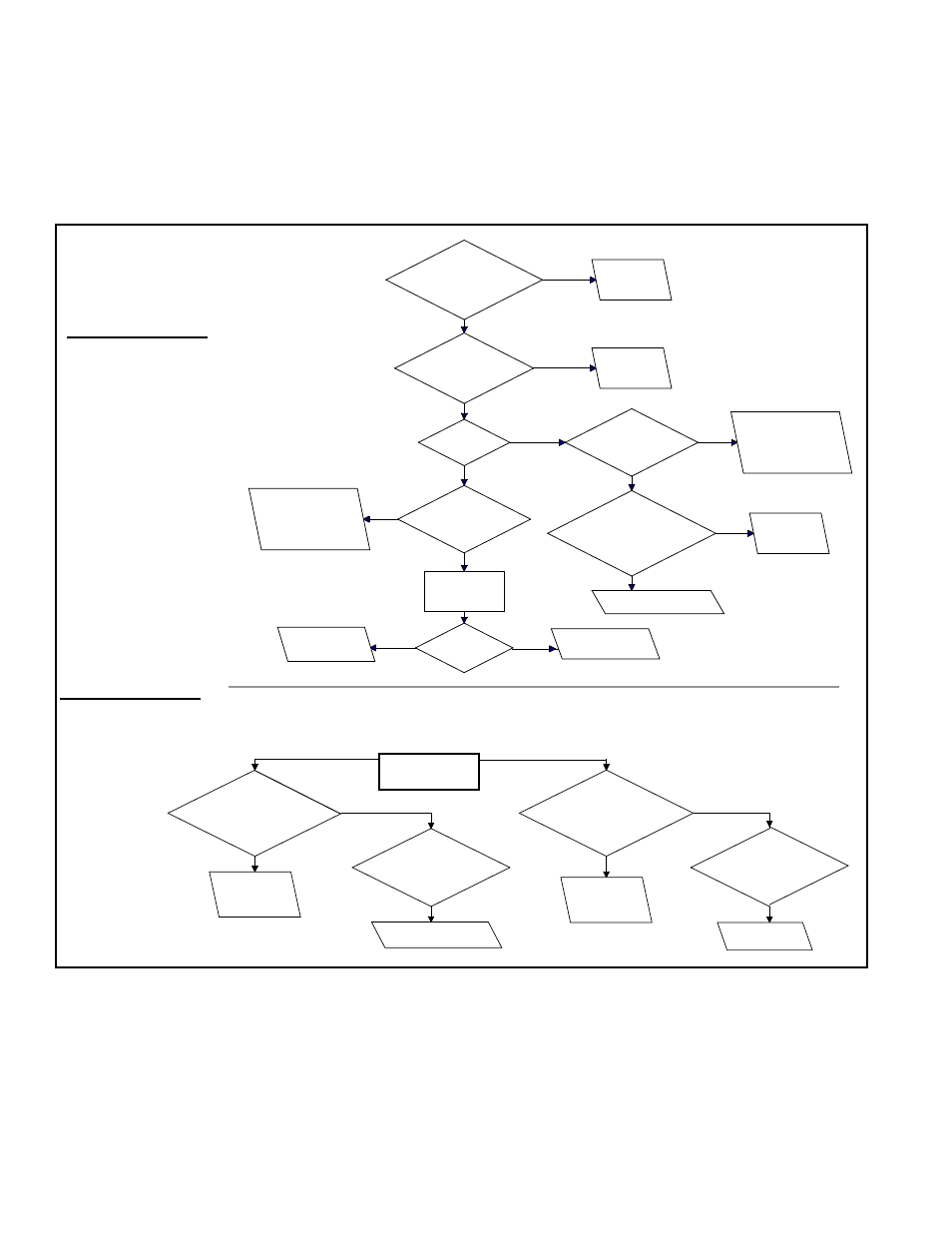
Form I-SSCBL/RPBL, Page 50
Wiring and Service
For wiring, consult the wiring diagram attached to the furnace. All wires in the electrical
box connecting the modulation controls must be 150°C.
This is a unique system which includes custom-built components and custom settings.
If service is required, follow the general troubleshooting guide and the special trouble-
shooting guide in
FIGURE 52.
Is there 24 volts
between Terminal 2 on #1
Time Delay Relay and
Terminal 7?
Go to
Troubleshooting
Chart for heater.
Is there 24 volts
between Terminal 84 and
Terminal 7?
Is the
damper open?
Is there voltage
between Terminal 88 and
Terminal 7?
Is there voltage
between Terminal 4 on
ignition permissive relay and
Terminal 7?
Replace #1 time delay relay.
Replace ignition
permissive
relay.
Check combustion
damper lower end switch
adjustment. If necessary,
replace end switch.
Is there voltage
between Terminal 87 and
Terminal 7?
Check combustion
damper lower end switch
adjustment. Replace end
switch if necessary.
Place a jumper
across Terminal
86 and Terminal 7.
Did the
damper close?
Replace motor run
time delay relay.
Replace combustion
damper gear motor.
Replace primary
manifold
pressure switch.
YES
NO
YES
NO
YES
NO
YES
NO
YES
NO
NO
YES
YES
NO
FIGURE 52 - Troubleshooting Guide
for Checking Bypass Combustion Air
Damper Safety Circuit on units with
Option AG39, AG40, AG41, or AG42
Symptom - Part 1:
Main burners are inoperative.
Assumes that 24 volts is available
between Terminal 2 and Terminal 7.
General
Instructions:
For each step,
check to ensure
that the wiring is
not defective and
that the wiring
connections are
secure.
Computer Controlled
Electronic Modulation
between 25% and 100%
Firing Rate, Option
AG40 and AG42
The furnace functions and is equipped in the same way as for Options AG39 and AG41
except that the temperature settings are selected through field-supplied computer soft-
ware and there is no temperature selector or duct sensor.
The furnace is equipped with a Maxitrol signal conditioner (see
FIGURE 50) which
accepts an input signal of either 4-20 milliamps or 0-10 volts from a customer-supplied
control device such as a computer. With the dip switches on the conditioner in the "on"
positions, the conditioner accepts a 4-20 milliamp signal. In the "off" positions, the con-
ditioner accepts a 0-10V signal. The conditioner converts the signal to the 0 to 20 volt
DC current required to control the modulating valve.
Measure manifold
pressure
during burner cycling.
When the
manifold pressure is
BELOW 1.0" w.c., is there a steady
voltage between Terminal 95
and Terminal 7?
Replace secondary
manifold pressure
switch.
While the
burner is cycling, is
there a steady voltage
between Terminal 84 and
Terminal 2?
Replace the primary
manifold pressure switch.
When the
manifold pressure is
ABOVE 1.5" w.c., is there a steady
voltage between Terminal 95
and Terminal 7?
Replace secondary
manifold pressure
switch.
Is there voltage
between Terminal 4 of the
ignition premissive relay and
Terminal 7?
Replace ignition
permissive relay.
YES
NO
YES
NO
YES
NO
Symptom - Part 2:
Steady call for heat - burner cycles. Assumes that 24 volts is available between Terminals 11 and
7 and Terminals 2 and 7.
8.0 Controls
(cont'd)
8.8 Gas Controls
(cont'd)
Electronic Modulation between 25% and 100% Firing Rate), Options
AG39, AG40, AG41, AG42 (cont'd)
8.8.4 Optional
Electronic Modulation
(cont'd)