3 using scheduled drive feedback data – Rockwell Automation Flex/WebPak 3000 DC Drive ControlNet, Network Communication Board, 915FK2101 User Manual
Page 28
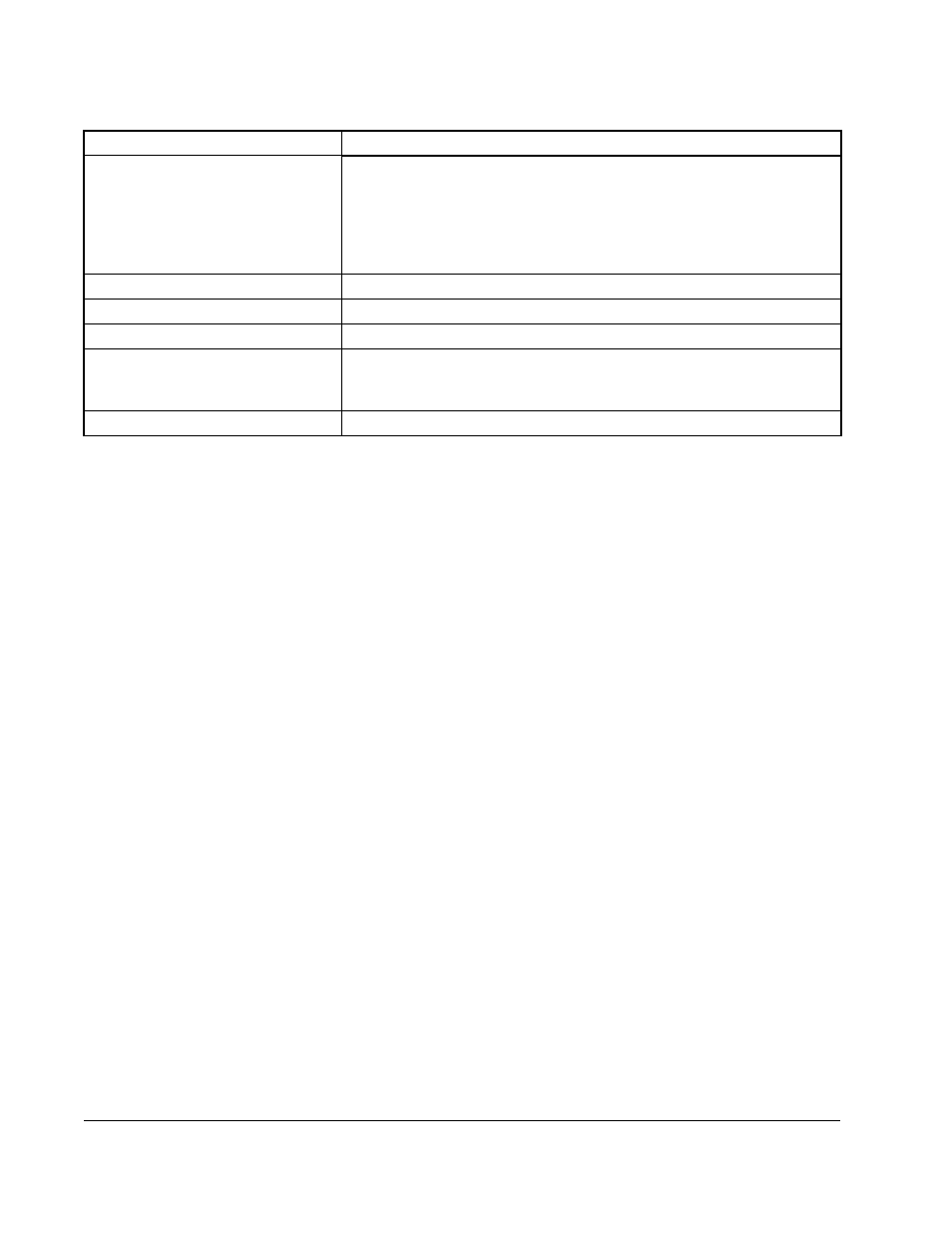
4-6
ControlNet Network Communication Option Board For Use With FlexPak 3000 and WebPak 3000 DC Drives
4.2.3 Using Scheduled Drive Feedback Data
The scheduled drive feedback data provides status to the programmable controller.
This data is sent over the ControlNet network as scheduled data, which is transmitted
at the configured update rate. However, the FlexPak 3000 drive sends the feedback
data to the option board every 5 ms and the WebPak 3000 drive sends the feedback
data to the option board every 10 ms, independent of the value of
CONTROL
SOURCE
SELECT
(P.000).
Scheduled drive feedback data is composed of one to eight words. You must create a
drive control application program to run in the programmable controller to read from
one to eight words of data to the file you defined during drive configuration as the
Input Address. The value you defined as the Input Size determines how many words
of data the programmable controller accepts from the option board. During a
scheduled data transfer, the option board writes the data contained in the Input
Address to the programmable controller.
The first word of the scheduled drive feedback data is always the drive status word; it
is written to element 0 in the Input file.
Should you configure less than eight words of input data, you can access the drive
reference and feedback data through file N12 as an unscheduled data transfer. See
section 4.3.
Table 4.5 describes the function of each word of the FlexPak 3000 scheduled drive
feedback data. Table 4.6 describes the function of each word of the WebPak 3000
scheduled drive feedback data.
Word 1 Speed/Torque Reference
This word is written to by the ControlNet network to command a speed
or torque reference. When the drive is configured as a speed
regulator, a value of 4095 corresponds to
TOP
LINE
SPEED
(P.020).
When the drive is configured as a torque/current regulator, a value of
4095 corresponds to
MAXIMUM
CURRENT
(P.007) percent of
MOTOR
RATED
ARM
AMPS
(P.008).
Word 2 Network Input 1
A value that is input in various places of the speed loop.
Word 3 Network Input 2
A value that is input in various places of the speed loop.
Word 4 Network Input 3
A value that is input in various places of the speed loop.
Word 5 Field Reference
This word is written to by the ControlNet network to command a field
reference value. 1= 1/4095 of
MOTOR
HOT
FLD
AMPS
(P.510). This
value is only used by the drive if a field current regulator kit is installed.
Words 6 and 7
Unused.
Table 4.5 – WebPak 3000 Scheduled Drive Reference Data (Continued)
Name
Description (PLC to Drive)