6 control clamps – NORD Drivesystems BU0750 User Manual
Page 94
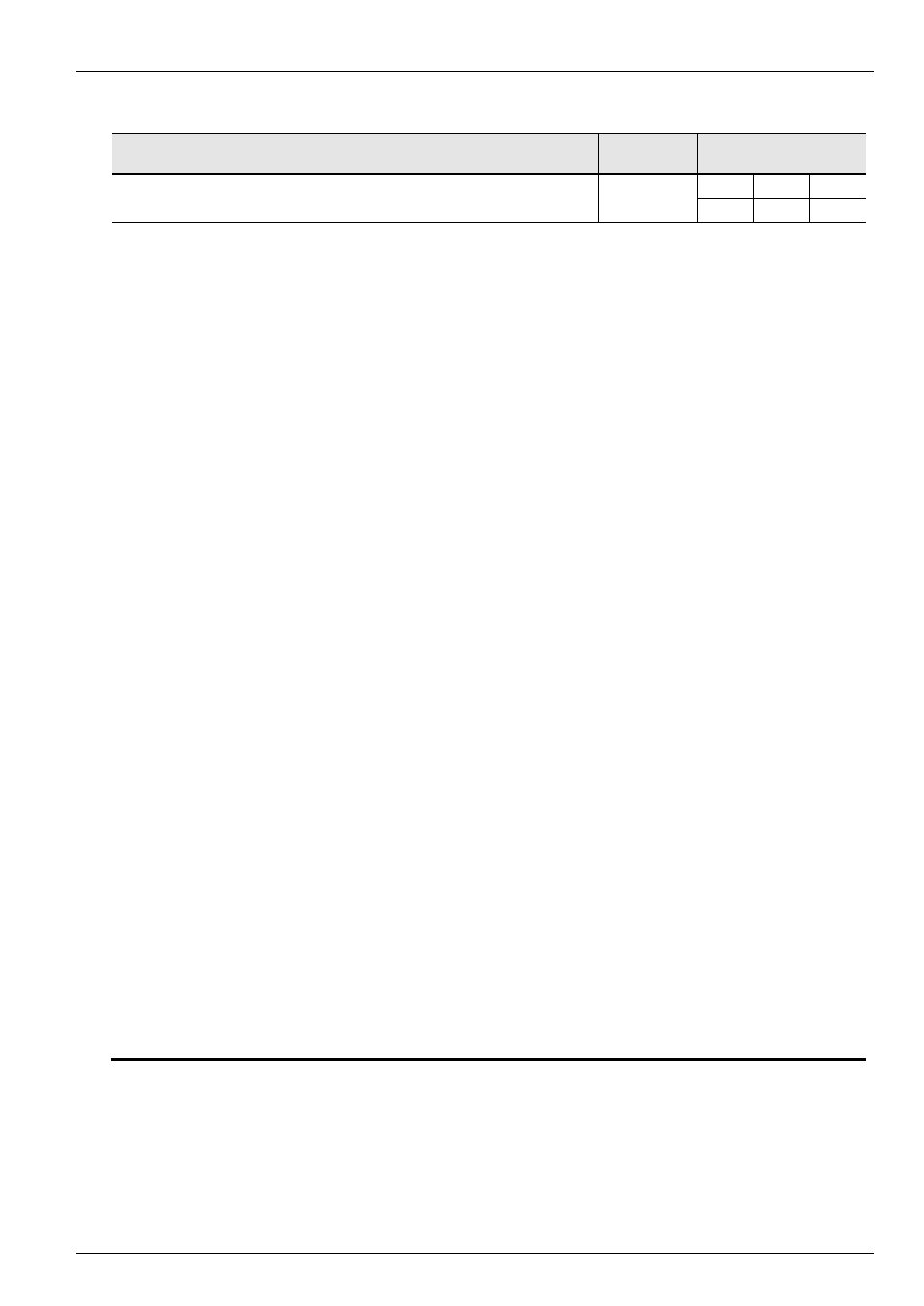
NORDAC SK 750E Manual
94
Subject to technical amendments
BU 0750 GB-3311
7.6 Control clamps
Parameter
Setting value / Description / Note
Parameter
set
Available with option
P400
Analog input function 1
BSC
STD
MLT
0...18
[ 1 ]
The FI analog input can be used for various functions. It should be noted that only one of the
functions given below is possible at any time.
If, for example, an actual PID frequency is selected, the frequency setpoint cannot be an analog
signal. The setpoint can, e.g., be specified via a fixed frequency.
0 =
Off, the analog input has no function. After the FI has been enabled via the control
terminals, it will supply the set minimum frequency (P104).
1 =
Setpoint frequency, the given analog range (P402/P403) varies the output
frequency between the set minimum and maximum frequencies (P104/P105).
2 =
Torque current limit, based on the set torque current limit (P112), this can be
altered by means of an analog value. 100% setpoint here corresponds to the set
torque current limit P112. 20% cannot be undershot (with P300=1, not below
10%)!
3 =
Actual PID frequency*, is required to set up a control loop. The analog input
(actual value) is compared with the setpoint (e.g. fixed frequency). The output
frequency is adjusted as far as possible until the actual value equals the setpoint.
(see Control variables P413
– P415)
4 =
Frequency addition *, the supplied frequency value is added to the setpoint.
5 =
Frequency subtraction *, the supplied frequency value is subtracted from the
setpoint.
6 =
Current limit, based on the set current limit (P536), this can be altered via the
analog input.
7 =
Maximum frequency, the maximum frequency of the FI is set in the analog range.
100% corresponds to the setting in parameter P411. 0% corresponds to the
setting in parameter P410. The values for the min/max output frequency
(P104/P105) cannot be exceeded or undershot.
8 =
Actual frequency PID limited *, as for Function 3, Actual frequency PID, however
the output frequency cannot fall below the programmed minimum frequency value
in Parameter P104. (no change to rotation direction)
9 =
Actual PID frequency monitored *, as for Function 3 "Actual frequency PID",
however the FI switches the output frequency off when the minimum frequency
P104 is reached.
10 =
Servo mode torque, in the Servo mode the motor torque can be set using this
function.
11 =
Torque precontrol, a function that enables a value for the anticipated torque
requirement to be entered in the controller (interference factor switching). This
function can be used to improve the load take-up of lifting equipment with separate
load detection.
12 =
Reserved
13 =
Multiplication, the setpoint is multiplied with the analog value supplied. The
analog value adjusted to 100% then corresponds to a multiplication factor of 1.
.... continued on next page