NORD Drivesystems BU0750 User Manual
Page 103
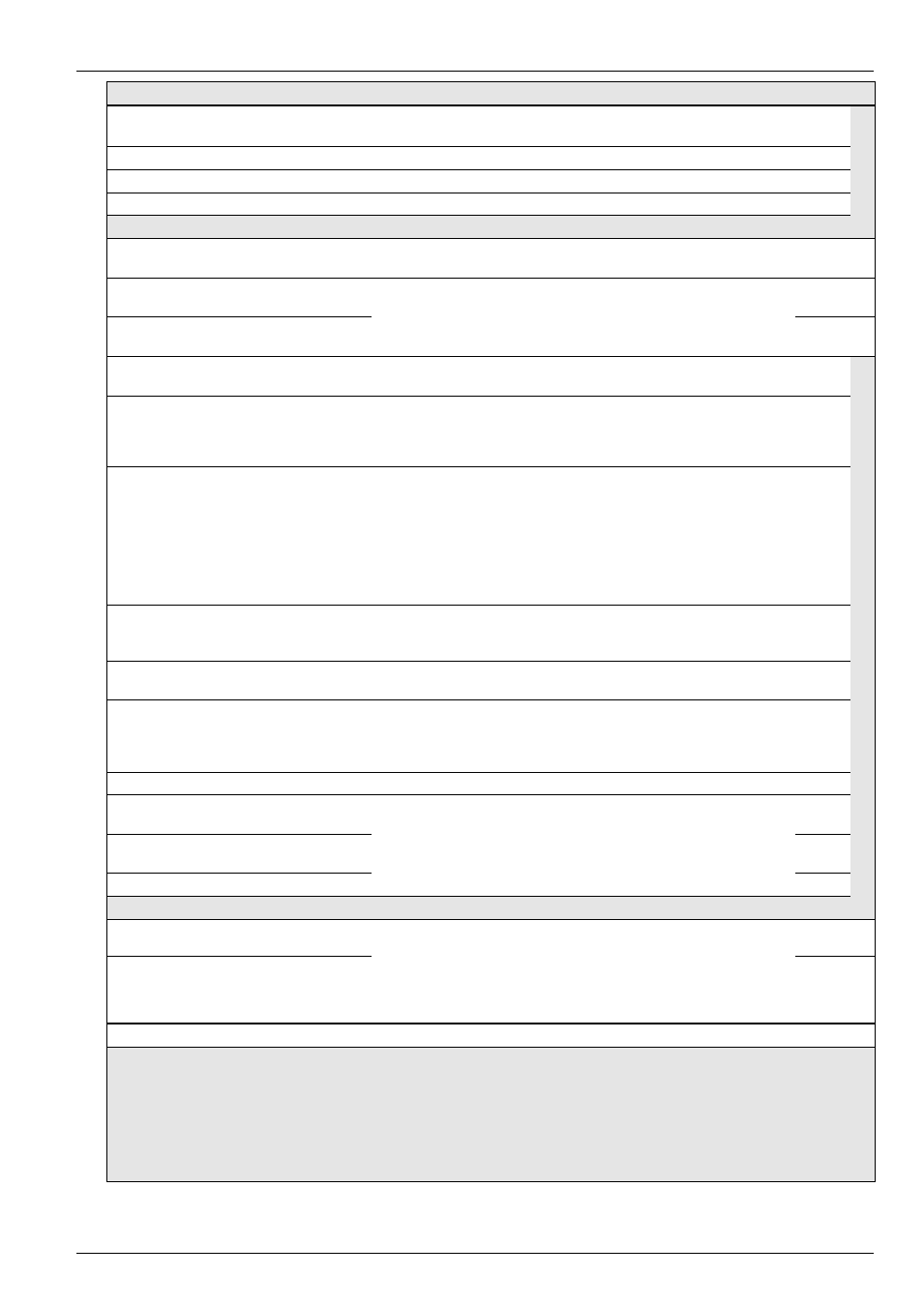
BU 0750 GB-3311
Subject to technical amendments
103
Value Function
Description
Signal
26
Torque current limit
2 3 5
Adjustable load limit, the output frequency is reduced when this is
reached.
P112
Analog
27
Actual PID frequency
2 3 4 5
Possible feedback of actual value for the PID controller
Analog
28
Frequency addition
2 3 4 5
Addition to other frequency setpoint values
Analog
29
Frequency subtraction
2 3 4 5
Subtraction from other frequency setpoint values
Analog
Digital inputs can be used for simple analog signals (max. 7 Bit resolution).
30
PID control on/off
5
Switches the PID controller / process controller function on and off
(High = ON)
High
=On
31
Enable right blocked
5
Blocks the >Enable right/left< via a digital input or Bus control.
Does not depend on the actual direction of rotation of the motor
(e.g. following negated setpoint).
With multi I/O only available in P420...423!
Low
32
Block enable left
5
Low
33
Current limit (analog)
2 3 5
Based on the set current limit (P536), this can be changed using
the digital/analog input.
Analog
34
Maximum frequency (analog)
2 3
4 5
The maximum frequency of the FI is set in the analog range. 100%
corresponds to the setting in parameter P411. 0% corresponds to
the setting in parameter P410. The values for the min/max output
frequency (P104/P105) cannot be exceeded or undershot.
Analog
35
Actual frequency PID controller
limited (analog)
2 3 4 5
Needed to set up a control loop. The digital/analog input (actual
value) is compared with the setpoint (e.g. other analog input or
fixed frequency). The output frequency is adjusted as far as
possible until the actual value equals the setpoint. (see control
variables P413
– P416)
The output frequency cannot fall below the programmed minimum
frequency value in parameter P104. (No change of rotation
direction!)
Analog
36
Actual frequency PID controller
monitored (analog)
2 3 4 5
As function 35, >Actual frequency PID< but the FI switches the
output frequency off when the >Minimum frequency< P104 is
reached.
Analog
37
Torque
Servo mode (analog)
2 3 5
The motor torque can be set or limited via this function in Servo
mode.
Analog
38
Torque precontrol (analog)
2 3 5
Function which enables a value for the anticipated torque
requirement to be entered in the controller (interference factor
switching). This function can be used to improve the load take-up
of lifting equipment with separate load detection.
P214
Analog
39
Multiplication
3 5
This factor multiplies the master setpoint value.
Analog
40
Actual value process controller
3
5
As for P400 = 14-16
Further details regarding the process controller can be found in
Section 10.2
Analog
41
Setpoint value process controller
3 5
Analog
42
Precontrol process controller
3 5
Analog
Digital inputs can be used for simple analog signals (max. 7 Bit).
47
Increase frequency
Only DI 1-4; in combination with enable R/L the output frequency
can be continuously varied. To save a current value in P113, both
inputs must be at a High voltage for 0.5s. This value then applies
as the next starting value for the same direction of rotation (Enable
R/L) otherwise start at f
MIN
. Values from other setpoint sources
(e.g. fixed frequencies) are not taken into account.
High
48
Decrease frequency
High
1
If none of the digital inputs is programmed for left or right enable, then the actuation of a fixed frequency or jog frequency will enable
the frequency inverter. The rotation field direction depends on the sign of the setpoint.
2
Also effective for Bus control (RS485, CANbus, CANopen, DeviceNet, Profibus DP, InterBus, RS232)
3
Functions only available for Basic and Standard I/O, analog setpoints are processed. They are suitable for simple requirements (7 bit
resolution).
4
The limits of these values are set by the parameters >Minimum frequency auxiliary setpoints< P410 and >Maximum frequency
auxiliary setpoints< P411.
5
Settings are not available with P424 and P425 (Multi I/O).