Watlow CLS User Manual
Page 163
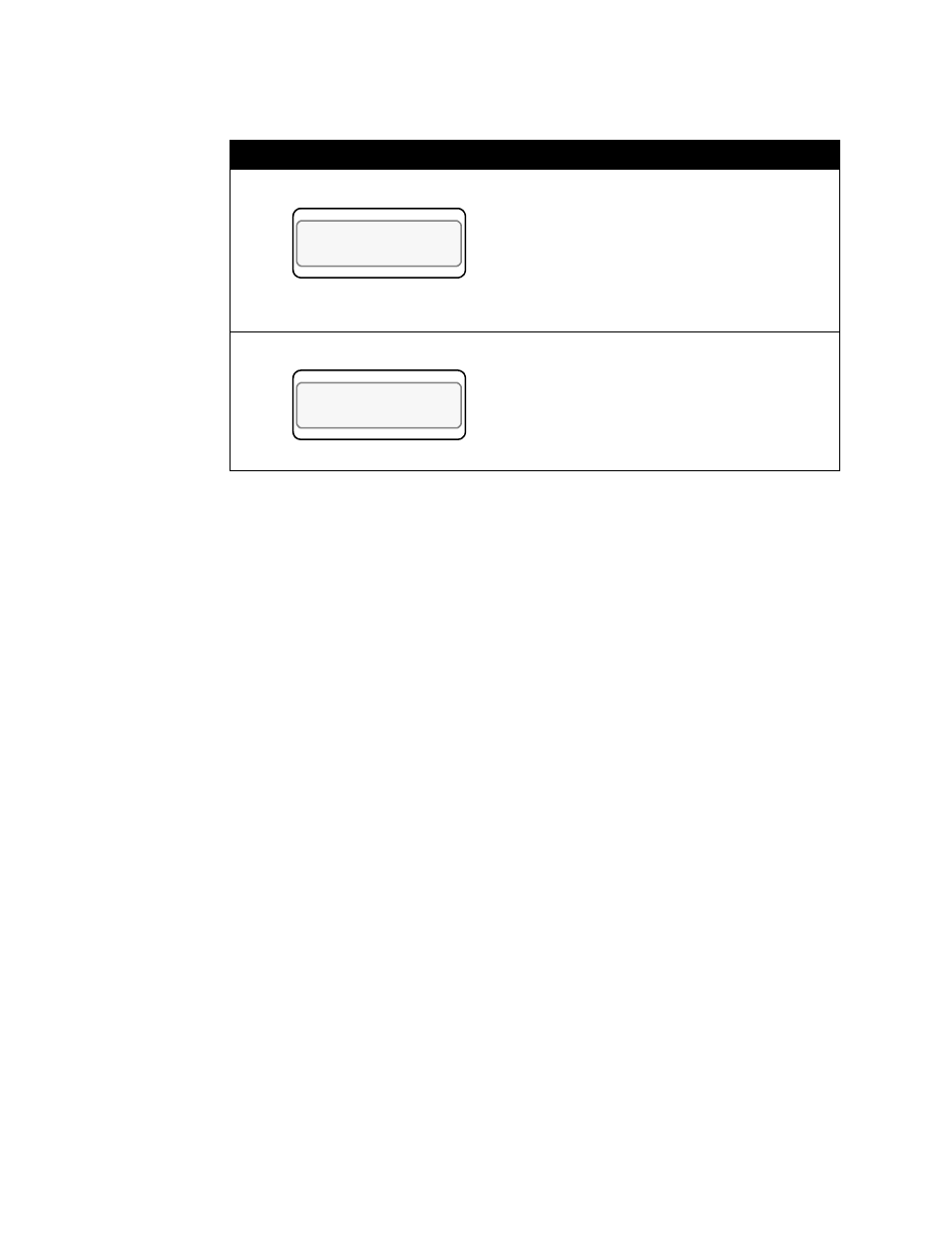
Appendix B: Enhanced Process Control
155
Now press the "Back" key several times until the normal loop display
appears. The output percentage of loop 1 will now control the setpoint
of loop 2. You may set Channel 1 to Manual and the Output to 0%,
Channel 2 SP should =150. Adjust Channel 1 Manual Output to 50%,
Channel 2 SP should =170. Adjust Channel 1 Manual Output to 100%,
Channel 2 SP should =190.
To complete the cascade setup, both loop 1 and loop 2 must be
configured for inputs, outputs, and alarms.
In addition, the PID parameters of loop 1 must be tuned to produce the
desired effect for the application on the setpoint of loop 2. For a cascade
control application that uses the secondary loop for PID control, then
Loop 1 must use only proportional mode. This must be set for the
amount of change in the PV to cause a 100% change in the output level.
It is necessary for the temperature of Loop 1 temperature to drop only
10 ºF in order for Loop 2 to change from 150 to 190 ºF. Then set the PB
of loops 1 to 10, and turn off Intergal and Derivative terms by setting TI
and TD to 0.
The PID parameters of loop 2 must be tuned to perform efficient
control.
For two-zone cascade control systems, the PID settings for both loops,
the primary plus the secondary, must be optimized for good temperature
control.
Please consult the SETUP Section of this manual for information on
tuning PID loops.
Enter the heat span of the secondary loop.
This is the span over which the primary
output from 0-100% is used to change the
setpoint. For this example we will assume
a linear rise in SP, so the heat span is
40°F.
Press Enter.
Enter the cool span of the secondary loop.
For this example we will assume no low-
side adjustment to the SP, so the cool
span is 0°F.
Press Enter.
Display
User Input
LOOP PROCESS UNITS
ALARM SETPOINT STATUS OUT%
02 CASCADE
HT SPAN? 40
LOOP PROCESS UNITS
ALARM SETPOINT STATUS OUT%
02 CASCADE
CL SPAN? 0