IAI America PCON-CY User Manual
Page 25
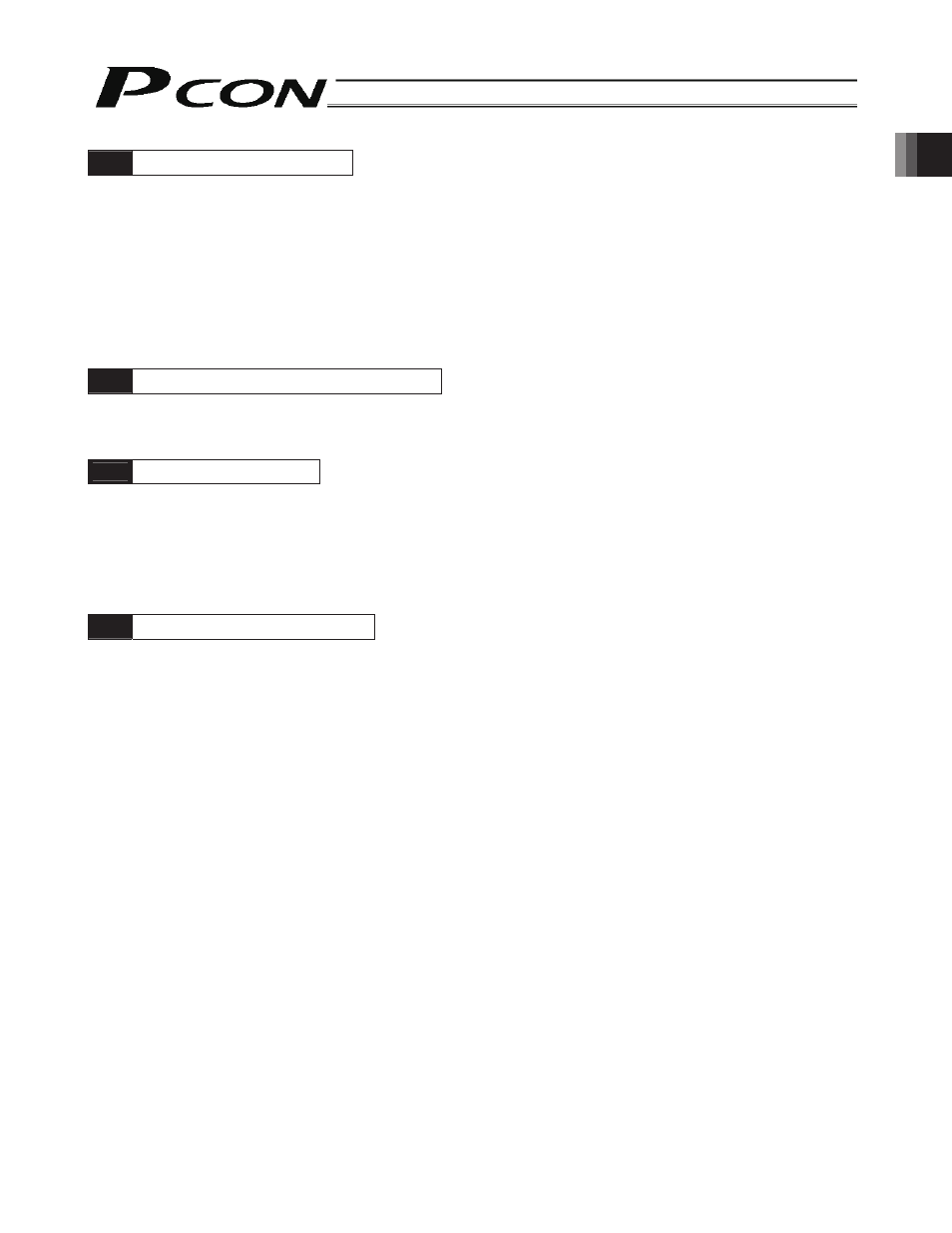
15
1. Overview
6.
Operating when the servo is ON
Confirm that the slider or rod is not contacting a mechanical end.
If the slider or rod is contacting a mechanical end, move it away from the mechanical end.
If the actuator is equipped with a brake, move the actuator after turning ON the forced brake release switch to forcibly release
the brake.
At this time, be careful not to get your hand pinched or the robot hand damaged by the actuator dropping suddenly due to its
dead weight.
Turn ON the servo using the PC or teaching pendant.
If the actuator enters a servo lock state and the monitor LED [SV/ALM] on the front face of the controller illuminates in green,
the controller is normal.
7.
Confirming the safety circuit operation
Confirm that the emergency cutoff circuit (or motor drive-power cutoff circuit) operates normally.
→ Chapter 3, “Installation and Wiring”
8.
Setting a target position
Use the teaching pendant or PC to set a target position in the “Position” field of the position table (rear end, front end,
intermediate point).
* If any movement operation is started without setting a target position first, the message “No movement data” will be
displayed. Determine an appropriate target position by fine-tuning the work or robot hand.
* Once a target position is set, other items (speed, acceleration/deceleration, positioning band, etc.) will be set to their defaults
automatically.
→ Chapter 4, “Position Table Settings”
9.
Adjustment by test operation
Input a move command from the PLC to perform positioning.
If necessary, perform the following fine adjustments:
• Depending on the weight, material and/or shape of the work, vibration or noise may occur. If you notice undesirable vibration
or noise, lower the speed, acceleration and/or deceleration.
• You may also want to adjust the zone output signal limits and positioning band to prevent contact with peripheral equipment
or reduce the tact time.
• If push-motion operation will be performed, select optimal current-limiting value, push-motion completion judgment time and
push speed.
→ Chapter 4, “Position Table Settings”
→ Chapter 5, “Operation Using I/O Signals”