IAI America PCON-CY User Manual
Page 117
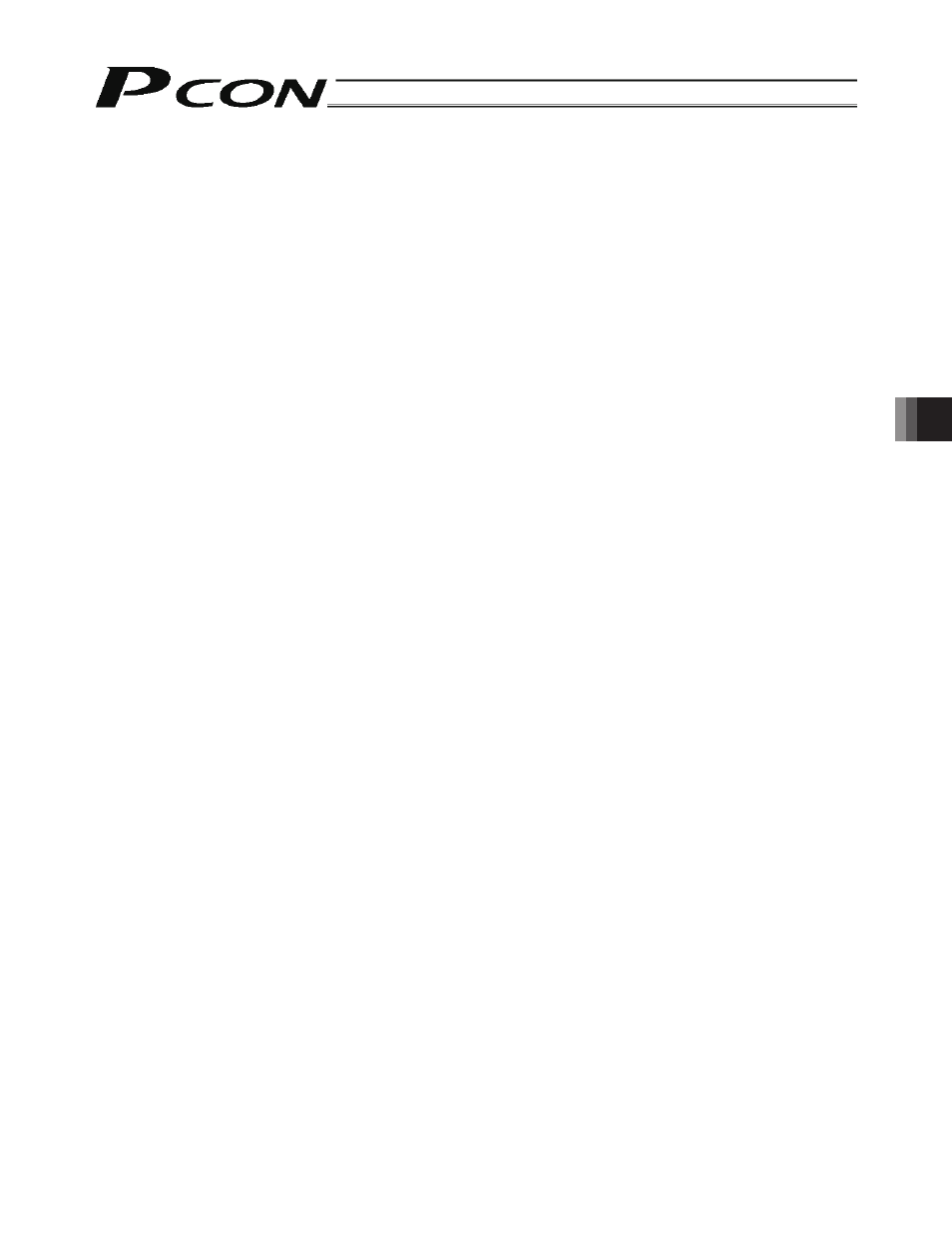
107
7. T
roubleshooting
z With an Actuator Installed in Vertical Orientation, Positioning Completes Prematurely.
Cause:
[1] The load exceeds the rated load capacity.
[2] The ball screw is receiving torsional stress due to the actuator affixing method, uneven tightening of bolts,
etc.
[3] The slide resistance of the actuator itself is high.
Action:
If [1] is suspected, increase the value of User Parameter No. 13 (Current-limiting value during homing).
Increasing the parameter value increases the homing torque. As a guide, however, the setting should not
exceed 100% for the RA3C/RGD3C types or 75% for all other types.
[2] To check if the condition in [2] is present, loosen the affixing bolts and check if the slider moves smoothly. If
the slider moves smoothly, adjust the affixing method and bolt tightening method.
[3] If the slide resistance of the actuator itself is high, contact IAI.
z With an Actuator Installed in Vertical Orientation, Noise Generates during Downward Movement.
Cause:
The load exceeds the rated load capacity.
Action:
[1] Decrease the speed.
[2] Decrease the value set in User Parameter No. 7 (Servo gain number). As a guide, do not decrease the
setting to below 3.
z Vibration Occurs when the Actuator Is at Standstill.
Cause:
The slider is receiving external force.
Action:
If external force cannot be removed, increase the value set in User Parameter No. 12 (Current-limiting value at
standstill after positioning).
Increasing the setting of this parameter increases the holding torque. As a guide, keep the current limiting value
to 70% or below.
z The Actuator Overshoots while Decelerating to a Stop.
Cause:
The load inertia is high due to an inappropriate balance of the load and deceleration.
Action:
Decrease the set deceleration.
z Stopped Position Sometime Deviates from the Home Position or Target Position.
Cause:
[1] Encoder waveforms are disturbed due to noise.
[2] If the actuator is of rod type, non-rotational error increased due to application of rotational moment to the
rod.
Action:
[1] Check if the grounding is provided correctly, and also check for any equipment that may be generating
noise.
[2] Depending on the condition, the actuator may have to be replaced. Contact IAI.
z The Actuator Moves Slow during Push-motion Operation.
Cause:
The set current-limiting value is low with respect to the load and slide resistance.
Action:
Increase the current-limiting value during push-motion operation.
z The Actuator Moves Only a Half, or as Much as Twice, the Specified Travel.
Cause:
[1] The controller and actuator combination is incorrect.
The ball screw lead varies according to the actuator type. If the actuator is not combined with an appropriate
controller, the travel and speed will change.
[2] Pre-shipment setting error at IAI
Action:
[1] If multiple actuators of different types are used, check the label on each actuator or use other means to see
if they are connected to correct controllers.
[2] Contact IAI.