FEC MICRO NR User Manual
Page 112
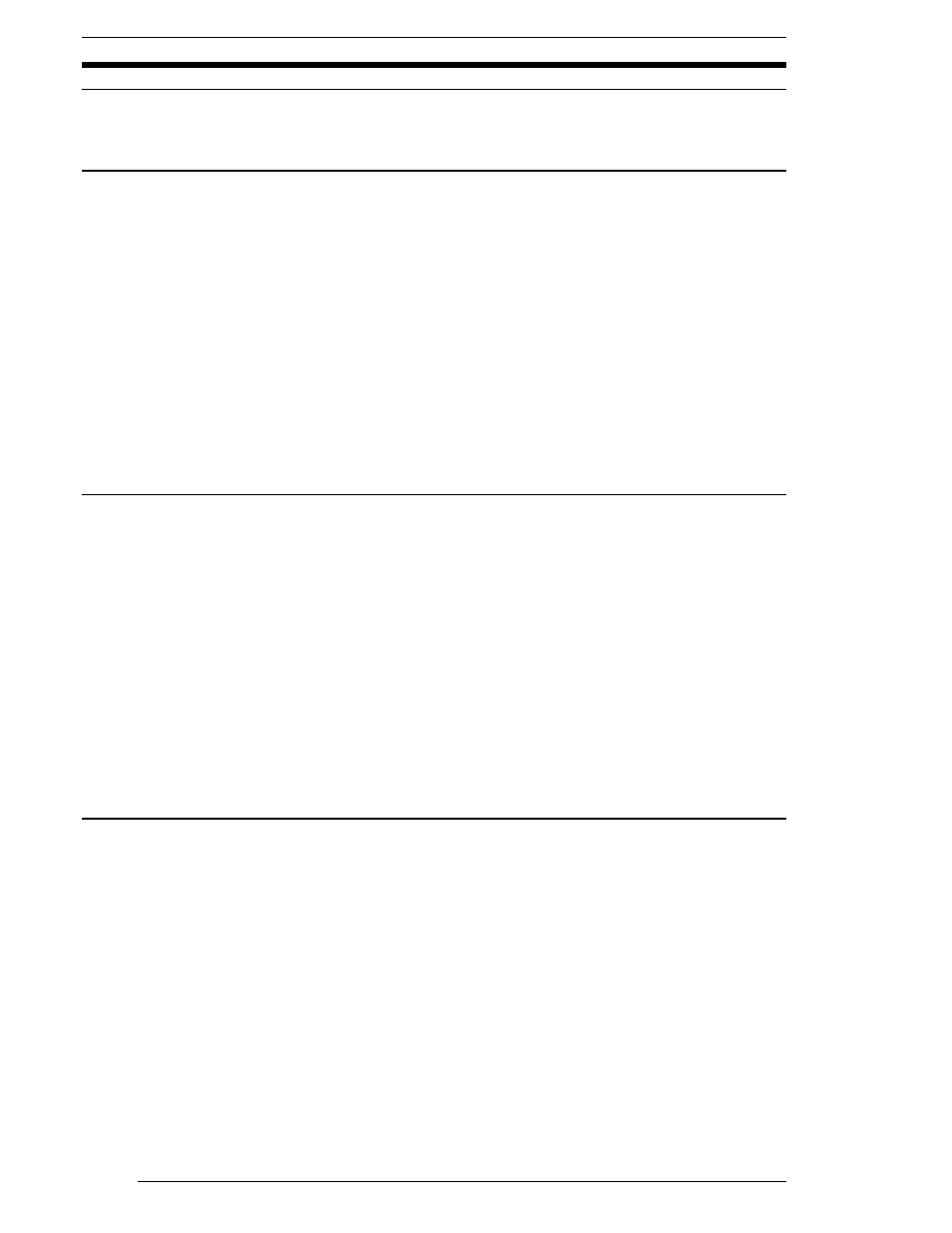
Chapter 9: Troubleshooting
Page 9-10
9.8
Servo Amplifier Error
When Servo Amplifier Errors occur and cannot be cleared with a RESET signal, cycle
power to the MNR Unit.
9.8.1 Code 8-1
SERVO AMPLIFIER ERROR / SERVO IS OVER HEATED
The MNR controller servo circuit has overheated.
This abnormal is caused from;
1. The controller servo drive circuit has failed.
2. If the environment temperature is more than 122 degrees Fahrenheit (50 degree
centigrade) without any air flow.
3. The duty cycle of the fastening application is too severe for this size of tool, or for the
parameters currently setup.
RECOVERY:
1. Replace the controller
2. Provide additional cooling to the enclosure.
3. Reduce duty cycle - Increase tool “downtime or off time” and/or increase torque speed to
reduce the amount of time running at high torque/slow speed.
9.8.2 Code 8-4
SERVO AMPLIFIER ERROR / OVER CURRENT
The MNR controller servo circuit experienced a current overload.
This abnormal is caused from;
1. The tool cable or controller servo drive circuit has failed.
2. If the environment temperature is more than 122 degrees Fahrenheit (50 degree
centigrade) without any air flow.
3. Maximum torque is being run or exceeded by the tool every cycle.
4. Speed may be too low or too high during torque speed.
RECOVERY:
1. Replace the tool cable and/or controller.
2. Verify proper cooling for the enclosure.
3. Verify proper torque or work piece.
4. Adjust torque speed setting.
9.8.3 Code 8-5
SERVO AMPLIFIER ERROR / INTERNAL POWER SUPPLY
The MNR controller servo power supply circuit is not working properly or the input voltage is
above the maximum limit.
This abnormal is caused from;
1. The controller internal power supply has failed
2. Source voltage is incorrect (24 volts dc) and the environment temperature is also close to
the limit.
3. If the environment temperature is more than 122 degrees Fahrenheit (50 degree
centigrade) without any air flow.
4. Speed may be too low or too high during torque speed.
RECOVERY:
1. Replace the controller.
2. Provide additional cooling to the enclosure.
3. Verify and correct the source voltage as required.
4. Adjust torque speed setting.