Oil sump, Oil filter support – Generac Power Systems NP-40G User Manual
Page 79
Attention! The text in this document has been recognized automatically. To view the original document, you can use the "Original mode".
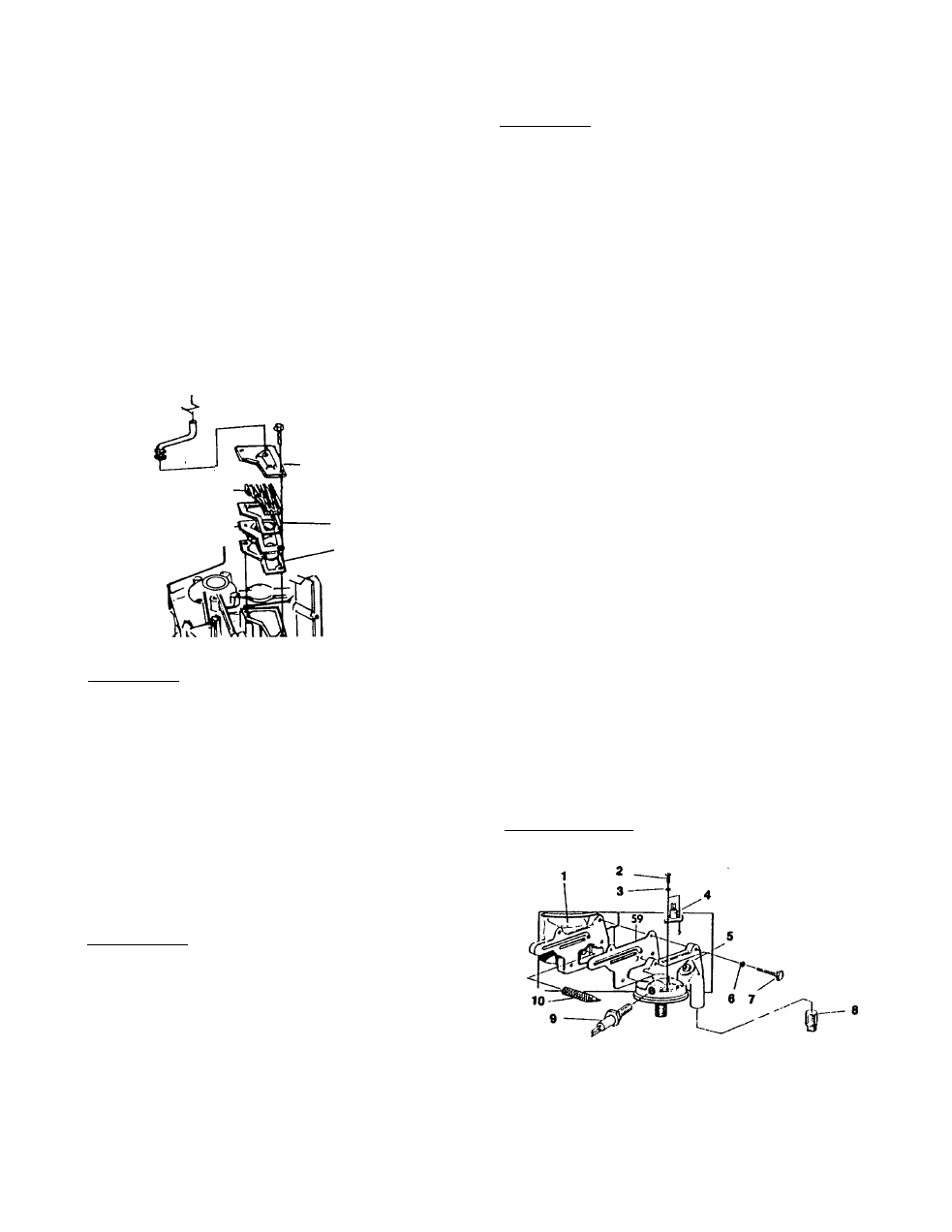
Section 5.1- ENGINE OIL SYSTEM
The breather serves to maintain a partial vacuum
In the engine crankcase, to prevent oil from being
forced past oil seals, gaskets or rings.
See Figure 6. A reed type breather valve permits
excess pressure to be vented out of the crankcase
and to atmosphere through a breather tube. A
breather retainer limits the movement of the
breather valve. Two small oil return holes In the
breather cup allow condensed oil vapors to drain
back to the crankcase. A "steel wool" type breather
separator separates the breather cup from the
breather cover and breather tube opening.
Figure 6, Breather Assembly
TO AIR
CLEANER
BASE
BREATHER
VALVE
BREATHER
BAFFLE CUP
— M6 BOLT
- BREATHER
COVER
GASKET
INSPECTION:
Remove the breather hose. Inspect It for cracks,
damage, hardening. Replace, If necessary.
Clean the breather cover and breather cup In
commercial solvent. Check that the two small drain
holes In the breahtre cup are open; open with a
length of wire. If necessary.
Inspect the rivets that retain the reed type
breather valve, make sure they are tight. Also
check that the valve seats flat on the breather cup
around the entire surface of the valve.
Oil Sump
DESCRIPTION:
The die cast aluminum oil sump Is retained to the
crankcase with six (6) flanged head bolts. Install a
new gasket between the oil sump and crankcase
each time the oil sump Is removed.
Bores are provided In the oil sump for fa) oil
pump rotors and camshaft, (b) crankshaft, (c) gov
ernor gear assembly, (d) oil pickup. Cored oil pas
sages are provided from the pickup to the pump
and from the pump to the crankshaft bore.
INSPECTION:
Clean the oil sump and blow dry with com
pressed air. Use compressed air to blow out all oil
passages. Inspect the sump for cracks, damaae,
etc. Check the following bores In the oil sump Tor
wear:
CRANKSHAFT BEARING BORE DIAMETER
GN-190 ENGINE
DESIGN DIAMETER: 1.103-1.105 Inch (28.030-
28.058mm)
WEAR LIMIT:
1.106 Inch (28.088mm) Maximum
CRANKSHAFT BEARING BORE DIAMETER
GN-220 ENGINE
DESIGN DIAMETER: 1.104-1.105 Inch (28.040-
28.065mm)
WEAR LIMIT: 1.106 Inch (28.092mm) Maximum
CAMSHAFT BEARING BORE DIAMETER
GN-190 & GN-220 ENGINE
DESIGN DIAMETER: 1.299-1.300 Inch (33.00-33.03mm)
WEAR LIMIT: 1.302 Inch (33.06mm) Maximum
OIL PUMP INNER ROTOR SHAFT DIAMETER
GN-190 & GN-220 ENGINE
DESIGN DIAMETER: 0.353-0.354 Inch (8.969-8.987mm)
WEAR LIMIT: 0.352 Inch (8.949mm) Minimum
Oil Filter Support
An oil filter support and its gasket are retained to
the oil sump by four (4) M6-1.00 bolt.
A threaded bore Is provided In the support for a
low oil pressure switch. This switch will protect the
engine against damaging low oil pressure by shut
ting the engine down automatically If oil pressure
should drop below a pre-set low limit.
A high oil temperature switch Is retained to the
support by two (2) MS screwqs and lockwashers.
This thermal sensor will protect the engine against
damaging high temperature conditions through au-
tomatlc shutdown.__________________________
Figure 7. Oil Filter Support
1. Oil Sump 5. Filter Support
2 MS Scraw 6. Lockwasher
3. Lockwasher 7. Screw
4. Oil Temp. Switch
8. Pipe Plug
9. Olf Press. Switch
10.011 Pickup
Screen
Page 5.1-3