Hapter, Flexpak 3000 drives: alternate register map – Rockwell Automation FlexPak/WebPak 3000 DC Drive AutoMax Network Communication Board User Manual
Page 49
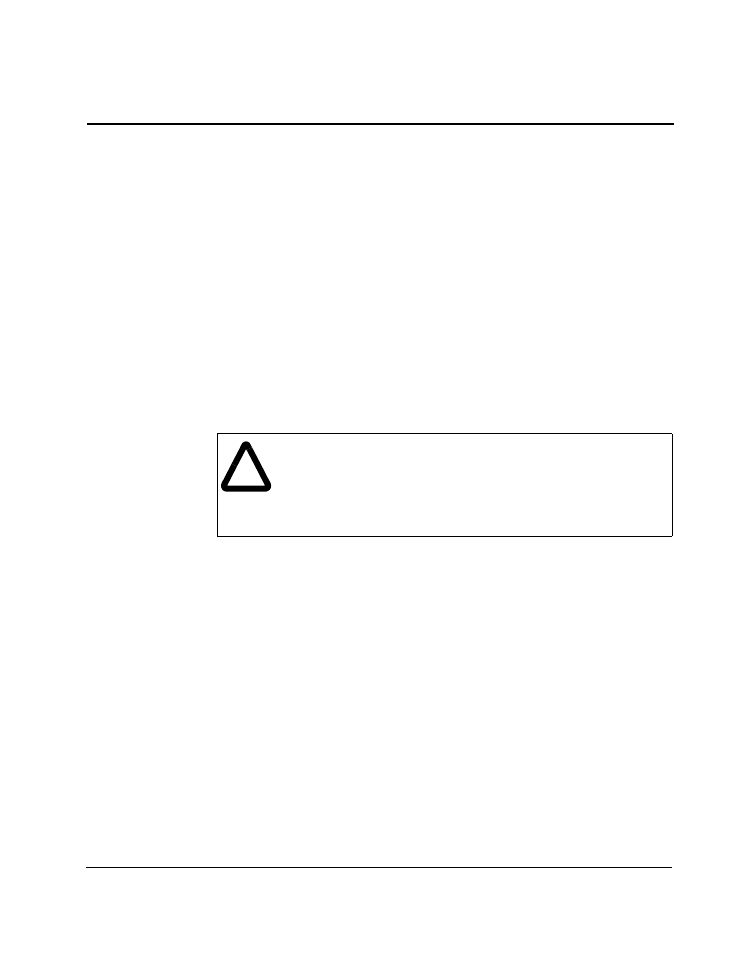
FlexPak 3000 Drives: Alternate Register Map
6-1
C
HAPTER
6
FlexPak 3000 Drives:
Alternate Register Map
This section lists the alternate register map, which enables you to access most of the
FlexPak 3000 original register map functions plus some additional functions. The
alternate register map is organized so that commonly used functions are available in
Drop_1. It also offers a different set of options in Drop_1 than the original register
map.
The additional functions that are available through the alternate register map are:
•
Winding functions:
SPEED
FEEDBACK
GAIN
(Drop_1, register 38) and
UNDERWIND
ENABLE
(Drop_1, register 32, bit 5) enable you to set up under- or overwinding and
set the gain of the speed loop feedback path for winding applications.
•
Access to the speed loop
PI
reset and initial value. These parameters are
SPD
LOOP
PI
INIT
SEL
(Drop_2, register 32),
SPD
LOOP
PI
INIT
VAL
(Drop_1, register 39), and
SPD
LOOP
PI
RESET
(Drop_1, register 32, bit 6).
•
Process Error Parameter Number (Drop_1, register 27)
•
NETW
REGISTER
MAP
SEL
(P.914) (Drop_1, register 29)
•
RAMP
STOP
DECEL
TIME
(P.018) (Drop_2, register 33)
•
INV
FLT
AVOID
SEL
(P.312) (Drop_2, register 43)
•
TACH
LOSS
SCR
ANGLE
(P.608), (Drop_3, register 50)
•
NEG
CUR
LIM
INV
EN
(P.226) (Drop_3, register 53, bit 0)
•
OCL
PROP
TRIM
SELECT
(P.813) (Drop_3, register 53, bit 1)
•
OCL
TYPE
3
POSN
REG
EN
(P.814) (Drop_3, register 53, bit 2)
•
PHASE
LOSS
DETECT
EN
(P.609) (Drop_3, register 53, bit 3)
•
STOP
DECEL
SELECT
(P.122) (Drop_3, register 53, bit 4)
•
CML
REF
LIMIT
SELECT
(P.311) (Drop_3, register 53, bit 6
•
DIG
IN
0
SELECT
(P.428) (Drop_4, register 47)
Brief descriptions of parameters are in the register map tables. For detailed parameter
descriptions, refer to the
FlexPak 3000 DC Drive Software Reference Manual
.
!
ATTENTION: If you are using the alternate register map (
NETW
REGISTER
MAP
SEL
(P.914) set to
ALTERNATE
) and you change the control source
from
NETWORK
, the parameters
SPD
LOOP
PI
INIT
SEL
,
SPD
LOOP
PI
INIT
VAL
,
and
SPD
LOOP
PI
RESET
are reset to their default values (0 for each). Make
sure these values are appropriate for your application before changing
the control source. Failure to observe this precaution could result in
severe bodily injury or loss of life.