System command and status blocks – Rockwell Automation 1771-QDC, D17716.5.93(Passport) PLASTIC MOLDING MODULE User Manual
Page 63
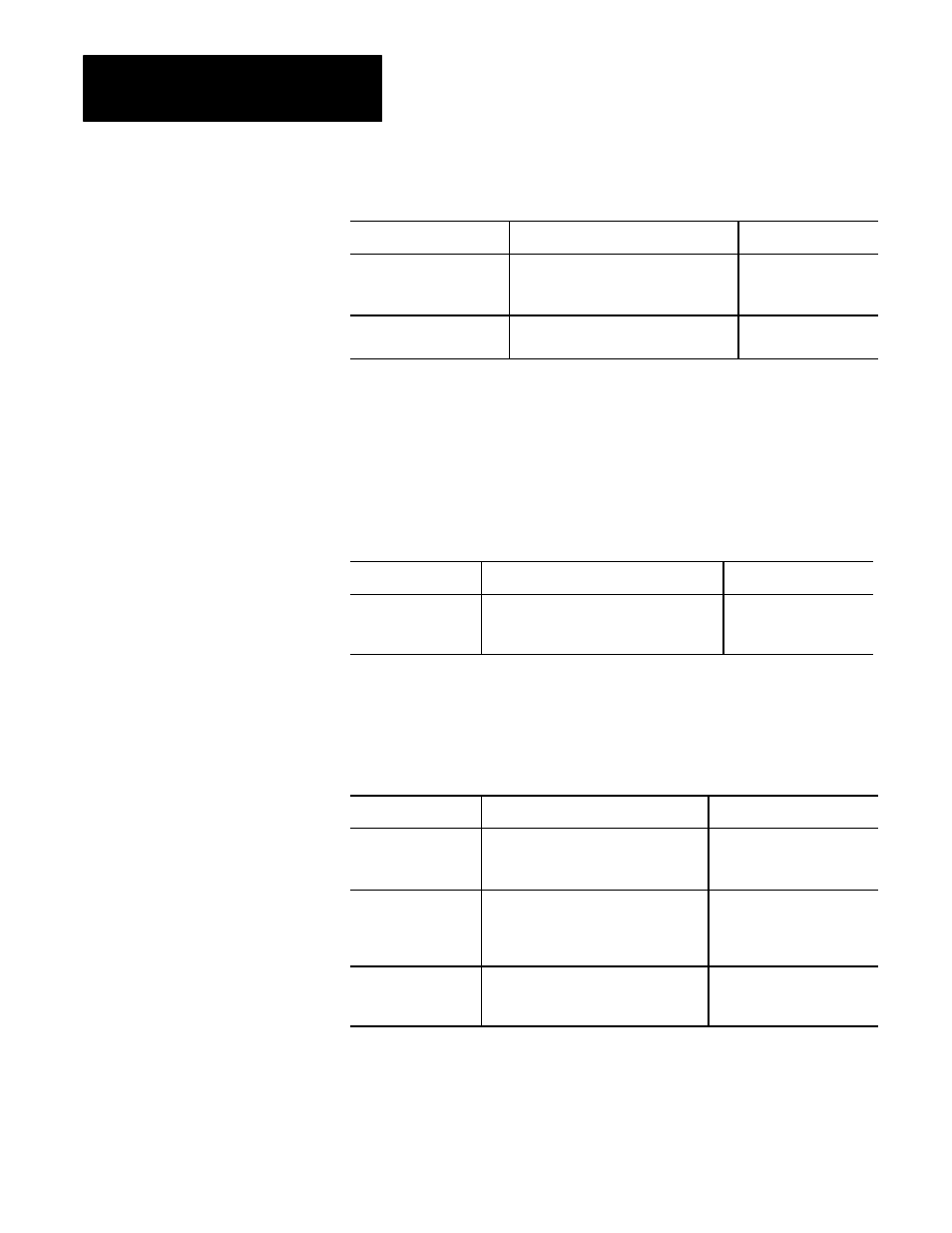
Overview of Remaining
Configuration Procedures
Chapter 4
4-2
There are two types of command blocks, presented in the following table:
Type of Command Block:
Which Contains:
Examples:
Configuration
Information necessary to configure your
module to run a certain portion of a profile.
Valve spanning
information for the 1st
clamp close profile.
Profile
Actual process setpoints necessary to
produce a desired part.
1st clamp close profile
operating setpoints.
Status Blocks
The QDC module returns critical operating status and values to the PLC-5
data table through status blocks. Like configuration blocks, status blocks
are areas of PLC-5 data table. Status blocks, however, contain actual
machine operation information rather than machine setpoints and action
commands.
Type of Block:
Which Contains:
Examples:
Status
Information about machine operation and
QDC module operating status.
The molding machine is
currently performing an
injection operation.
The Module Configuration Block (MCC), Dynamic Command Block
DYC), and the System Status Block (SYS) are system data blocks because
of functions they perform:
Type of Block:
Description:
Examples:
Module Configuration
(MCC)
Contains configuration information used
throughout all phases of machine
operation.
Sensor spanning information
and global alarm setpoints.
Dynamic Command
(DYC)
Includes all commands necessary to jog,
run, and stop any applicable machine
phase or operation.
Command to start the injection
phase.
System Status
(SYS)
Returns to the PLCĆ5 processor
information relevant to common module
parameters.
Actual voltages and
engineering units read at the
four QDC module inputs.
System Command and
Status Blocks