Rockwell Automation 1771-QDC, D17716.5.93(Passport) PLASTIC MOLDING MODULE User Manual
Page 187
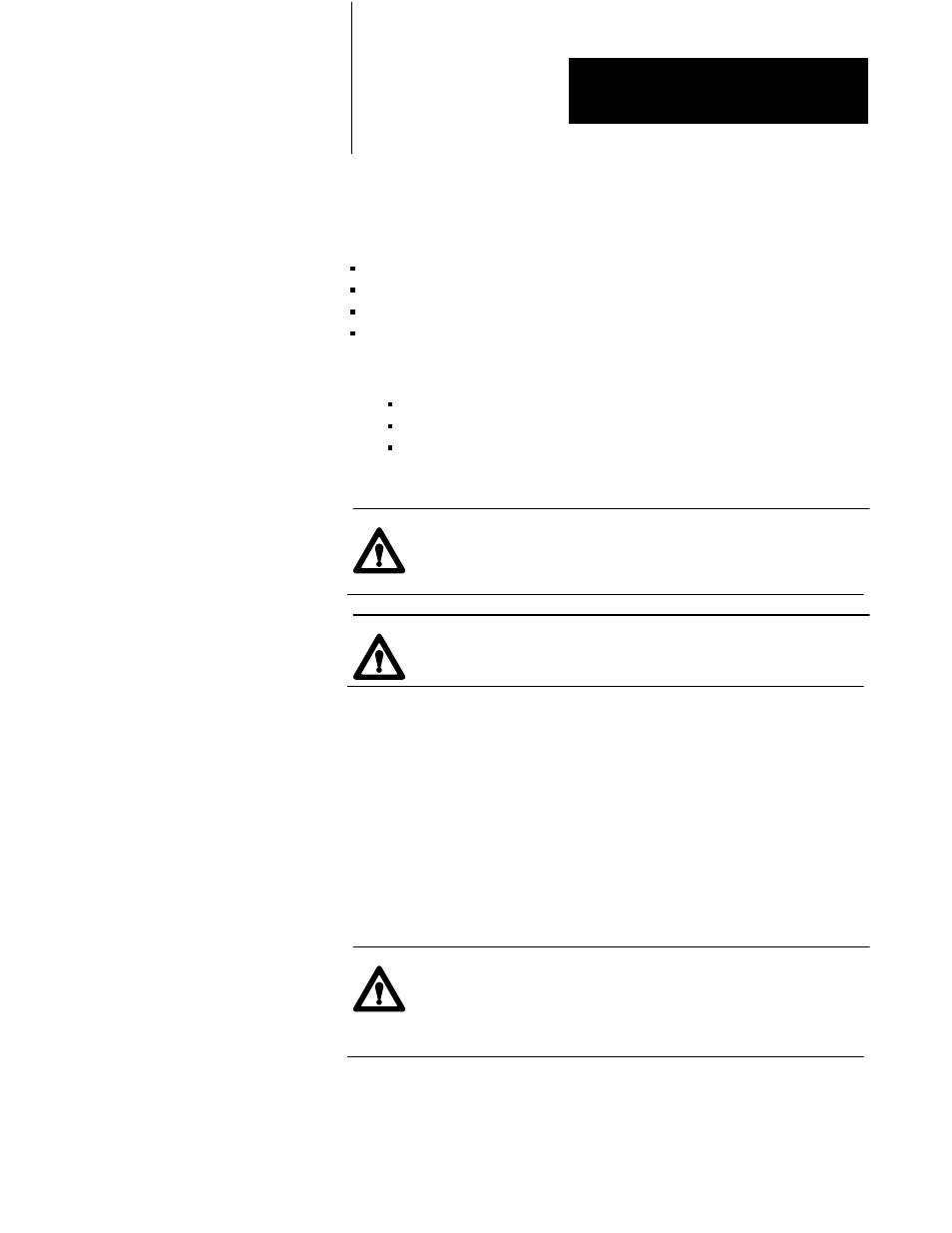
Span Your Valves
Chapter 9
9-21
Span Your Injection Pressure Valve
Span your injection valve for smooth operation at highest desired pressure.
Do this in the following procedure by finding the optimum values for:
Minimum Pressure Control Limit INC41 (N44:37)
Maximum Pressure Control Limit INC42 (N44:38)
Selected Pressure Valve, Output for Minimum INC43 (N44:39)
Selected Pressure Valve, Output for Maximum INC44 (N44:40)
Important: If PanelView is operational for injection profiles, use it to:
observe actuals
change and download setpoints
run profiles
Important: We suggest that you read this procedure before starting.
ATTENTION: As with any machine start-up, install a test
mold. Programming errors, configuration errors, or hydraulic
problems could lead to personal injury and/or machine damage.
ATTENTION: Be sure all machine guards and shields are in
place before proceeding to guard against personal injury.
1.
Manually jog your ram (screw) to the mold-end position so you can
exert maximum pressure against the nozzle tip.
2.
Align all other machine hydraulics to simulate injection: enable
pumps and align valves to their normal injection state.
3.
Copy initial values INC09-12 (N44:5-8) into DYC09-12
(N40:121-124) of your PLC-5 data table with this exception:
Important: Enter a value corresponding to zero pressure into the word
DYC09-12 (N40:121-124) for output 1, 2, 3, or 4 that drives the selected
clamp pressure valve.
ATTENTION: A value of 0 does not always correspond to zero
pressure or flow. For example, a bi-directional valve requires a
set-output value of 50% (5000) to obtain 0 PSI. Valve spools or
amplifier electronics may also allow pressure or flow at 0 volts.