Closed loop tuning, 10ć2 – Rockwell Automation 1771-QDC, D17716.5.93(Passport) PLASTIC MOLDING MODULE User Manual
Page 230
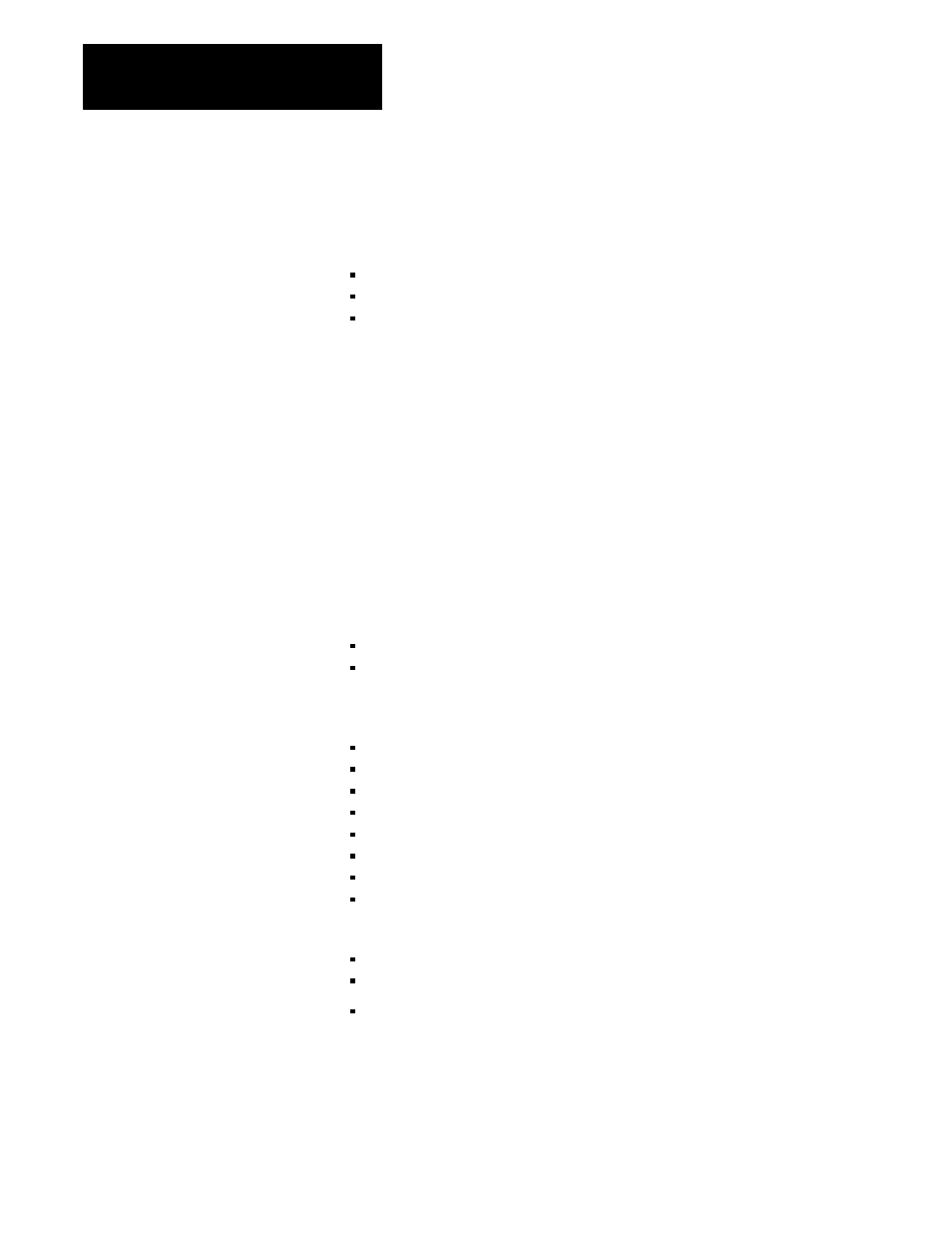
Tune Your Machine
Chapter 10
10-2
ClosedĆloop Control
So far, you have run open-loop profiles with the QDC module’s PID and
VelFF algorithms disabled. We suggest that you use open-loop control:
for spanning valves
for troubleshooting machine performance
when the machine has no pressure sensors for feedback
Important: You can achieve considerably better consistency of finished
parts when the QDC module operates in closed-loop control. With few
exceptions, you should run machine production with closed-loop profiles.
Correctly tuned closed-loop profiles are essential for precise, repeatable
operation. In chapter 7 you entered our recommended values. They may
give you desired machine performance.
Important: If you need to improve performance, continue with this
section. If not, skip to Injection Tuning Considerations for Producing Parts.
General Guidelines for Pressure Tuning
In this section we present two procedures:
Tune Pressure Loops without an Oscilloscope
Tune Pressure Loops with an Oscilloscope
Repeat either one of these procedures as needed for tuning the
pressure-control loop of these profiles:
Injection – Pressure vs. Position or Time
Pack and Hold – Pressure vs. Time
Plastication – Backpressure vs. Position
Clamp Open (3) – Pressure vs. Position
Clamp Open Slow – Pressure vs. Position
Clamp Close (3) – Pressure vs. Position
Low Pressure Close – Pressure vs. Position
Ejector – Pressure vs. Position
Follow these general guidelines when tuning closed-loop pressure profiles:
Disable
ramping
Disable Expert Response Compensation (ERC)
Reset ERC values to zero by setting DYC05-B15 (B34/463) = 1.
(Pro-Set 600 resets this bit to zero after resetting ERC values.)
Important: Gain constants differ between pressure profiles. The
dynamics of loads being moved and different hydraulic characteristics
warrant separate PID tuning considerations for each profile.
ClosedĆloop Tuning