1ć16 – Rockwell Automation 1771-QDC, D17716.5.93(Passport) PLASTIC MOLDING MODULE User Manual
Page 28
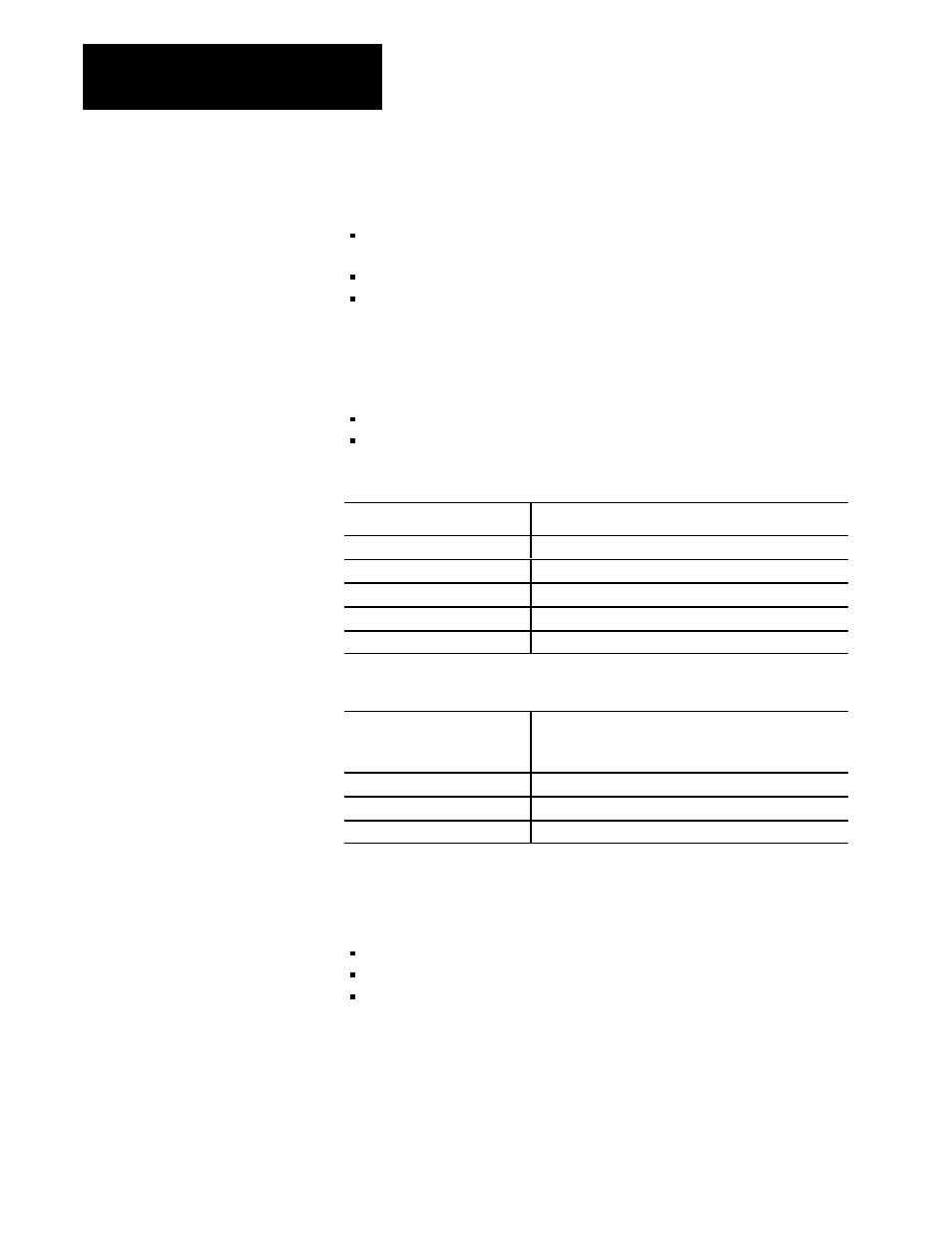
Overview of Inject, Clamp, and Eject Mode
Chapter 1
1-16
Because system pressure may change from one phase to the next, we
recommend that you:
assign pressure control to phases that require pressure profiles
(and are hydraulically plumbed to support it)
place the system pressure sensor accordingly in the hydraulic circuit
configure the remaining phases with velocity profiles
We define open-loop pressure control as when the QDC module controls
phase pressure without input from the system pressure sensor. For example:
when the system pressure sensor monitors the clamp for closed-loop pressure
control, the QDC module can control:
ram (screw) pressure for pack, hold, and plastication in open loop
ejector velocity in closed- or open-loop using a position sensor
For example:
For this Phase
The QDC Module Can Control it With
clamp close and open
closedĆloop pressure
injection
openĆloop pressureĆlimited velocity
pack/hold
openĆloop pressure
plastication
openĆloop pressure
ejector advance and retract
velocity
In general:
If your system pressure sensor
reads pressure for only ONE of
these modes:
Then you must control the other modes by either of:
1. closedĆ or openĆloop velocity
2. openĆloop pressure
inject
clamp, eject
clamp
inject , eject
eject
inject, clamp
We illustrate three examples of hydraulic circuits compatible with the QDC
module in the inject, clamp, and eject mode:
4-valve system with system pressure sensor
3-valve system with ram (screw) pressure sensor
2-valve system for inject phase with clamp and ejector position inputs
(clamp and ejector direction solenoid valves controlled by ladder logic)
Example Hydraulic Circuits
for the Inject, Clamp, and
Eject Mode