Yaskawa VS-626 MC5 User Manual
Page 206
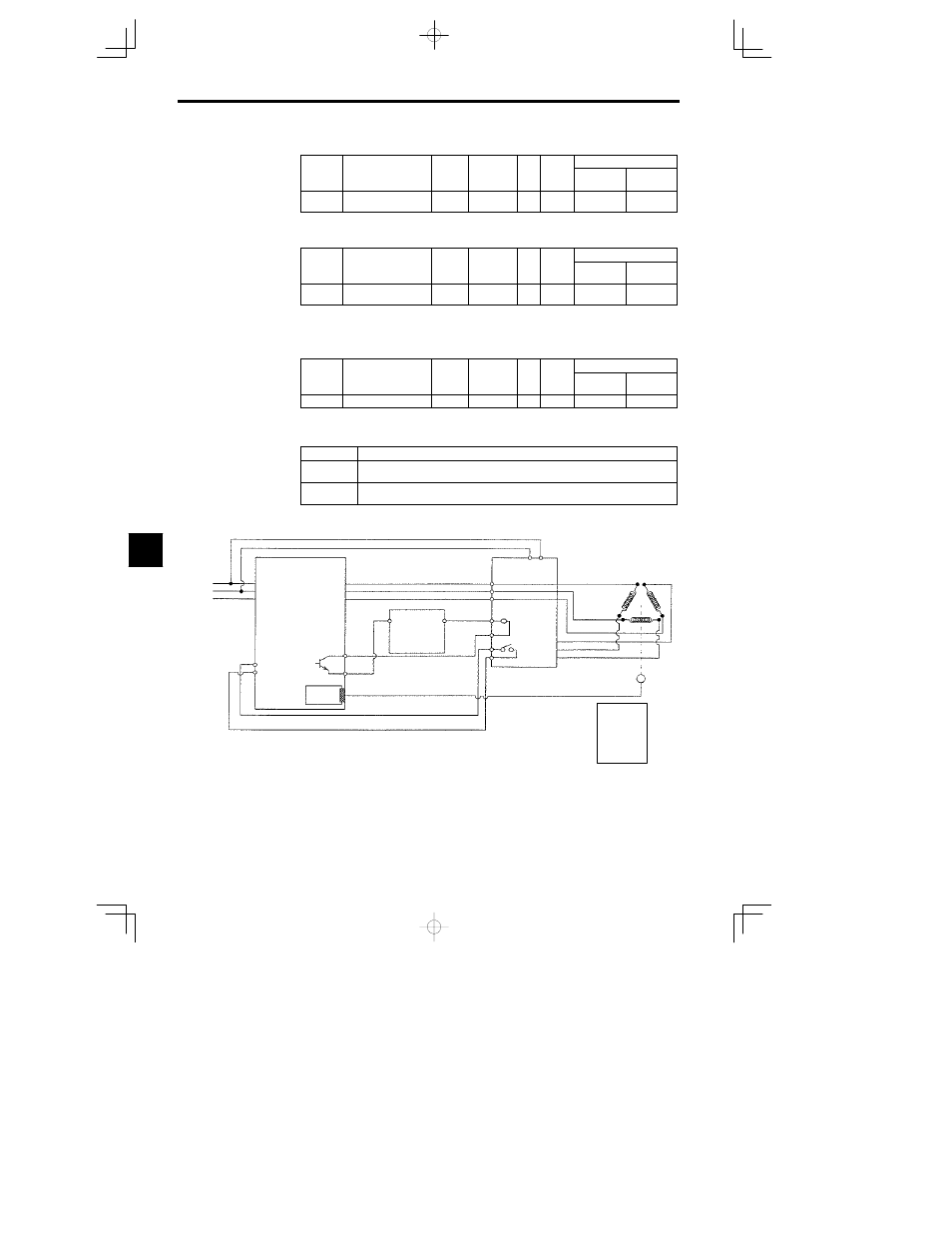
Advanced Operation
7.4.2 Wiring for Winding Change
- 68
Winding change hysteresis: P1-02
User
Change
during
Setting
Factory
Valid Access Levels
User
Constant
Number
Name
during
Opera-
tion
Setting
Range
Unit
Factory
Setting
Open Loop
Vector
Flux Vector
P1-02
Winding change hyster-
esis
0.0 to 20.0
--
5.0
A
A
D
Sets the hysteresis of the winding change frequency.
MC Answerback error detection: P1--03
User
Change
during
Setting
Factory
Valid Access Levels
User
Constant
Number
Name
during
Opera-
tion
Setting
Range
Unit
Factory
Setting
Open Loop
Vector
Flux Vector
P1-03
MC Answerback error
detection
0.20 to 1.00
sec
0.20
A
A
D
This constant determines the waiting time for the MC (Magnetic Contactor) answerback error detec-
tion. Constant setting is valid when one of the multi-function digital inputs (H1-01 to H1-06) has been
set to 81 or 82.
Motor constant selection: P1-04
User
Change
during
Setting
Factory
Valid Access Levels
User
Constant
Number
Name
during
Opera-
tion
Setting
Range
Unit
Factory
Setting
Open Loop
Vector
Flux Vector
P1-04
Motor constant selection
0 1
--
1
A
A
D
Select the motor constants allocated for the types of winding to be used.
D
Settings
Setting
Function
0
Motor 1 constants (E1 E2) are used for Y-winding, and motor 2 constants (E3 E4 E5) are
used for -winding
1
Motor 2 constants (E3 E4 E5) are used for Y-winding, and motor 2 constants (E1 E2) are
used for -winding
Figure 7.38 shows a wiring example of auto-winding change
B1-02 = 4
H1-06 = 82
H2-03 = 41
P1-04 = 1
A1-02 = 3
E3-01 = 3
3
230 V
R
T
S
11
8
U
W
V
26
27
VS--626MC5
1
230 V
0 V
24 V
+24 VDC
Supply
MC Answerback
17 18
2
6
4
13
14
15
16
HV--75AP3
Megnetic Contactor
Dual Winding
Motor
U
Z
X V
Y
W
X
X
PG--X2
Card
(Option)
PG
Fig
7.38
Sample Wiring for Auto-winding Change
7