Yaskawa VS-626 MC5 User Manual
Page 204
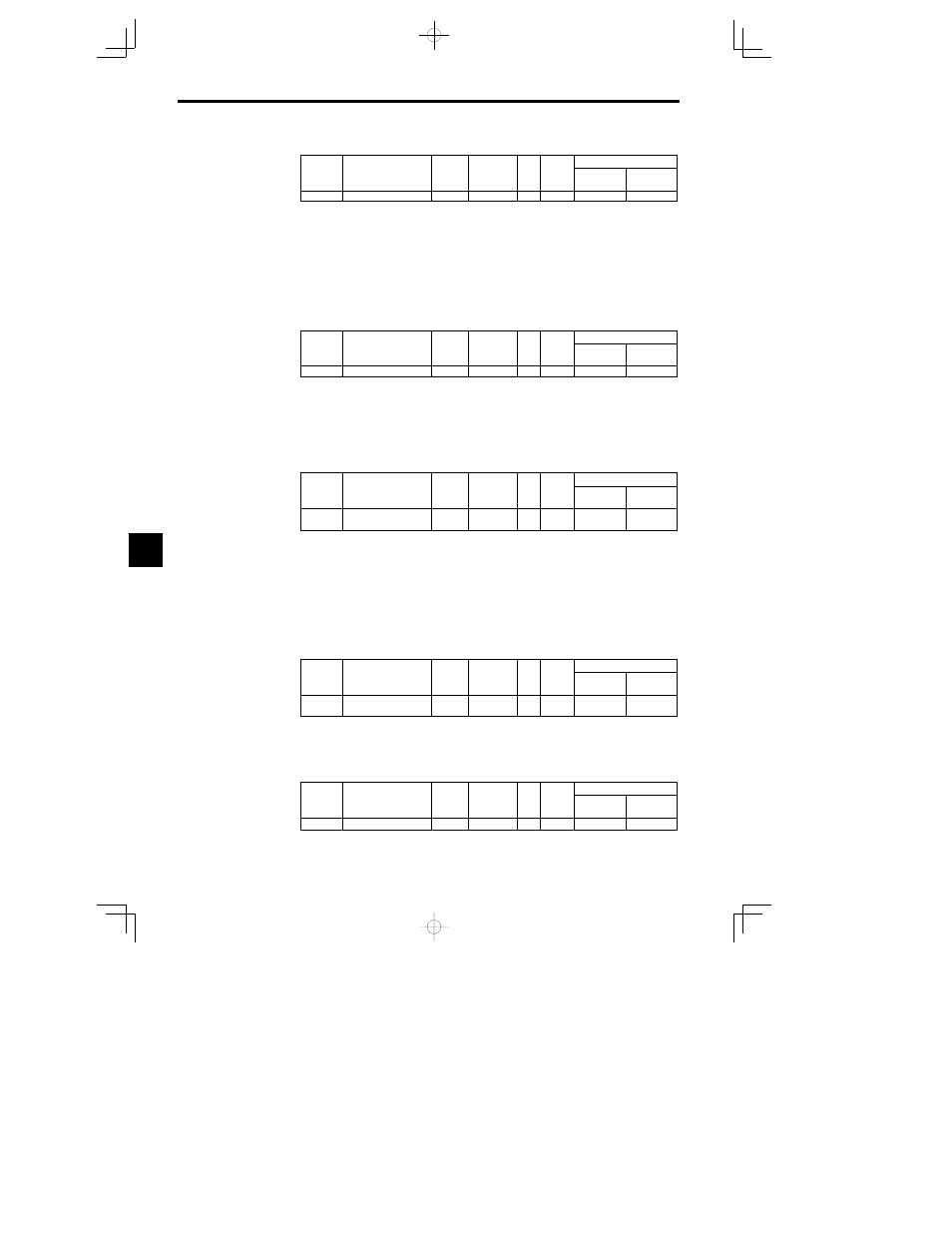
Advanced Operation
7.4.2 Wiring for Winding Change
- 66
Minimum Baseblock Time: L2-03
User
Change
during
Setting
Factory
Valid Access Levels
User
Constant
Number
Name
during
Opera-
tion
Setting
Range
Unit
Factory
Setting
Open Loop
Vector
Flux Vector
L2-03
Min. baseblock time
0.0 to 5.0
s
0.5
B
B
D
The factory setting depends on the Inverter capacity. The factory setting shown in the table is for a
200 V class, 0.4 kW Inverter. (See page NO TAG.)
D
This setting is used with the speed search and DC injection braking functions.
D
Set the time required for the leakage voltage to dissipate. Increase the setting if an overcurrent (OC)
occurs when the speed search or DC injection braking function starts.
D
Set the baseblock time during winding change. Time for winding change varies according to the set-
ting. (For example, lower the setting, and time for winding change is also reduced.) Overcurrent (OC)
might occur if setting is too low.
D
This setting is valid for speed searches performed after a momentary power loss and regular speed
searches.
Voltage Recovery Time: L2-04
User
Change
during
Setting
Factory
Valid Access Levels
User
Constant
Number
Name
during
Opera-
tion
Setting
Range
Unit
Factory
Setting
Open Loop
Vector
Flux Vector
L2-04
Voltage recovery time
0.0 to 5.0
s
0.3
A
A
D
Set the time allowed for the normal voltage to be restored after completion of the speed search.
For a 200 V class Inverter, this is the time in seconds for voltage to be restored from 0 VAC to 200 VAC.
For a 400 V class Inverter, this is the time in seconds for voltage to be restored from 0 VAC to 400 VAC.
D
This setting is valid for speed searches after a momentary power loss, regular speed searches, the volt-
age changes with energy-saving control, and the voltage changes with baseblock clearing.
D
Set the voltage recovery time after baseblock during winding change. Ovrevoltage (OV) might occur
if setting is too low.
Speed Search Deceleration Time: b3-03
User
Change
during
Setting
Factory
Valid Access Levels
User
Constant
Number
Name
during
Opera-
tion
Setting
Range
Unit
Factory
Setting
Open Loop
Vector
Flux Vector
b3-03
Speed search decelera-
tion time
0.1
10.0
s
2.0
A
D
Set output frequency deceleration time during speed search. (Set the time to decelerate from the max.
output frequency to OHz.)
7.4.2 Wiring for Winding Change
The VS-626MC5 offers two different types of winding changes, external winding change and auto- wind-
ing change. W-winding and -winding can be set independently using constants for motor 1 and 2.
J
External Winding Change Method
In this method, an external signal is given to one of the multi-function inputs (set as “80H”) to start the
winding change. The external signal is given from the CNC.
MC Answerback error detection
:
P1-03
User
Change
during
Setting
Factory
Valid Access Levels
User
Constant
Number
Name
during
Opera-
tion
Setting
Range
Unit
Factory
Setting
Open Loop
Vector
Flux Vector
P1-03
MC Answerback error
detection
0.20 to 1.00
sec
0.20
A
A
D
This constant determines the waiting time for the MC (Magnetic Contactor) answerback error detec-
tion.
D
Setting is valid when one of the multi-function digital inputs (H1-01 to H1-06) has been set to 81 or
82.
Motor constant selection: P1-04
User
Change
during
Setting
Factory
Valid Access Levels
User
Constant
Number
Name
during
Opera-
tion
Setting
Range
Unit
Factory
Setting
Open Loop
Vector
Flux Vector
P1-04
Motor constant selection
0 1
--
1
A
A
D
Select the motor constants allocated for the types of winding to be used.
7