Yaskawa MotionWorks IEC Hardware User Manual
Page 136
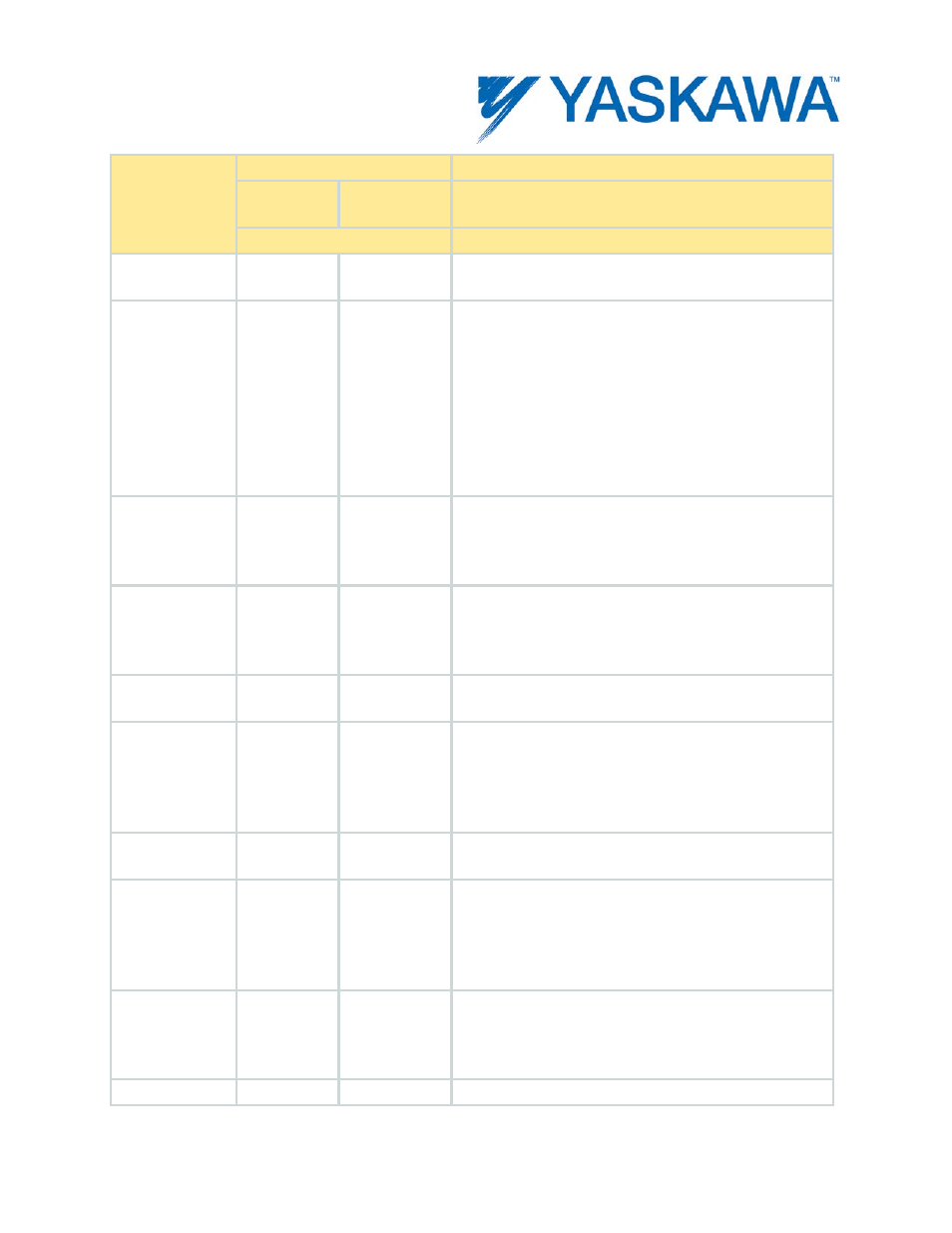
MotionWorks IEC Hardware Configuration – 2013-03-26
133
Hex Code
Description
ErrorClass
AxisErrorID
ErrorClass+AxisErrorID output from
MC_ReadAxisError
AlarmID
AlarmID output from Y_ReadAlarm
motionKernel
3202
0051
Axis enable failed. This problem is usually a result of
communication problems with the servo drive.
motionKernel
3202
0052
Runtime computation detected an invalid motion
parameter. This alarm ID can occur if a discrete move
has to be completed but the commanded deceleration
for that move is not sufficient. For example if a
MC_MoveAbsolute aborts another move and the axis
has to stop at a position that will come up in a couple
of scans, but the deceleration input on the
MC_MoveAbsolute is not high enough to make the
desired profile, this alarm will occur.
motionKernel
3202
0061
The axis Positive Overtravel (P-OT) limit has been
exceeded. Motion is prevented in the positive direction.
The axis may not be moved again until the alarm
condition is cleared.
motionKernel
3202
0062
The axis Negative Overtravel (N-OT) limit has been
exceeded. Motion is prevented in the negative
direction. The axis may not be moved again until the
alarm condition is cleared.
motionKernel
3202
0100
The inverse kinematics computation detected a world
position that can not be reached.
motionKernel
3202
0101
The inverse kinematics computation detected that the
elbow 'handedness' (orientation) does not match the
configuration. The 'handedness' must be fixed by
commanding the individual axes or manually moving
the robot.
motionKernel
3202
0102
The robot XY position intruded into the configured dead
zone area near the origin.
Mechatrolink
3301
0009
Some motor properties, such as encoder resolution,
maximum speed, and maximum torque, could not be
determined for the attached motor. The serial encoder
may be malfunctioning, incorrectly programmed, or
unplugged.
Mechatrolink
3301
000B
Setting of Pn002, digits 3 and 4, disables torque limit
and/or velocity limit in velocity and/or torque control
modes. Set Pn002 = xx11 to initialize. Saving in the
Hardware Configuration will automatically set Pn002.
Mechatrolink
3301
000D
The servo network does not support this motion control