Wbk16 – user tips – Measurement Computing WBK Options User Manual
Page 76
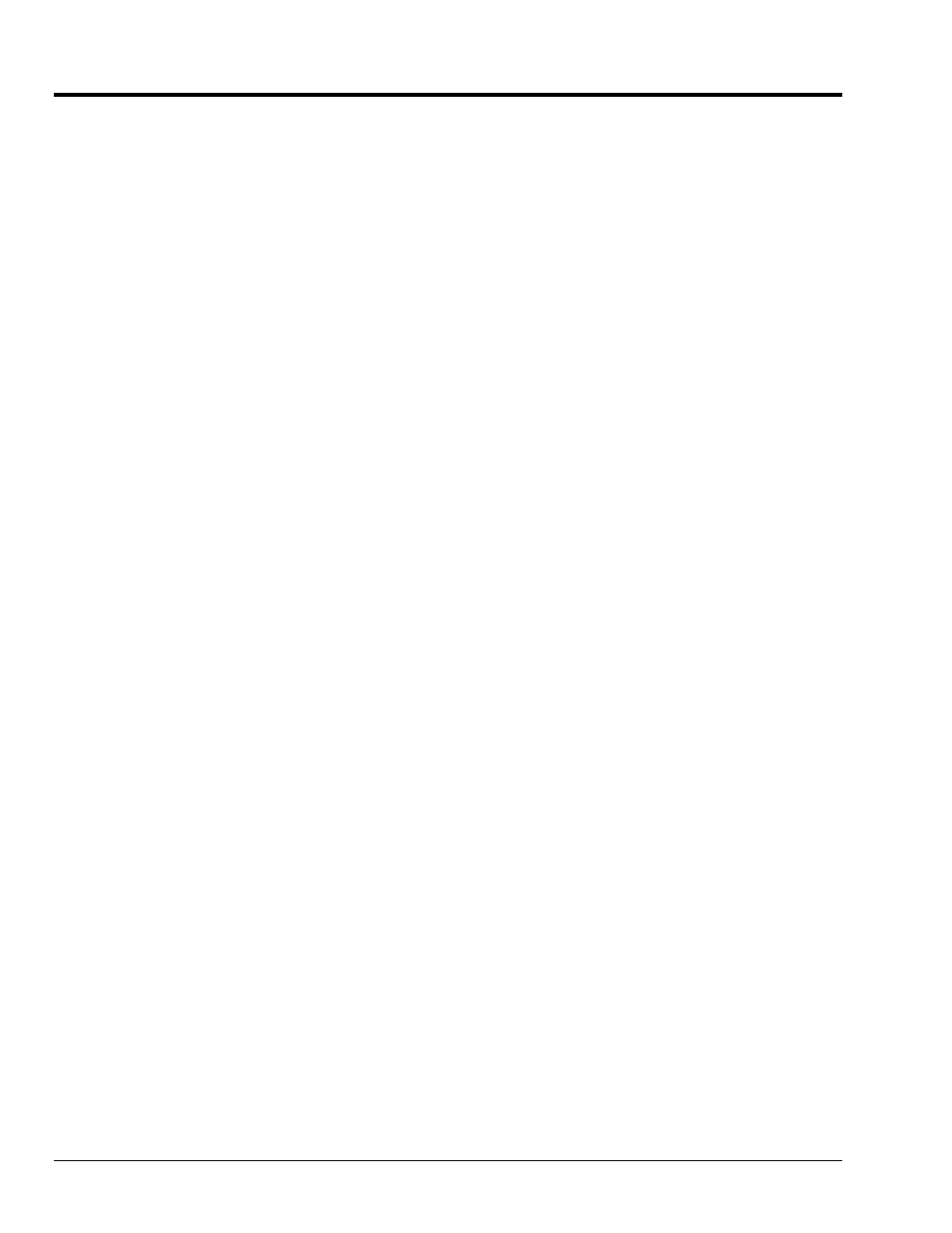
WBK16, pg. 36
949794
WBK16, Strain-Gage Module
WBK16 – User Tips
There are some aspects of the WBK16 that can cause user difficulties if misunderstood. The following
tips should increase your level of understanding and help you get the most out of your WBK16.
(1) Keep things cool.
Operating 120 ohm bridges on 10 volts of excitation is possible with the WBK16 but the strain gages and
bridge completion resistors must both be rated for this voltage or there will be excessive drift as the gages
and resistors heat up. The 120 ohm bridge completion resistors we offer (part number R-17-120) are of
insufficient power rating for 10 volt bridges. If the excitation level is set to 5 volts, drift is not a problem
with our 120 ohm resistors. An alternative is to purchase higher quality, higher power and higher cost
bridge completion resistors (part number S-120-01) from the Measurement Group.
(2) Understand the difference between calibration and set-up.
Calibration requires measurements of channels with external wiring and gages connected to establish
computational data on which to base gain and offset settings. The two-point manual and shunt cal menu
choices provide calibration. Set-up uses manually entered parameters to computationally choose gain and
offset settings. The two-point automatic and nameplate menu choices provide channel set-up.
The nameplate menu selection for strain gages cannot effectively calibrate field configured strain gage
bridges which have not been externally hardware nulled because the software algorithm assumes the zero
point and computes the other settings based on the excitation voltage, gage factor and full scale value
entered by the user. Nameplate “calibration” is intended for packaged and pre-calibrated devices, such as
load cells and pressure transducers with nameplates listing their output sensitivity in mV/V and full-scale
output in engineering units.
(3) Do not attempt to “calibrate” all the channels simultaneously.
Although desirable, it is not possible, to globally calibrate all the channels without making any actual
measurements. It is possible to apply global auto-zero to previously calibrated channels that have auto-zero
enabled. However, the original requirement for the channel to have been externally nulled, prior to
performing nameplate calibration remains. The overall settings for all of the channels can be stored as a
configuration for re-use, but assuming the overall calibration and external system are unchanged between
chronologically separated tests is risky and not recommended.
(4) Know an unbalanced bridge when you configure one.
Theoretically, a strain gage bridge is balanced with zero output until strain is applied producing an output
voltage linearly proportional to the strain. In the real world, the bridge is slightly unbalanced due to
component tolerances. There are two approaches to allow accurate strain measurements with the slightly
unbalanced bridge, (1) balance the bridge, or (2) compensate for the error with correction factors.
Understand that if you do neither, the bridge will provide erroneous results.
(5) Take it easy on the excitation regulators.
The excitation outputs of the WBK16 will deliver up to 90 mA without any degradation in output voltage.
If this level of current is exceeded, the voltage is reduced to protect the regulator. It is important to
consider the current drawn by the internal reference node resistors. These resistors are never switched off,
they continue to load the excitation regulator no matter what bridge configuration is chosen. If these
resistors are 120 ohm resistors, which they never really need to be, they draw 41.7 milliamps at 10 volts.
An external full bridge of 120 ohm resistors, and requiring an additional 83.3 milliamps will definitely
overload the regulator and result in a reduced excitation level and an incorrect signal level. For two
reasons, the best choice for the reference node resistors is 1000 ohms. The parts will draw less excitation
current, helping the regulators and the lower degree of self-heating will result in less drift.