Arcglide communication, Hypernet communication – Hypertherm THC ArcGlide User Manual
Page 48
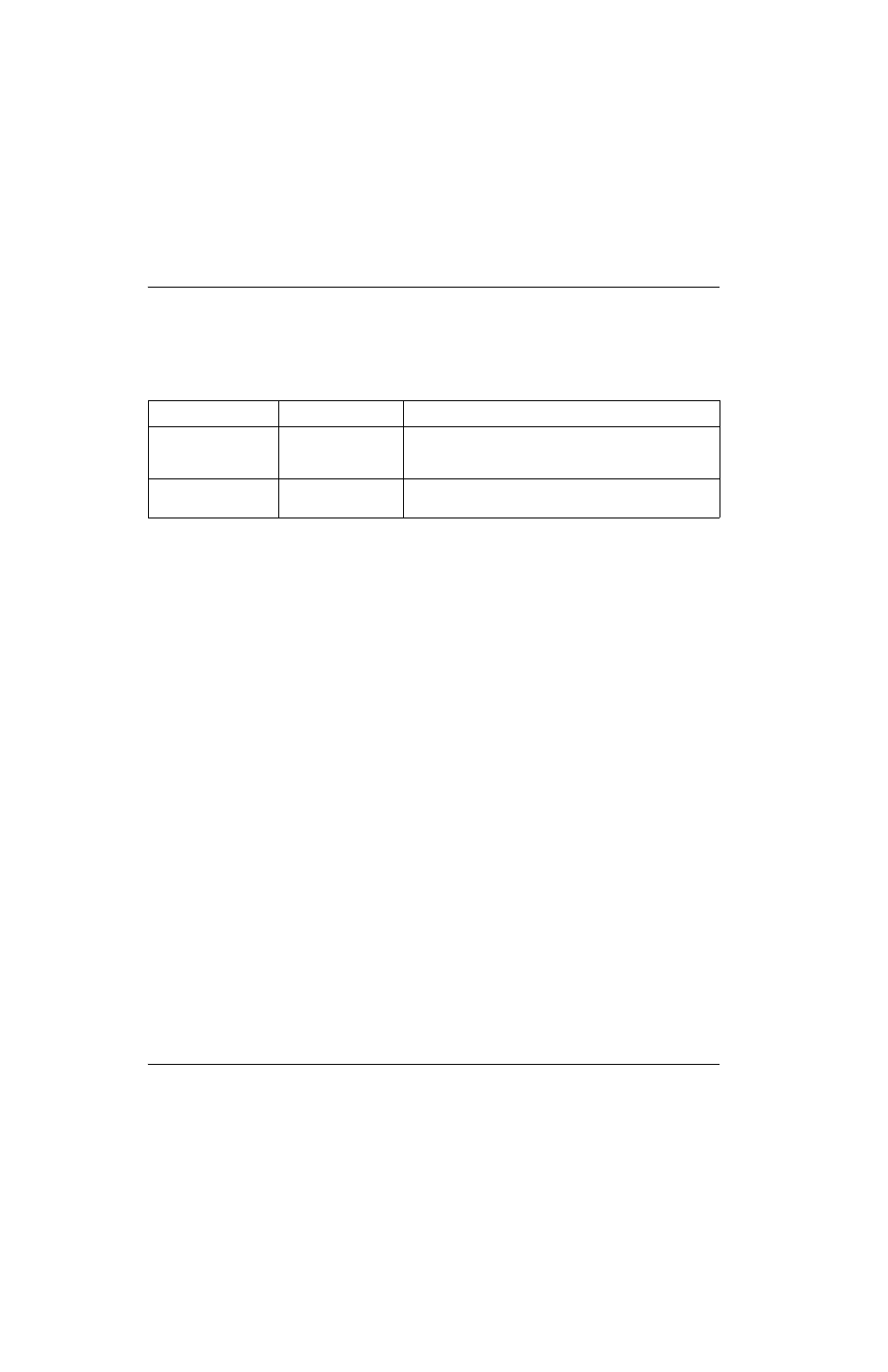
48
ArcGlide THC Instruction Manual 806450
1 – Specifications
ArcGlide communication
Figure 7 through Figure 10 show discrete and Hypernet communication that the ArcGlide THC uses to exchange signals
with the CNC and the plasma system. Use the following table to distinguish between discrete and Hypernet
communication.
Both communication styles transmit the same signals. The difference is in the way the signals are “packaged” for
transmission over the two cabling configurations.
Do not use redundant (both discrete and Hypernet) communication between the same two components in the same
ArcGlide configuration.
Hypernet communication
ArcGlide THCs in Hypernet configurations connect to the CNC and plasma system using the Hypernet protocol over
shielded, Ethernet Cat5e or Cat6 cables. Both the CNC and plasma systems in this configuration must have a dedicated,
Hypernet-configured, Ethernet port for these connections.
In addition, a Hypernet configuration must include an industrial-grade Ethernet switch to route communication from the
CNC to the other components in the system.
Each ArcGlide THC component (HMI, control module, and plasma interface board) that is connected to the Hypernet
must have the same Hypernet component address. This address must correspond to the station number for the THC
that is selected in Phoenix, on the Station Configuration screen. See
Assign an ArcGlide THC to a station on page 125
for more information.
Communication style
Data architecture
Cabling configuration
Discrete
Discrete I/O and serial
data
A dedicated cable to each component from the ArcGlide control
module; within each cable, there is a dedicated wire for each
signal.
Hypernet
Ethernet data packets
A standard, Cat5e or Cat6, shielded, Ethernet cable from the
Ethernet switch to each component of the cutting machine.