Rockwell Automation Liqui-Flo V2.0 AC Drive User Manual
Page 217
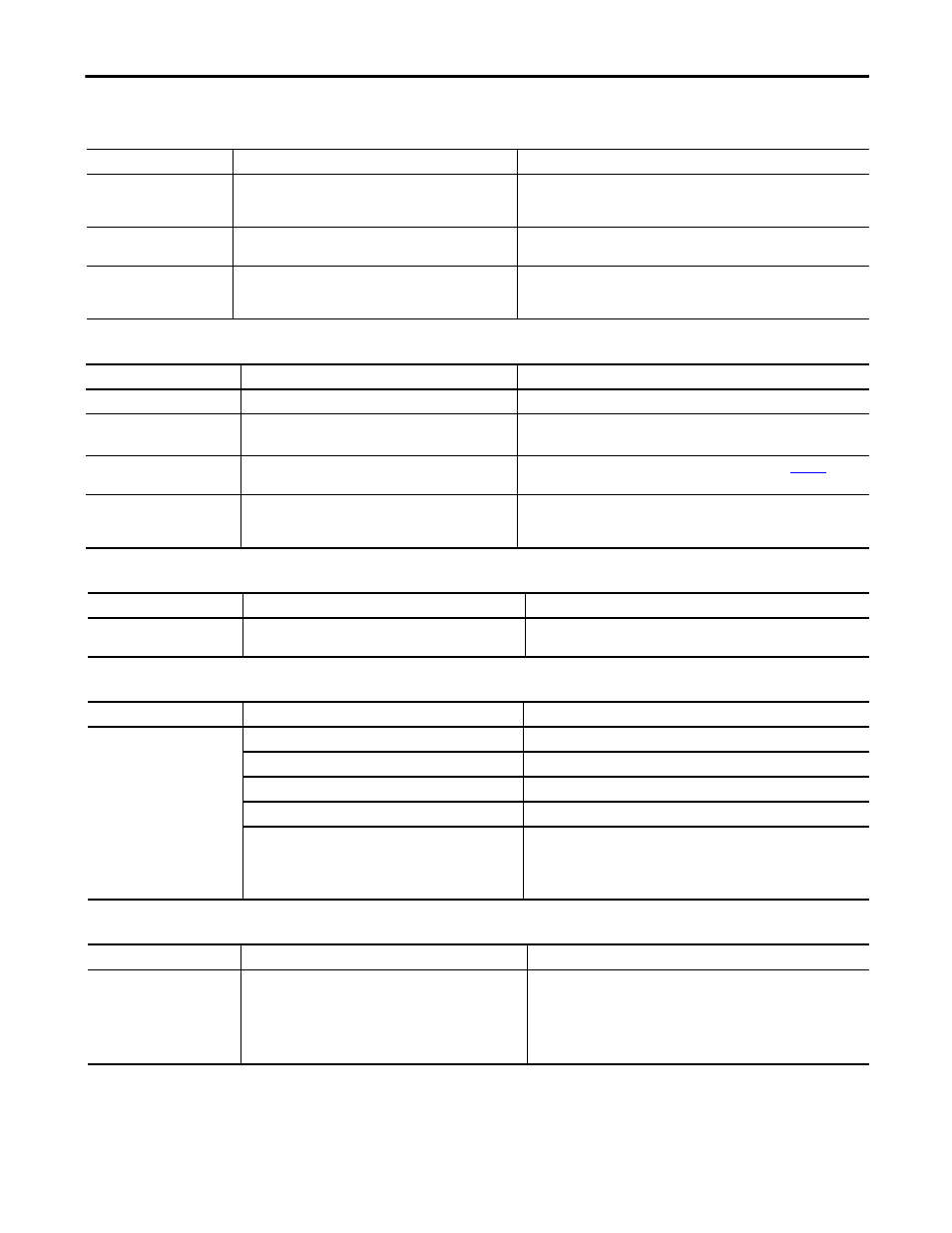
Rockwell Automation Publication D2-3518-3 - May 2013
217
Chapter 10
Table 26 - Drive Does Not Respond to Changes in Speed Command
Table 27 - Motor and/or Drive Does Not Accelerate to Commanded Speed
Table 28 - Motor Operation is Unstable
Table 29 - Drive Does Not Reverse Motor Direction
Table 30 - Stopping the Drive Results in a Decel Inhibit Fault
Indication
Cause(s)
Corrective Action
OIM Status Line indicates At
Speed and output is 0 Hz.
No value is coming from the source of the command.
1. If the source is an analog input, check wiring and use a meter to check for
presence of signal.
2. Check Commanded Freq (2) for correct source.
None
Incorrect reference source has been programmed.
1. Check Speed Ref Source (213) for the source of the speed reference.
2. Reprogram Speed Ref A Sel (90) for correct source.
None
Incorrect reference source is being selected via remote device or
digital inputs.
1. Check Drive Status 1 (209), bits 12...15 for unexpected source selections.
2. Check Dig In Status (216) to see if inputs are selecting an alternate source.
3. Reprogram digital inputs to correct Speed Sel x option.
Indication
Cause(s)
Corrective Action
Acceleration time is excessive.
Incorrect value in Accel Time x (140, 141).
Reprogram Accel Time x (140, 141).
Drive is forced into current limit,
slowing or stopping acceleration.
Excess load or short acceleration time.
Check Drive Status 2 (210), bit 10 to see if the drive is in current limit.
Remove excess load or reprogram Accel Time x (140, 141).
Speed command source or value
is not as expected.
Improper speed command.
Check for the proper speed command using steps 1...7 in table
Programming is preventing the
drive output from exceeding
limiting values.
Incorrect programming.
Check Maximum Speed (82) and Maximum Freq (55) to insure that speed is not
limited by programming.
Indication
Cause(s)
Corrective Action
None
Motor data was incorrectly entered or autotune was not
performed.
1. Correctly enter motor nameplate data.
2. Perform static or rotate autotune procedure (61).
Indication
Cause(s)
Corrective Action
None
Digital input is not selected for reversing control.
Check Digital Inx Sel. Choose correct input and program for reverse.
Digital input is incorrectly wired.
Check input wiring.
Direction Mode (190) parameter is incorrectly programmed.
Reprogram Direction Mode (190) for analog bipolar or digital unipolar control.
Motor wiring is improperly phased for reverse.
Switch two motor leads.
A bipolar analog speed command input is incorrectly wired or
signal is absent.
1. Use meter to check that an analog input voltage is present.
2. Check wiring.
Positive voltage commands forward direction.
Negative voltage commands reverse direction.
Indication
Cause(s)
Corrective Action
Decel Inhibit fault screen.
LCD status line indicates Faulted.
The bus regulation feature is enabled and is halting deceleration
due to excessive bus voltage. Excess bus voltage is normally due
to excessive regenerated energy or unstable AC line input
voltages.
Internal timer has halted drive operation.
1. Reprogram bus regulation (parameters 161 and 162) to eliminate any
Adjust Freq selection.
2. Disable bus regulation (parameters 161 and 162) and add a dynamic
brake.
3. Correct AC input line instability or add an isolation transformer.
4. Reset drive.