Proportional plus integral (pi) control, Dead band, Pid control – Watlow EZ-ZONE PM PID User Manual
Page 99: Positive dead band
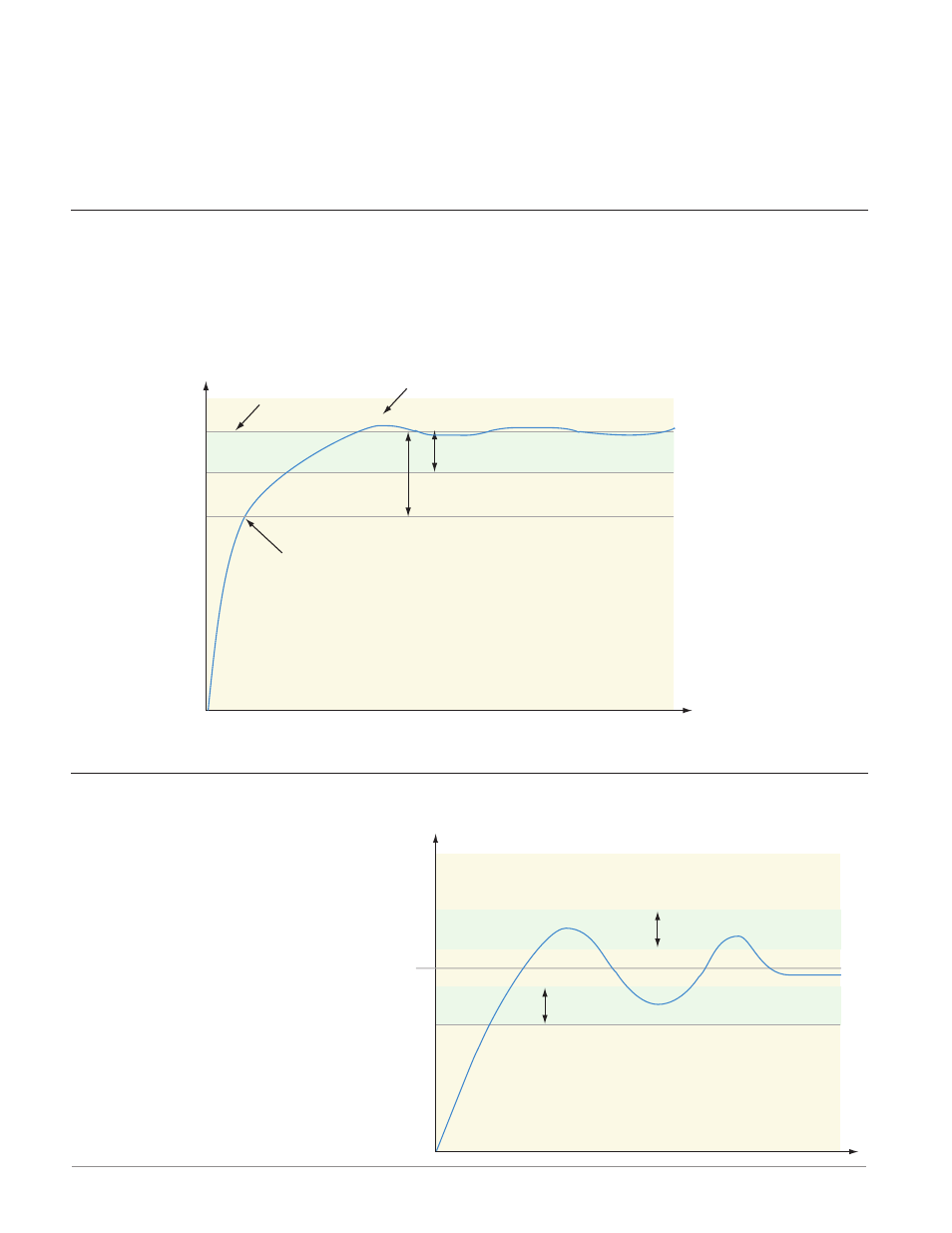
Watlow EZ-ZONE
®
PM PID Controller
•
96
•
Chapter 9 Features
Proportional plus Integral (PI) Control
The droop caused by proportional control can be corrected by adding integral (reset) control. When the sys-
tem settles down, the integral value is tuned to bring the temperature or process value closer to the set point.
Integral determines the speed of the correction, but this may increase the overshoot at startup or when the
set point is changed. Too much integral action will make the system unstable. Integral is cleared when the
process value is outside of the proportional band.
Adjust the integral with Time Integral [``ti] (Operations Page, Loop Menu).
Proportional plus Integral plus Derivative (PID) Control
Use derivative (rate) control to minimize the overshoot in a PI-controlled system. Derivative (rate) adjusts the
output based on the rate of change in the temperature or process value. Too much derivative (rate) will make
the system sluggish.
Derivative action is active only when the process value is within twice the proportional value from the set
point.
Adjust the derivative with Time Derivative [``td] (Operations Page, Loop Menu).
Dead Band
In a PID application the dead bands above and below the set point can save an application’s energy and wear
by maintaining process temperature within ac-
ceptable ranges.
Proportional action ceases when the process
value is within the dead band. Integral action
continues to bring the process temperature to
the set point.
Using a positive dead band value keeps
the two systems from fighting each other.
Time
Temperature
PID Control
Set Point
Reduced Overshoot
Proportional Band
Proportional Band x 2
Heating Slows
Time
Temperature
Positive Dead Band
Set Point
Heat Output Active
Cool Output Active