Watlow EZ-ZONE PM PID User Manual
Page 112
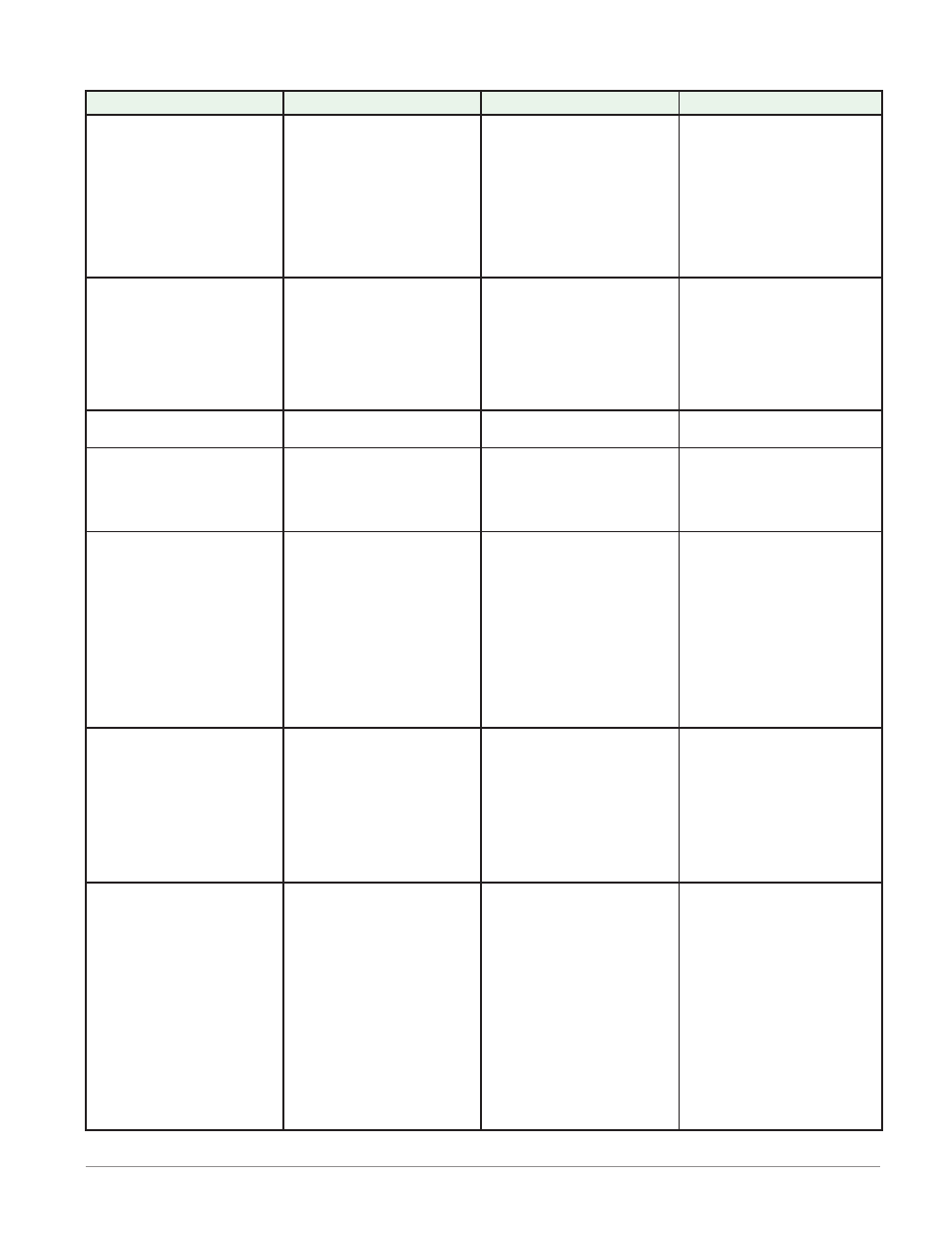
Watlow EZ-ZONE
®
PM PID Controller
•
109
•
Appendix
Indication
Description
Possible Causes
Corrective Action
[LP;o1]
Loop Open Error
Open Loop Detect is active and
the process value did not devi-
ate by a user-selected value in
a user specified period.
• Setting of Open Loop Detect
Time incorrect
• Setting of Open Loop Detect
Deviation incorrect
• Thermal loop is open
• Open Loop Detect function not
required but activated
• Set correct Open Loop Detect
Time for application
• Set correct Open Loop Devia-
tion value for application
• Determine cause of open ther-
mal loop: misplaced sensors,
load failure, loss of power to
load, etc.
• Deactivate Open Loop Detect
feature
[LP;r1]
Loop Reversed Error
Open Loop Detect is active and
the process value is headed
in the wrong direction when
the output is activated based
on deviation value and user-
selected value.
• Setting of Open Loop Detect
Time incorrect
• Setting of Open Loop Detect
Deviation incorrect
• Output programmed for incor-
rect function
• Thermocouple sensor wired in
reverse polarity
• Set correct Open Loop Detect
Time for application
• Set correct Open Loop Devia-
tion value for application
• Set output function correctly
• Wire thermocouple correctly,
(red wire is negative)
[`rP1]
Ramping 1
Controller is ramping to new set
point
• Ramping feature is activated • Disable ramping feature if not
required
[tUN1]
Autotuning 1
Controller is autotuning the con-
trol loop
• User started the autotune
function
• Digital input is set to start
autotune
• Wait until autotune completes
or disable autotune feature
• Set digital input to function
other than autotune, if desired
No heat/cool action
Output does not activate load
• Output function is incorrectly
set
• Control mode is incorrectly set
• Output is incorrectly wired
• Load, power or fuse is open
• Control set point is incorrect
• Incorrect controller model for
application
• Set output function correctly
• Set control mode appropriately
(Open vs Closed Loop)
• Correct output wiring
• Correct fault in system
• Set control set point in appro-
priate control mode and check
source of set point: remote, idle,
profile, closed loop, open loop
• Obtain correct controller model
for application
No Display
No display indication or LED il-
lumination
• Power to controller is off
• Fuse open
• Breaker tripped
• Safety interlock switch open
• Separate system limit control
activated
• Wiring error
• Incorrect voltage to controller
• Turn on power
• Replace fuse
• Reset breaker
• Close interlock switch
• Reset limit
• Correct wiring issue
• Apply correct voltage, check
part number
No Serial Communication
Cannot establish serial commu-
nications with the controller
• Address parameter incorrect
• Incorrect protocol selected
• Baud rate incorrect
• Parity incorrect
• Wiring error
• EIA-485 converter issue
• Incorrect computer or PLC
communications port
• Incorrect software setup
• Termination resistor may be
required
• Set unique addresses on net-
work
• Match protocol between devices
• Match baud rate between de-
vices
• Match parity between devices
• Correct wiring issue
• Check settings or replace con-
verter
• Set correct communication port
• Correct software setup to match
controller
• Place 120 Ω resistor across
EIA-485 on last controller
Troubleshooting Alarms, Errors and Control Issues (cont .)