Yaskawa Z1000U HVAC Matrix Bypass User Manual
Z1000u hvac matrix bypass, Technical manual, Low harmonic drive bypass for hvac applications
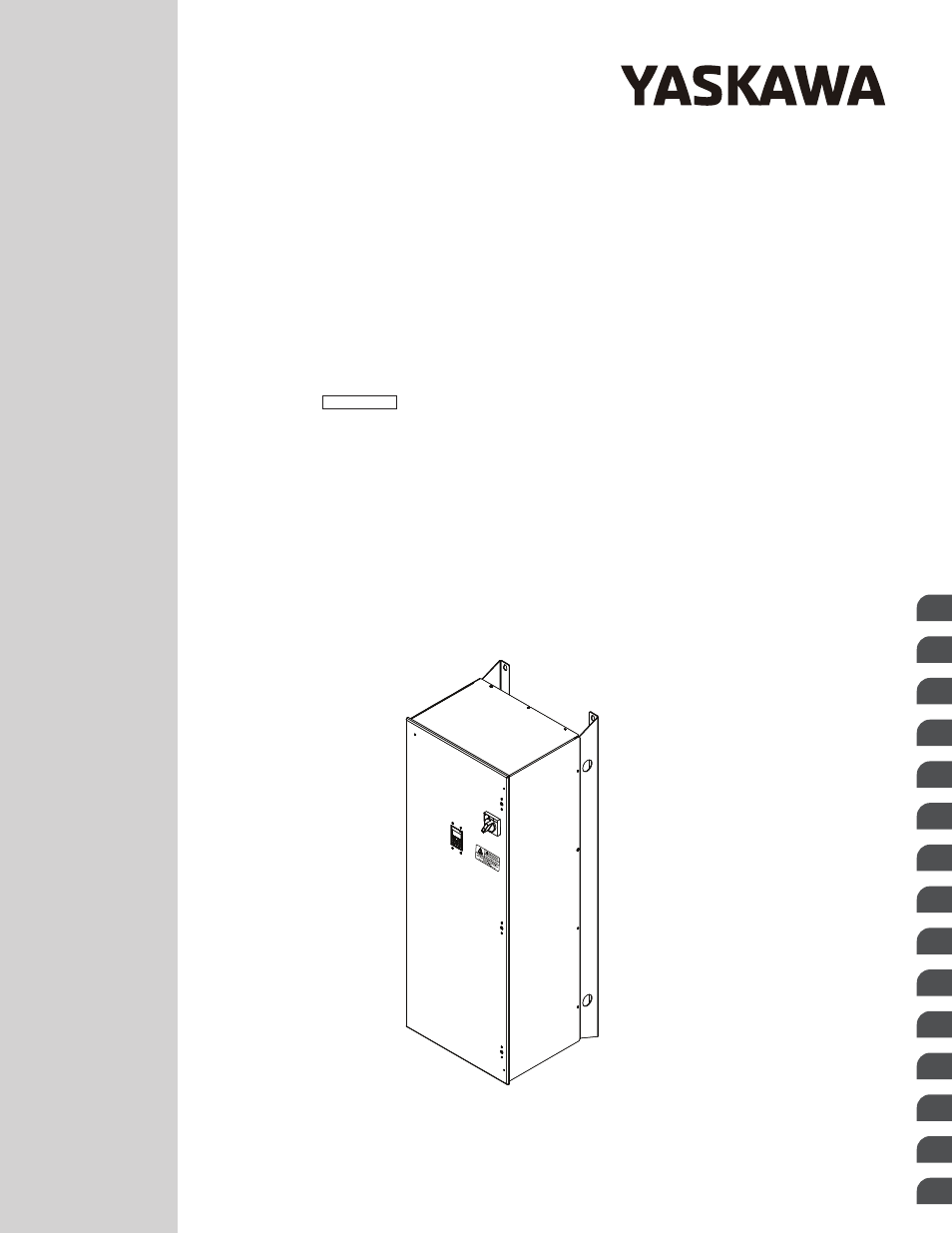
MANUAL NO. SIEP YAIZ1D 01A
Models: 208 V: 7.5 to 75 HP
480 V: 7.5 to 350 HP
To properly use the product, read this manual thoroughly and retain
for easy reference, inspection, and maintenance. Ensure the end user
receives this manual.
Type: Z1D1
Receiving
1
Mechanical Installation
2
Electrical Installation
3
Start-Up Programming &
Operation
4
Programming
5
Diagnostics &
Troubleshooting
6
Periodic Inspection &
Maintenance
7
Specifications
A
Parameter List
B
BACnet Communications
C
MEMOBUS/Modbus
Communications
D
Apogee FLN Network
Protocol
E
Metasys N2 Network
Protocol
F
Standards Compliance
G
Quick Reference Sheet
H
Z1000U HVAC MATRIX Bypass
Low Harmonic Drive Bypass for HVAC Applications
Technical Manual
Table of contents
Document Outline
- Quick Start Procedure
- Preface & General Safety
- Receiving
- Mechanical Installation
- Electrical Installation
- Section Safety
- Standard Connection Diagram
- Main Circuit Wiring
- Input and Output Power Wiring Connections
- Control Circuit Wiring
- Control Circuit Connection Diagram
- Control Circuit Terminal Block Functions
- Bypass Analog Outputs
- Serial Communications
- Drive Cover Removal
- Drives in Bypass Models D024 to D114 and B011 and B124
- Drives in Bypass Models D143 to D211 and B156 to B414
- Removing/Reattaching the Front Cover
- Wiring the Drive Control Circuit Terminal
- Switches and Jumpers on the Terminal Board
- Bypass and Drive Control I/O Connections
- External Interlock
- Start-Up Programming & Operation
- Programming
- Diagnostics & Troubleshooting
- Section Safety
- Motor Performance Fine-Tuning
- Drive Alarms, Faults, and Errors
- Fault Detection
- Alarm Detection
- Operator Programming Errors
- Auto-Tuning Fault Detection
- Diagnosing and Resetting Faults
- Troubleshooting without Fault Display
- Common Problems
- Cannot Change Parameter Settings
- Motor Does Not Rotate Properly after Pressing AUTO Button orafter Entering External Run Command
- Motoris Too Hot
- oPE02 Error Occurs When Lowering the Motor Rated Current Setting
- Motor Stalls during Acceleration or Acceleration Time is TooLong
- Drive Frequency Reference Differs from the Controller FrequencyReference Command
- Excessive Motor Oscillation and Erratic Rotation
- Deceleration Takes Longer than Expected
- Noise From Drive or Motor Cables When the Drive is PoweredOn
- Ground Fault Circuit Interrupter (GFCI) Trips During Run
- Connected Machinery Vibrates When Motor Rotates
- PID Output Fault
- Motor Rotates after the Drive Output is Shut Off (Motor RotatesDuring DC Injection Braking)
- Output Frequency is Not as High as Frequency Reference
- Sound from Motor
- Motor Does Not Restart after Power Loss
- The Safety Controller Does Not Recognize Safe Disable MonitorOutput Signals (Terminals DM+ and DM-)
- Periodic Inspection & Maintenance
- Specifications
- Parameter List
- Parameter Groups
- A: Initialization Parameters
- b: Application
- C: Tuning
- d: References
- E: Motor Parameters
- F: Options
- H Parameters: Multi-Function Terminals
- L: Protection Function
- n: Special Adjustment
- o: Operator-Related Settings
- S: HVAC Function
- T: Motor Tuning
- U: Monitors
- Z: Bypass Parameters
- Defaults by Drive Model
- BACnet Communications
- MEMOBUS/Modbus Communications
- Apogee FLN Network Protocol
- Metasys N2 Network Protocol
- Standards Compliance
- Quick Reference Sheet