New functions of software 548328-04 – HEIDENHAIN SW 548328-05 User Manual
Page 6
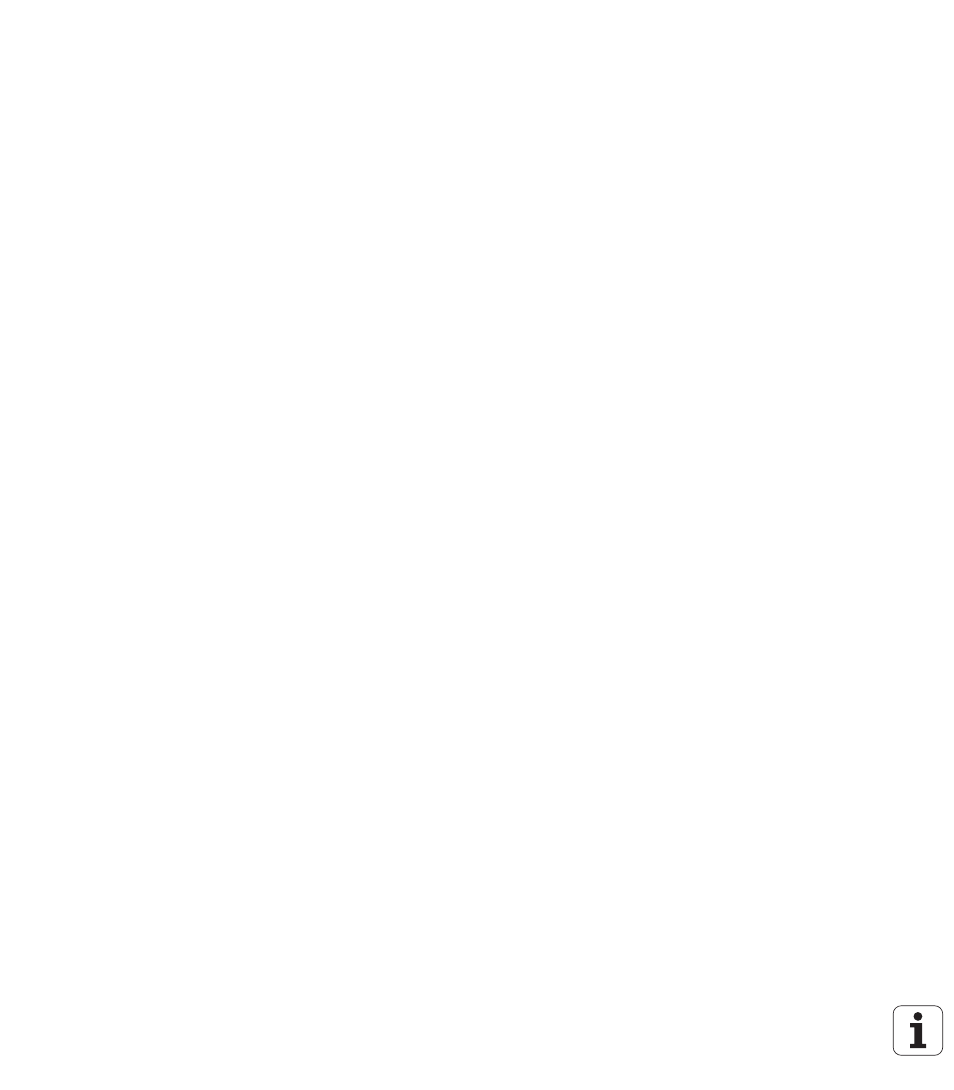
6
New functions of software 548328-04
In the program simulation, the current contour description (of
workpiece blank and finished part) can be mirrored and saved. In
smart.Turn, these contours can be reinserted (see page 473)
On machines with counterspindle, the workpiece spindle can now
be selected in the TSF menu (see page 93)
On machines with a counterspindle, it’s datum can be shifted (see
Page 93)
The user documentation is now also available in the context-
sensitive help system TURNguide (see page 64)
You can make your own project folder in the project management,
so that you can centrally manage associated files (see page 114)
With a manual tool change system it is possible to insert tools that
are not in the turret during a program run (see page 484)
Engraving cycles are now available in the Teach-In mode of
operation (see Page 328)
During tool data backup, you can now select in a dialog window the
data to be saved or restored (see page 554)
The G30 function is now available for converting G functions, M
functions or spindle numbers, as well as for mirroring traverse paths
and tool dimensions (see the smart.Turn and ISO Programming
User’s Manual)
The "traverse to a fixed stop" function (G916) is now available for
transferring the workpiece to the second traversable spindle or for
pressing the tailstock against the workpiece (see the smart.Turn and
ISO Programming User’s Manual)
The G925 function makes it possible to define and monitor the
maximum contact force for an axis. This function can be applied to
use the opposing spindle as a mechatronic tailstock, for example
(see the smart.Turn and ISO Programming User’s Manual)
Controlled parting using servo-lag monitoring (G917) can now be
activated to prevent collisions caused by incomplete parting
processes (see the smart.Turn and ISO Programming User’s
Manual)