Regular (periodical) inspection – KEYENCE GL-RHG Series User Manual
Page 133
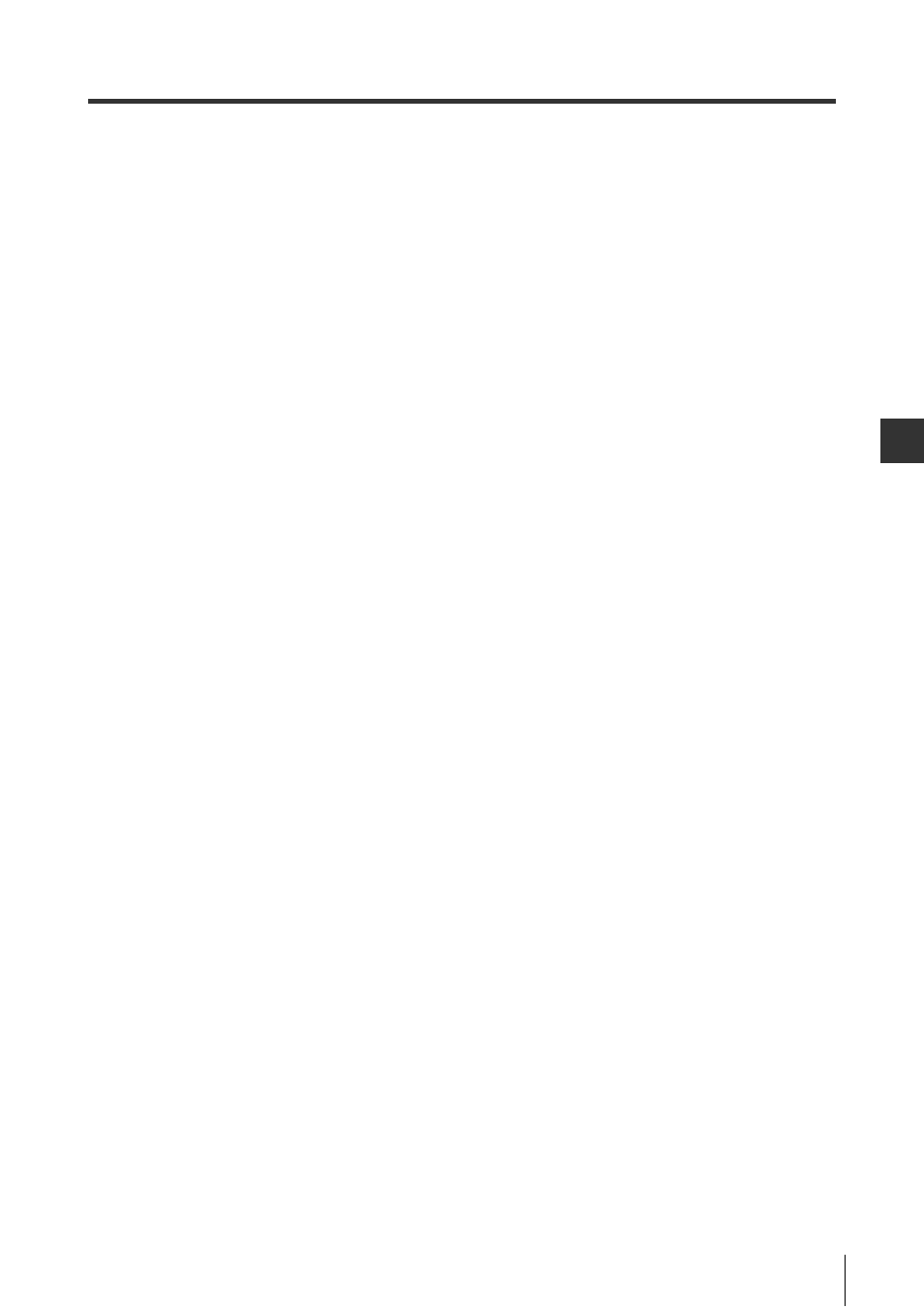
2
Checklist
A-9
GL-RHG-M-NOA-E
App
end
ix
Inspection prior to daily operation (Daily inspection)
You should check the GL-RHG operation and the machine operation according to the following checklist
prior to daily operation.
Note that the following inspection items comprise only a bare minimum inspection. KEYENCE Corporation
strongly recommends including the necessary checking items into this checklist based on the judgment of
the responsible personnel since additional criteria may be necessary depending on both the machine to
which the GL-RHG is installed and the laws, rules, regulations and standards in the country or region in
which the GL-RHG is used/installed.
The result of this inspection must be kept on record along with the machine log.
(1) Pre-check for installation condition
The GL-RHG is installed so that the machine operator cannot go into or approach the hazardous area
without passing through the protective zone.
The GL-RHG has been installed at a distance greater than or equal to the minimum safety distance
required.
The GL-RHG is installed at a location free from light interference, for example fluorescent lamps.
The cable sheaths are not damaged. The protection against the disconnection or short-circuit of cable,
which might be caused by crushing or being caught in a machine, is taken into account.
Additionally, you should perform the following inspections as described in "Inspection before opera-
tion".
(3) Pre-check test while the machine is stopped
(4) Pre-check test while the machine is operating
There is no change of installation that would influence the result of your original risk assessment.
Regular (periodical) inspection
The responsible personnel must perform a regular inspection.
It is recommended to perform a regular inspection at least once every six months.
Note that the following inspection items comprise only a bare minimum inspection. KEYENCE Corporation
strongly recommends including the necessary checking items into this checklist based on the judgment of
the responsible personnel since additional criteria may be necessary depending on both the machine to
which the GL-RHG is installed and the laws, rules, regulations and standards in the country or region in
which the GL-RHG is used/installed.
The result of this inspection must be kept on record along with the machine log.
(1) Additional inspection items
The actual distance between the hazardous zone or hazards and the GL-RHG still keeps greater than
the calculated safety distance.
The stop time of the machine connected to the GL-RHG has not increased.
There are no loose screws in the mounting bracket.
The unit connection cable or the series connection cable is fastened tightly to the GL-RHG with no
loose screws.
The OSSD is connected correctly to the machine.
There is no damage to the GL-RHG that may influence IP65 structure.
The surface of the GL-RHG is not polluted or damaged.
Beam axes must be aligned. If it is out of alignment, beam axes are aligned.
There is no change of installation that would influence the result of your original risk assessment.