Rockwell Automation 20A PowerFlex 70EC/700VC User Manual
Page 88
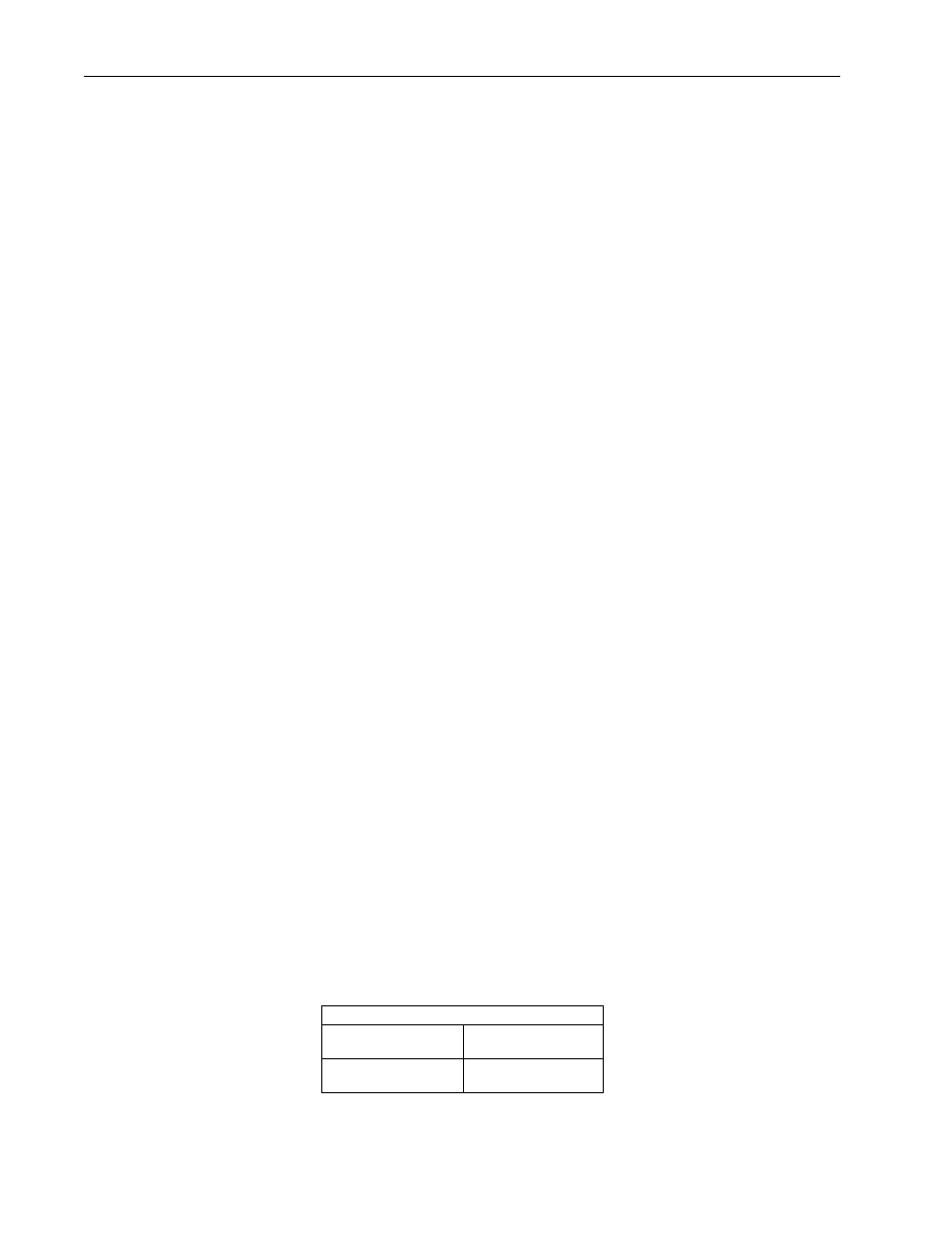
84
Process PID Loop
PID Status
[PI Status] parameter is a set of bits that indicate the status of the process PID
controller
•
Enabled - The loop is active and controlling the drive output.
•
Hold - A signal has been issued and the integrator is being held at its current
value.
•
Reset - A signal has been issued and the integrator is being held at zero.
•
In Limit - The loop output is being clamped at the value set in [PI Upper/Lower
Limit].
PID Reference and Feedback
The selection of the source for the reference signal is entered in the PID Reference
Select parameter. The selection of the source for the feedback signal is selected in
the PID Feedback Select parameter. The reference and feedback have the same
limit of possible options.
Options include DPI adapter ports, MOP, preset speeds, analog inputs, pulse input,
encoder input and PID setpoint parameter.
The value used for reference is displayed in PID Reference as a read only
parameter. The value used for feedback is displayed in PID Feedback as a read only
parameter. These displays are active independent of PID Enabled. Full scale is
displayed as
±100.00.
PID Reference and Feedback Scaling
The PID reference can be scaled by using [PI Reference Hi] and [PI Reference Lo].
[PI Reference Hi] determines the high value, in percent, for the PID reference. [PI
Reference Lo] determines the low value, in percent, for the PID reference.
The PID feedback can be scaled by using [PI Feedback Hi] and [PI Feedback Lo].
[PI Feedback Hi] determines the high value, in percent, for the PID feedback. [PI
Feedback Lo] determines the low value, in percent, for the PID feedback.
Example:
The PID reference meter and PID feedback meter should be displayed as positive and negative values.
Feedback from our dancer comes into Analog Input 2 as a 0-10V DC signal.
− [PI Reference Sel] = 0 “PI Setpoint”
− [PI Setpoint] = 50%
− [PI Feedback Sel] = 2 “Analog In 2"
− [PI Reference Hi] = 100%
− [PI Reference Lo] = –100%
− [PI Feedback Hi] = 100%
− [PI Feedback Lo] = 0%
− [Analog In 2 Hi] = 10V
− [Analog In 2 Lo] = 0V
Now 5V corresponds to 50% on the PID Feedback, and we will try to maintain a
PID setpoint of 50% (5V).
PI Feedback Scaling
[Torque Ref A Sel] = “Analog In 1”
[Analog In 2 Hi]
10V
[PI Feedback Hi]
100%
[Analog In 1 Lo]
0V
[PI Feedback Lo]
0%