Rockwell Automation 20A PowerFlex 70EC/700VC User Manual
Page 110
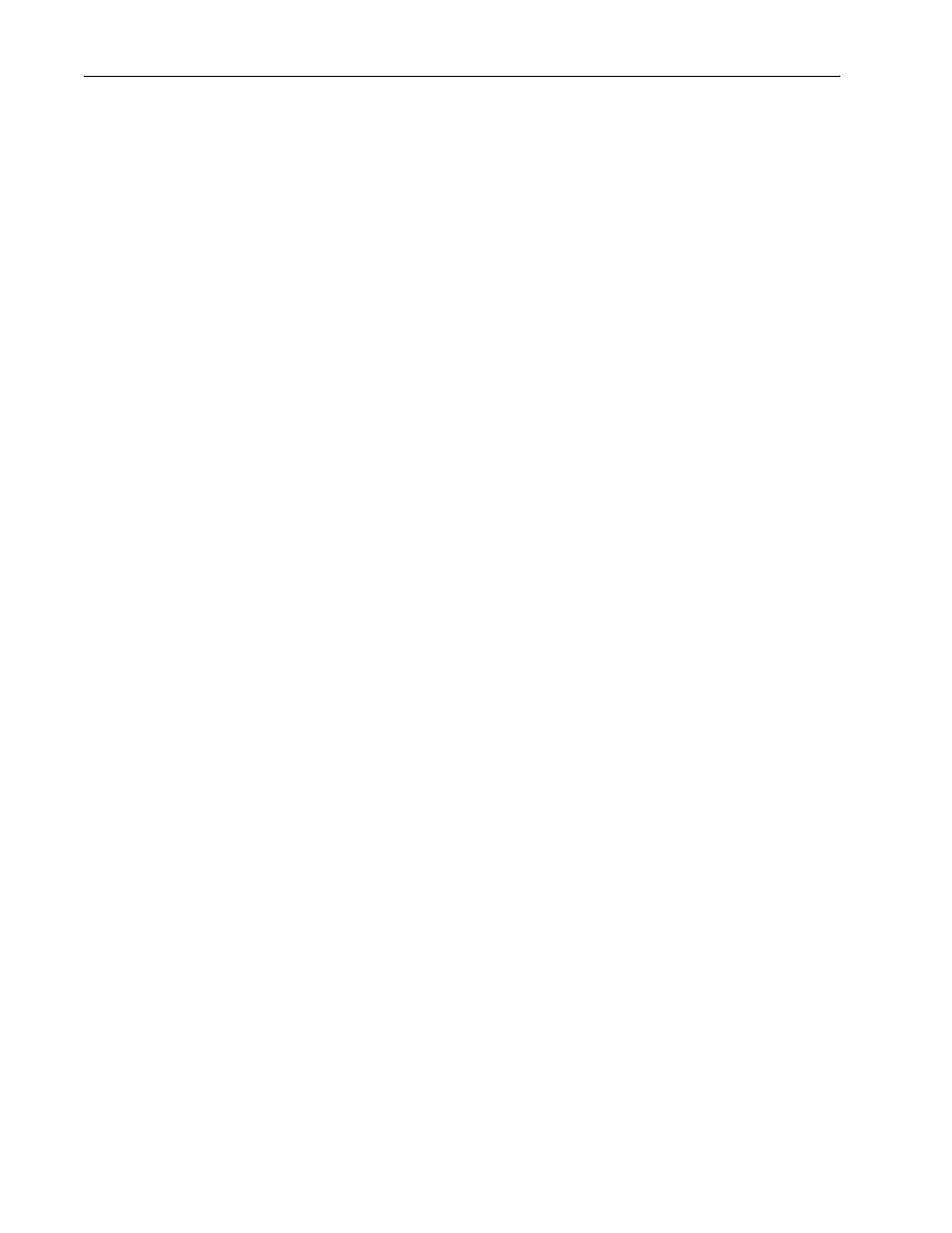
106
Speed/Torque Mode
The Min mode is typically used with positive torque and forward speed operation,
the minimum of the two being closest to zero. The Max mode is opposite, typically
used with reverse speed and negative torque, the maximum being the least negative
(closest to zero). Sum mode is selected when set to “5.” This mode allows an
external torque command to be added to the speed regulator output.
Zero Torque Mode
Operation in zero torque mode allows the motor to be fully fluxed and ready to
rotate when a speed command or torque command is given. For a cyclical
application where through put is a high priority this mode can be used. The control
logic can select zero torque during the “rest” portion of a machine cycle instead of
stopping the drive. When the cycle start occurs, instead of issuing a start to the
drive, a speed regulate mode can be selected. The drive will then immediately
accelerate the motor without the need for “flux up” time.
Important: Zero Torque may excessively heat the motor if operated in this mode
for extended periods of time. Flux current is still present when the
drive is operating in zero torque mode. A motor with an extended
speed range or separate cooling methods (blower) may be required.
Speed Regulation Mode
Operating as a speed regulator is the most common and therefore simplest mode to
setup. Examples of speed regulated applications are blowers, conveyors, feeders,
pumps, saws, and tools. In a speed regulated application, the torque reference is
generated by the speed regulator output. Note that under steady state conditions the
speed feedback is steady while the torque reference is a constantly adjusting signal.
This is required to maintain the desired speed. At transient state, the torque
reference will change dramatically to compensate for a speed change. A short
duration change in speed is the result of increasing or decreasing the load very
rapidly.
Torque Regulation Mode
A torque regulated application can be described as any process that requires some
tension control. An example of this is a winder or unwind where material is being
“drawn” or pulled with a specific tension required. The process requires another
element setting the speed. Configuring the drive for torque regulation requires
[Speed/Torque Mod] to be set to “2.” In addition, a torque reference signal must be
selected through [Torque Ref A] or [Torque Ref B]. When operating in torque
mode, the motor current will be adjusted to achieve the desired torque. If the
material being wound/unwound breaks, the load will decrease dramatically and the
motor can potentially go into a “runaway” condition.
Torque Reference
[Torque Ref A Hi] and [Torque Ref A Lo], parameters 428 & 429 are used to scale
Torque Ref A only when [Torque Ref A Sel], parameter 427 is set to an analog
output. Torque Ref A is divided by [Torq Ref A Div], parameter 430 (PF700VC
only) regardless of the source of Torque Ref A.
[Torque Ref B Hi] and [Torque Ref B Lo], Parameter 432 & 433 are used to scale
Torque Ref B only when [Torque Ref B Sel], parameter 431 is set to an analog
output. Torque Ref B is multiplied by [Torq Ref B Mult] regardless of the source of
Torque Ref A. Note: Only the PF700VC has a second torque reference (“Torque
Ref B”).