Rockwell Automation 20A PowerFlex 70EC/700VC User Manual
Page 85
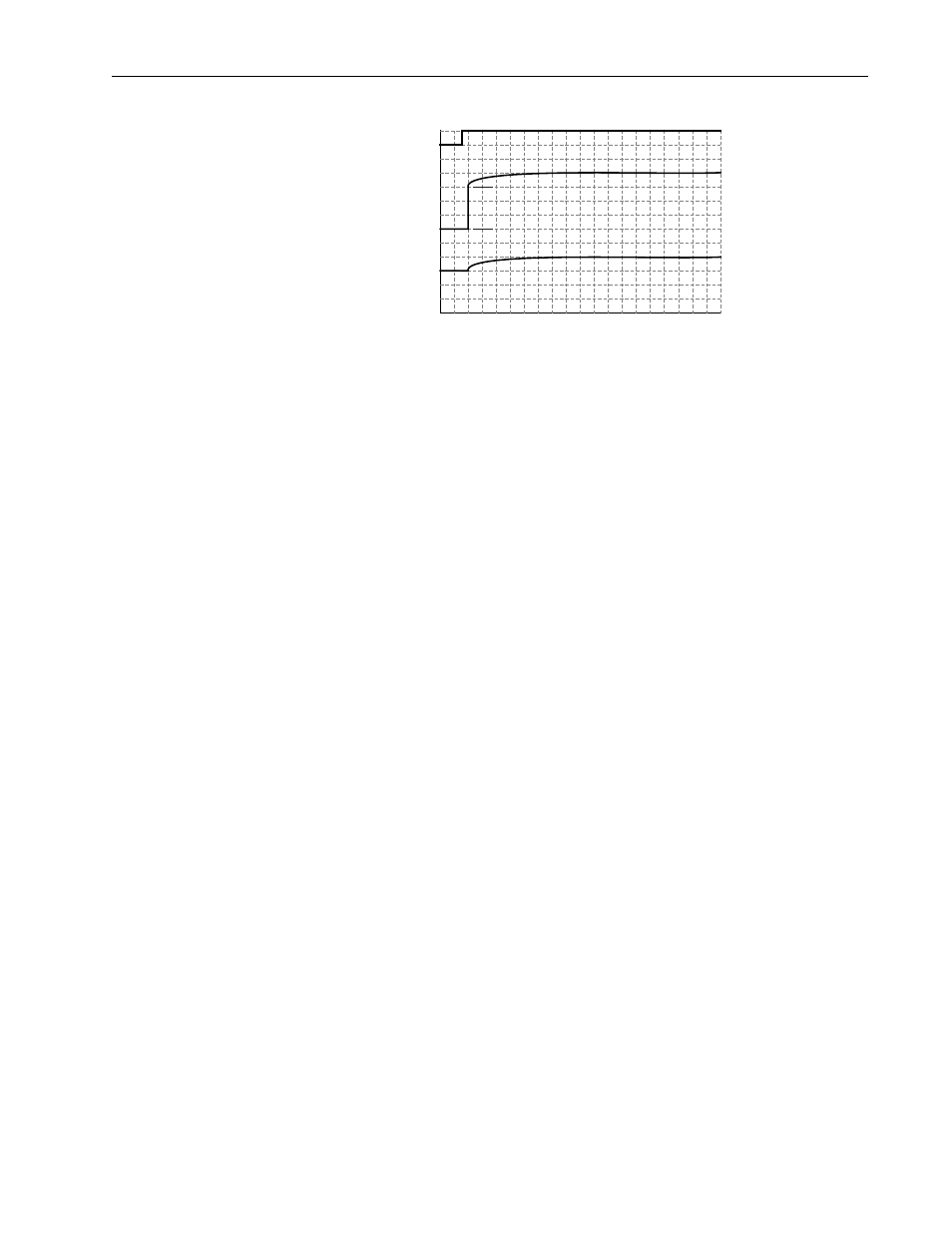
Process PID Loop
81
When the PID is configured to have exclusive control of the commanded speed and
the drive is in current limit or voltage limit the integrator is preset to the
commanded speed so that it knows where to resume when no longer in limit.
•
Ramp Ref - The PID Ramp Reference feature is used to provide a smooth
transition when the PID is enabled and the PID output is used as a speed trim
(not exclusive control). When PID Ramp Reference is selected in the PID
Configuration parameter, and PID is disabled, the value used for the PID
reference will be the PID feedback. This will cause PID error to be zero. Then
when the PID is enabled the value used for the PID reference will ramp to the
selected value for PID reference at the selected acceleration or deceleration rate.
After the PID reference reaches the selected value the ramp is bypassed until the
PID is disabled and enabled again. S-curve is not available as part of the PID
linear ramp.
•
Zero Clamp - This feature limits the possible drive action to one direction only.
Output from the drive will be from zero to maximum frequency forward or zero
to maximum frequency reverse. This removes the chance of doing a “plugging”
type operation as an attempt to bring the error to zero. This bit is active only in
trim mode.
The PID has the option to limit operation so that the output frequency will
always have the same sign as the master speed reference. The zero clamp option
is selected in the PID Configuration parameter. Zero clamp is disabled when
PID has exclusive control of speed command.
For example, if master speed reference is +10 Hz and the output of the PID
results in a speed adder of –15 Hz, zero clamp would limit the output frequency
to not become less than zero. Likewise, if master speed reference is –10 Hz and
the output of the PID results in a speed adder of +15 Hz, zero clamp would limit
the output frequency to not become greater than zero.
•
Feedback Square Root - This feature uses the square root of the feedback
signal as the PID feedback. This is useful in processes that control pressure,
since centrifugal fans and pumps vary pressure with the square of speed.
The PID has the option to take the square root of the selected feedback signal.
This is used to linearize the feedback when the transducer produces the process
variable squared. The result of the square root is normalized back to full scale to
provide a consistent range of operation. The option to take the square root is
selected in the PID Configuration parameter.
Pre-load to Command Speed
PI Enabled
Spd Cmd
PI Output
Start at Spd Cmd