Encoder feedback (closed loop) – Rockwell Automation 20A PowerFlex 70EC/700VC User Manual
Page 107
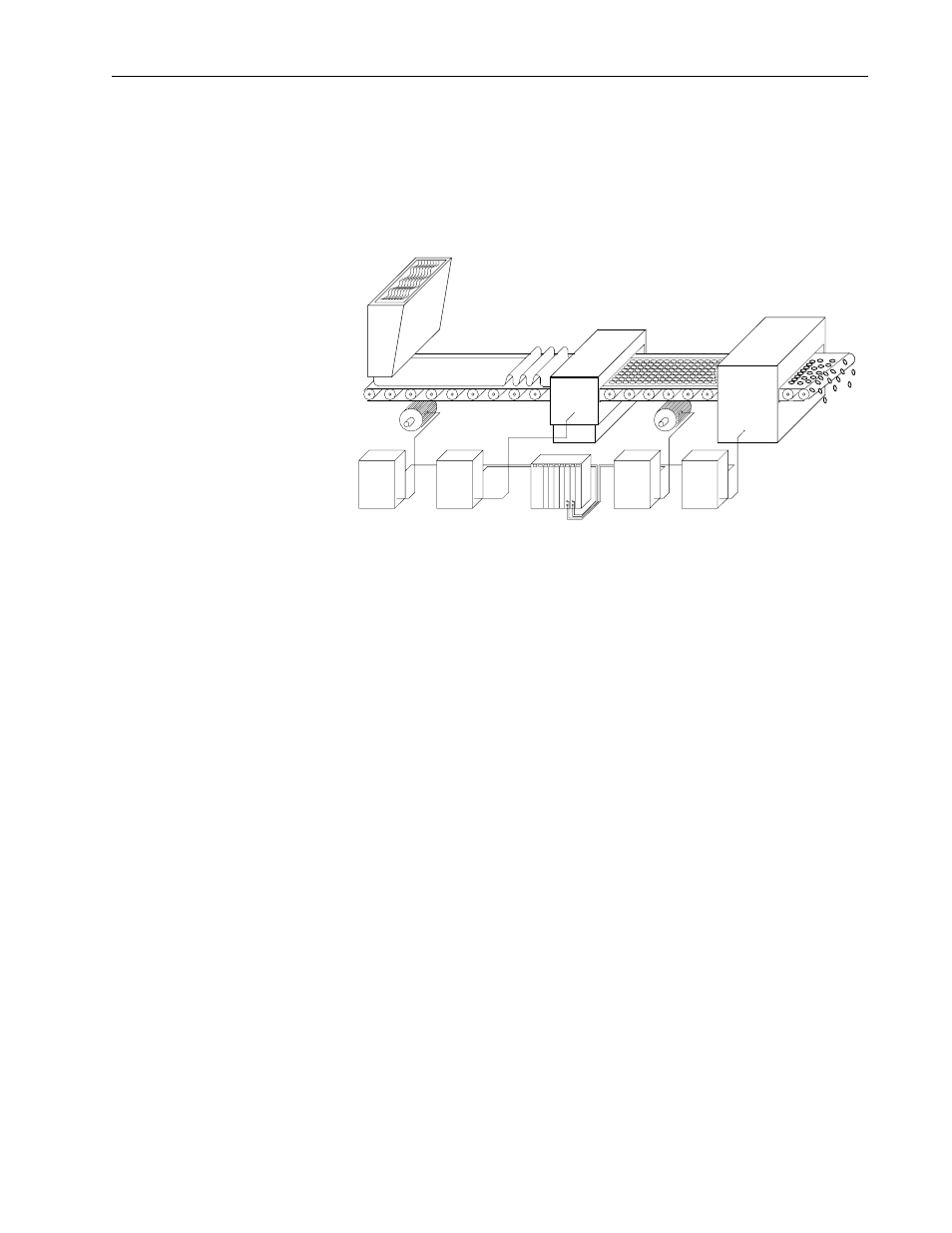
Speed Regulation
103
Application Example - Baking Line
The diagram below shows a typical application for the Slip Compensation feature.
The PLC controls the frequency reference for all four of the drives. Drive #1 and
Drive #3 control the speed of the belt conveyor. Slip compensation will be used to
maintain the RPM independent of load changes caused by the cutter or dough feed.
By maintaining the required RPM, the baking time remains constant and therefore
the end product is consistent.
Encoder Feedback (Closed Loop)
An encoder offers the best performance for both speed and torque regulation
applications, providing high bandwidth response, tight speed regulation, torque
regulation, and very low speed operation (less than 1/120
th
of base motor speed).
•
[Motor Fdbk Type] selects the type of encoder:
– “Quadrature” – dual channel.
– “Quad Check” – dual channel and detects loss of encoder signal when using
differential inputs.
– “Single Chan” – pulse type, single channel.
– “Single Check” – pulse type, single channel and detects loss of encoder
signal when using differential inputs.
•
[Encoder PPR] sets the number of encoder pulses per revolution.
•
[Enc Pos Feedback] displays the raw encoder count. For single channel
encoders, this count will increase (per rev.) by the amount in [Encoder PPR].
For quadrature encoders this count will increase by 4 times the amount defined
in [Encoder PPR].
In closed loop mode, the drive uses proportional and integral gains to adjust the
torque reference that is sent to the motor and produces a high bandwidth response
to speed command and load changes.
PowerFlex
Drive
PowerFlex
Drive
PowerFlex
Drive
PowerFlex
Drive
#1
#2
#4
5/40
#3
Dough Stress
Relief
Cookie Line
CUTTERS
OVEN