Rockwell Automation 20A PowerFlex 70EC/700VC User Manual
Page 38
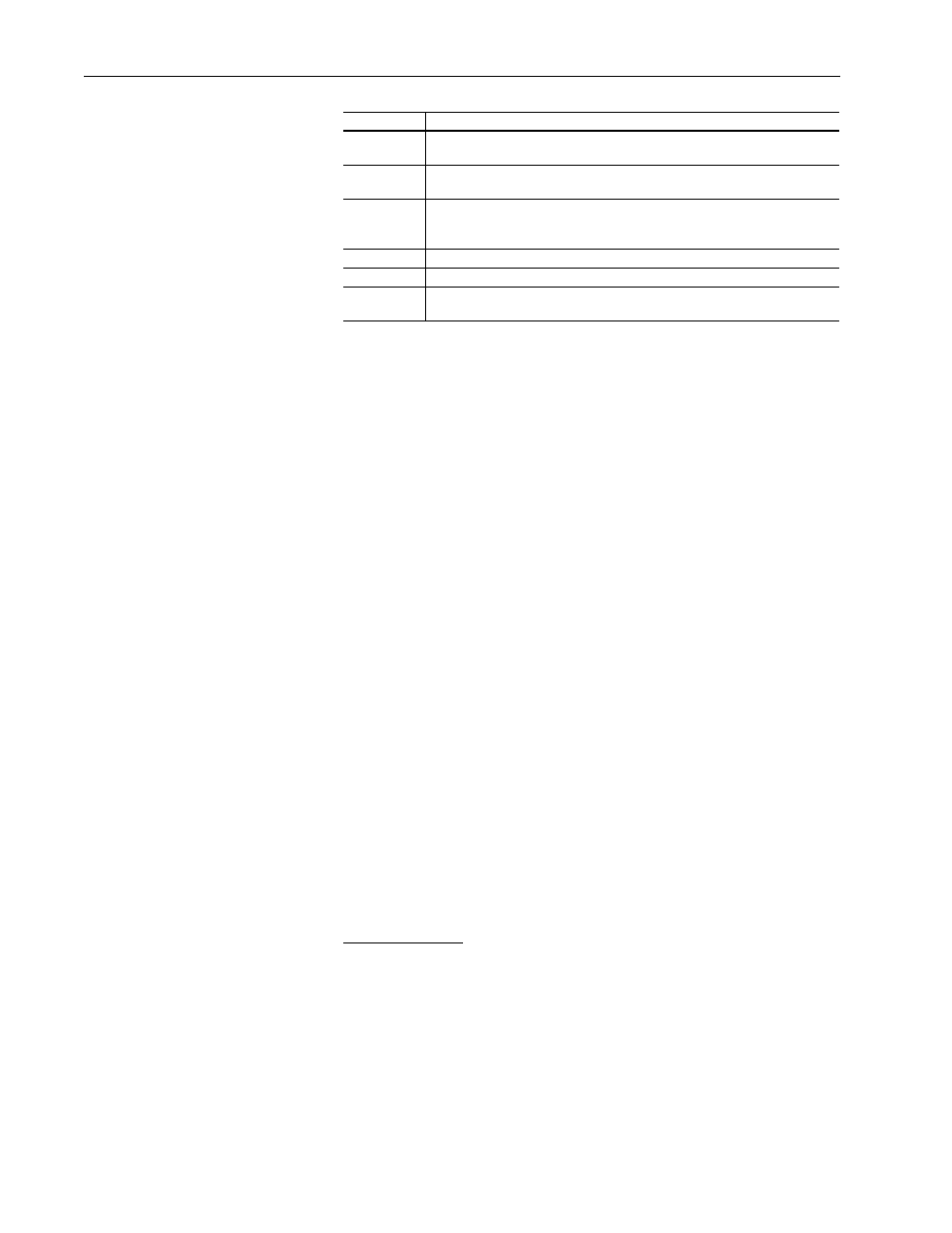
34
Digital Outputs
Digital Out Mask Function
This feature provides a method for one of the digital outputs to change state
based on monitoring of individual parameter bits. An AND or OR function can
be chosen to determine the output result, based on the state of more than one bit
in the selected source parameter.
Configuration
Parameters 380, 384, 388 [Digital Outx Sel] applies the mask function to the
selected value in Parameter 393 [Dig Out Param]. A value of 31 chooses “Mask
1 AND” and a value of 32 chooses “Mask 1 OR”. Note: there is only one
parameter (P393) that can feed this function with data and only 1 parameter
(P394) than can mask the data. However, each digital output can apply either the
AND function or the OR function to the result before it takes action on a digital
output. The choices for parameter 393 are shown in the User Manual.
While monitoring the value of a particular choice for Parameter 393 [Dig Out
Param], only the bits with a corresponding value of “1” in Parameter 394 [Dig
Out Mask], will be monitored and passed through to the AND or OR digital
output functions. All of the bits with zeros in the mask are ignored.
Example
This example demonstrates how to turn on a digital output if dynamic braking is occurring (the
dynamic brake transistor is switching) and bus frequency regulation is also occurring. This would
be an indication that the connected brake resistor is shunting energy, but there is too much
regeneration for that moment in time and the drive is not following its commanded decel rate.
− P393 [Dig Out Param] = “Drive Sts 2"
− P380 [Digital Out 1 Sel] = “Mask 1 AND”
− P394 [Dig Out Mask] = 0 0 0 0 1 0 0 0 1 0 0 0 0 0 0 0
Setting bits 7 and 11 of [Dig Out Mask] equal to 1 allows bit 7 (“DB Active”) and bit 11 (“Bus Freq
Reg”) of [Drive Status 2]) to pass through to the AND function. This way, when both of these
conditions occur together, the digital output will turn on.
2.
Exceeded Levels
These functions require a level to be programmed into [Dig Out1 Level] and/or
[Dig Out2 Level] depending on the output(s) being used. If the value for the
specified function (frequency, current, etc.) exceeds the programmed limit, the
output will activate. If the value falls back below the limit, the output will
deactivate.
Notice that the [Dig Outx Level] parameters do not have units. The drive
assumes the units from the selected function. For example, if the selection is
current, the drive assumes that the value for [Dig Outx Level] is % rated Amps.
If the selection is Temperature, the drive assumes that the value for [Dig Outx
Economize
The drive is currently reducing the output voltage to the motor to attempt to
reduce energy costs during a lightly loaded situation.
Motor Overld
The drive output current has exceeded the programmed [Motor NP FLA] and the
electronic motor overload function is accumulating towards an eventual trip.
Power Loss
The drive has monitored DC bus voltage and sensed a loss of input AC power
that caused the DC bus voltage to fall below the fixed monitoring value (82% of
[DC bus Memory]
PI Enabled
The drive’s process PID controller has been enabled (see “Process PID”).
PI Hold
The process PID integrator is being held (see “Process PID”).
Drive Overld
The drive is in a overload condition and will take action to avoid a fault, or
possibly fault if the load is not reduced (see “Drive Overload”).
Condition
Description