Current limit, Datalinks, Current limit datalinks – Rockwell Automation 20A PowerFlex 70EC/700VC User Manual
Page 28
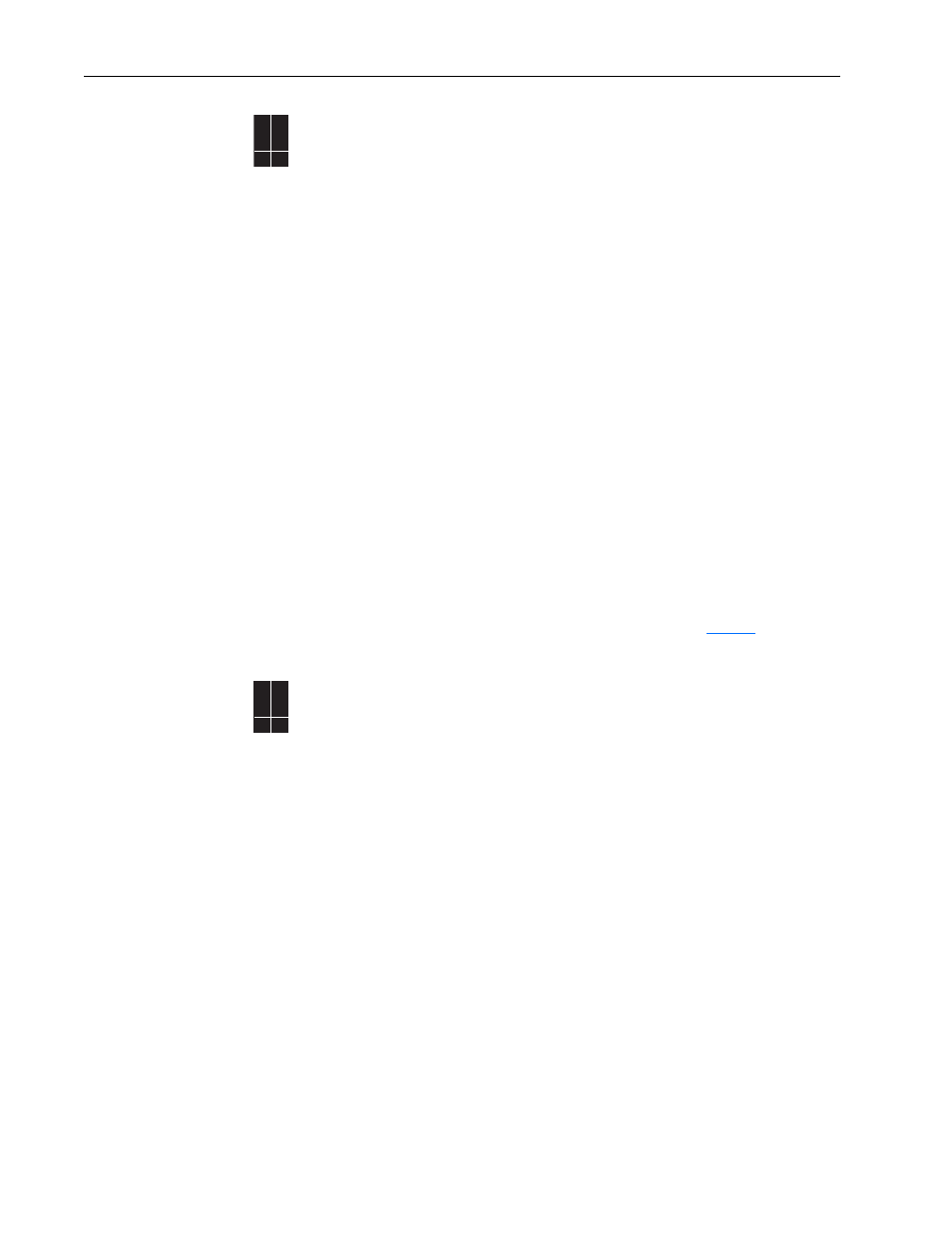
24
Current Limit
Current Limit
There are 5 ways that the drive can protect itself from overcurrent or overload
situations:
•
Hardware Overcurrent - This is a feature that instantly faults the drive if the
output current exceeds this value. The value is fixed by hardware and is
typically 250% of drive rated amps. The fault code for this feature is F12 “HW
Overcurrent.” This feature cannot be defeated or mitigated.
•
Software Overcurrent - This protection mode occurs when peak currents do not
reach the Hardware Overcurrent value and are sustained long enough and high
enough to damage certain drive components. If this situation occurs, the drives
protection scheme will cause an F36 “SW Overcurrent” fault. The point at
which this fault occurs is fixed and stored in drive memory.
•
Software Current Limit - This is a feature that attempts to reduce current by
folding back output voltage and frequency if the output current exceeds a
programmable value. The [Current Lmt Val] parameter is programmable
between approximately 25% and 150% of drive rating. The reaction to
exceeding this value is programmable with [Shear Pin Fault]. Enabling this
parameter creates an F63 “Shear Pin Fault.” Disabling this parameter causes the
drive to use fold back to attempt load reduction.
•
Heatsink Temperature Protection - The drive constantly monitors the heatsink
temperature. If the temperature exceeds the drive maximum, a “Heatsink
OvrTemp” fault will occur. The value is fixed by hardware at a nominal value of
100 degrees C. This fault is generally not used for overcurrent protection due to
the thermal time constant of the heatsink. It is an overload protection.
•
Drive Overload Protection - Refer to "Drive Overload" on
.
Datalinks
A Datalink is one of the mechanisms used by PowerFlex drives to transfer data to
and from a programmable controller. Datalinks allow a parameter value to be
changed without using an Explicit Message or Block Transfer. Datalinks consist of
a pair of parameters that can be used independently for 16 bit transfers or in
conjunction for 32 bit transfers. Because each Datalink consists of a pair of
parameters, each Datalink occupies two 16 or 32-bit words in both the input and
output image tables, depending on configuration. A parameter number is entered
into the Datalink parameter. The value that is in the corresponding output data table
word in the controller is then transferred to the parameter whose number has been
placed in the Datalink parameter. The following example demonstrates this
concept. The object of the example is to change Accel and Decel times “on the fly”
under PLC control.
The user makes the following PowerFlex drive parameter settings:
[Data In A1], parameter 300 = 140 (parameter number of [Accel Time 1]
[Data In A2], parameter 301 = 142 (parameter number of [Decel Time 1]
In the PLC data Table, the user enters Word 3 as a value of 100 (10.0 Secs) and
word 4 as a value of 133 (13.3 seconds). On each I/O scan, the parameters in the
PowerFlex drive are updated with the value from the data table:
[Accel Time], parameter 140 = 10.0 seconds (output image table Word 3 value)
[Decel Time], parameter 142 = 13.3 seconds (output image table Word 4 value).
Any time these values need to be changed, the new values are entered into the data
table, and the parameters are updated on the next PLC I/O scan.
70EC
700VC
700H
✔ ✔
70EC
700VC
700H
✔ ✔