Process pid loop, Loop. see "process pid loop" on, See "process pid loop" on – Rockwell Automation 20A PowerFlex 70EC/700VC User Manual
Page 81: Process pid loop" on
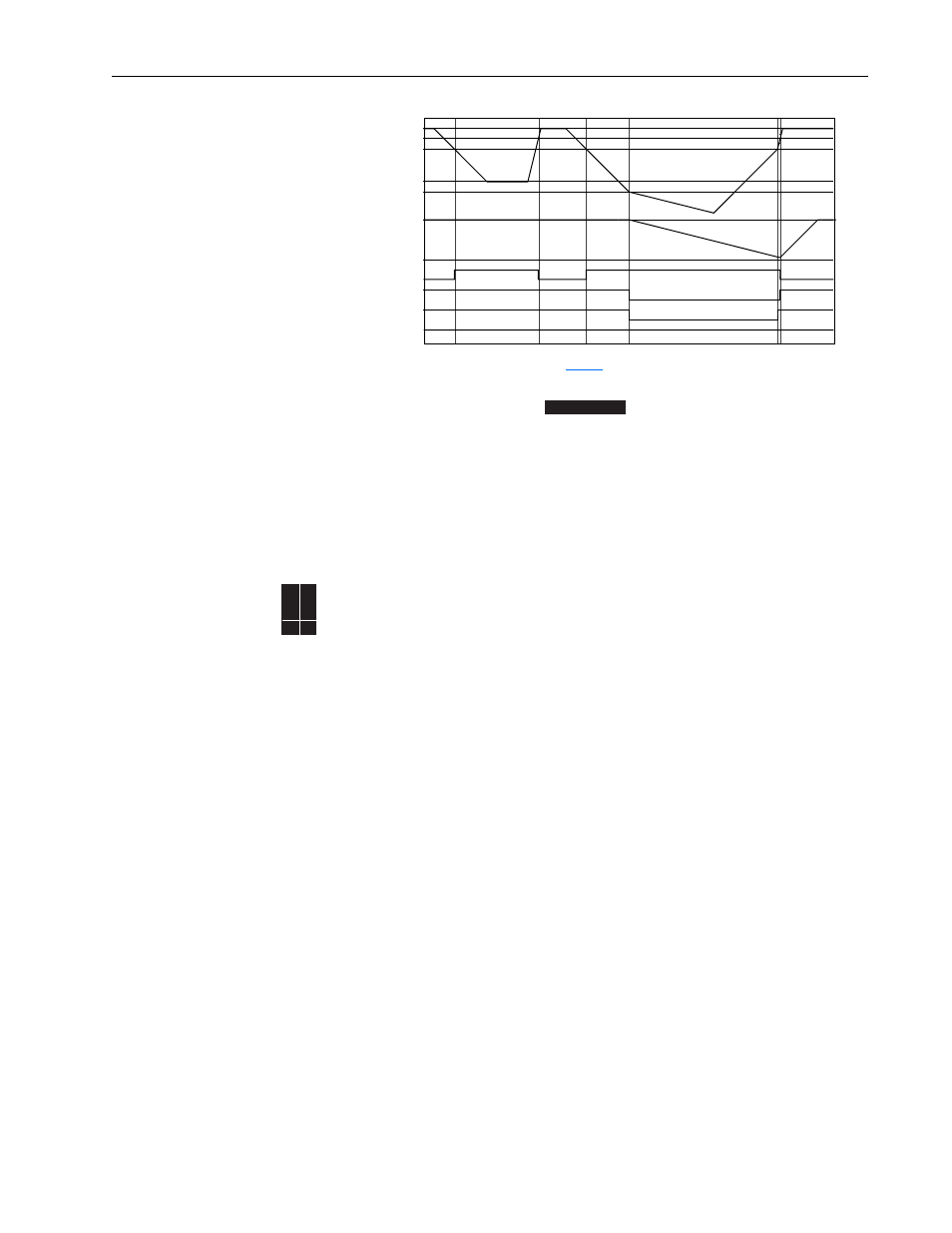
Process PID Loop
77
Coast Input and Decel Input
These modes operate similarly to their “non-input” versions, but provide additional
ride through time. This is accomplished by early sensing of the power loss via an
external device that monitors the power line. This device provides a hardware
signal which is connected to the drive through the “pulse” input (because of its
high-speed capability). Normally this hardware power loss input will provide a
power loss signal before the bus drops to less than V
open.
Process PID Loop
The internal PID function provides closed loop process control with proportional
and integral control action. The function is designed to be used in applications that
require simple control of a process without the use of a separate stand-alone loop
controller.
The PID function reads a process variable input to the drive and compares it to a
desired setpoint stored in the drive. The algorithm will then adjust the output of the
PID regulator, changing drive output frequency to attempt zero error between the
process variable and the setpoint.
The Process PID can be used to modify the commanded speed or can be used to
trim torque. There are two ways the PID Controller can be configured to modify the
commanded speed.
•
Speed Trim - The PID Output can be added to the master speed reference.
•
Exclusive Control - PID can have exclusive control of the commanded speed.
The mode of operation between speed trim, exclusive control, and torque trim is
selected in the [PI Configuration] parameter.
Speed Trim Mode
In this mode, the output of the PID regulator is summed with a master speed
reference to control the process. This mode is appropriate when the process needs
to be controlled tightly and in a stable manner by adding or subtracting small
amounts directly to the output frequency (speed). In the following example, the
master speed reference sets the wind/unwind speed and the dancer pot signal is
used as a PID Feedback to control the tension in the system. An equilibrium point is
programmed as PID Setpoint, and as the tension increases or decreases during
winding, the master speed is trimmed to compensate and maintain tension near the
equilibrium point.
680V
620V
560V
305V
365V
Bus Voltage
Motor Speed
Output Enable
Power Loss
Drive Fault
Pre-Charge
480V example shown, see
Table F
for further information.
700VC
ONLY
70EC
700VC
700H
✔ ✔