Running a g-code program, Starting or stopping a g-code program, 2 f o lders – ACU-RITE MILLPWRG2 User Manual
Page 116
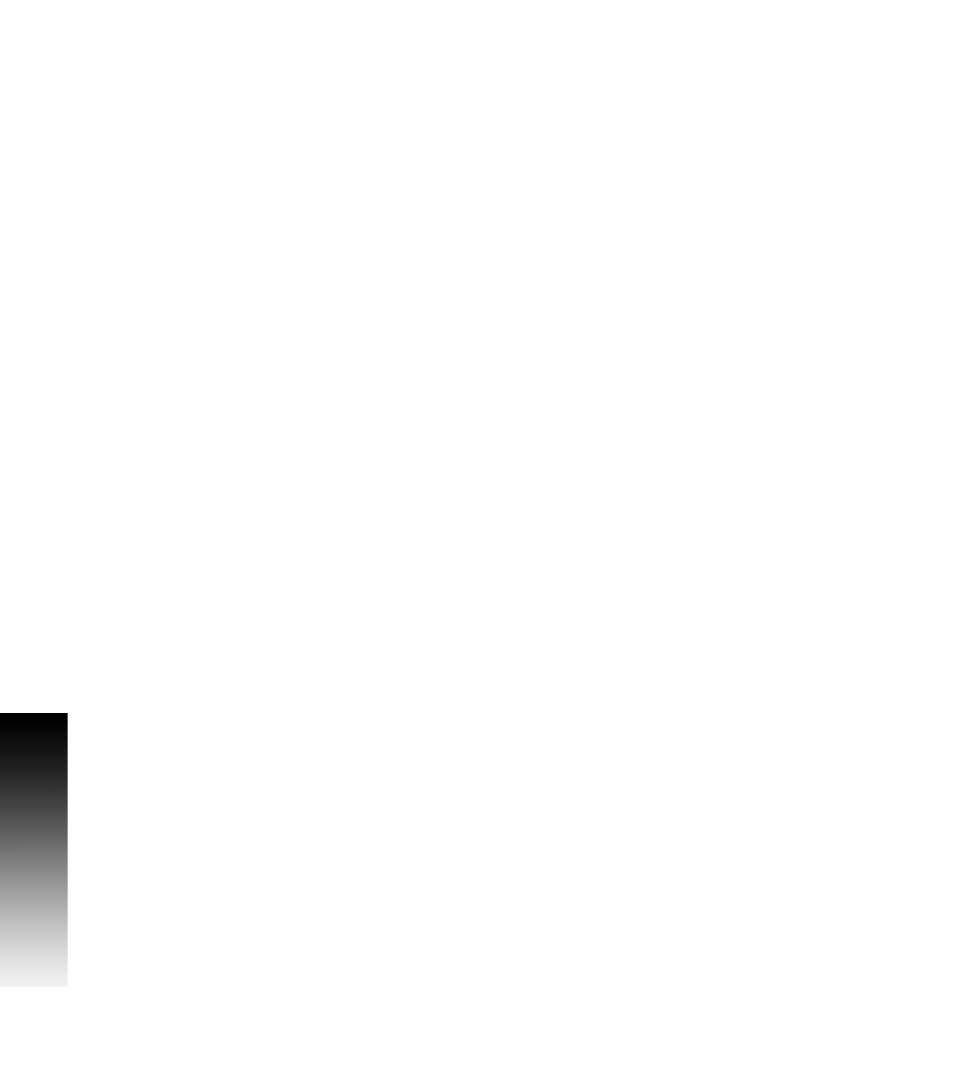
98
6 Programming
6.2 F
o
lders
Running a G-Code Program
MILLPWR
G2
has the ability to read and run G-code programs, however
those programs can not be edited by the MILLPWR
G2
. It is important
to create and proof the G-code program before attempting to machine
a part.
Verify the program in the CAD/CAM system that generated the
program. MILLPWR
G2
will draw the program when Loaded. Finally,
lower the knee and dry run the program to verify that the tool path,
feeds and speeds are correct.
Using the Tool Table
Each "T" block refers to the corresponding number in the Tool Table.
For example, T1 will cause MILLPWR
G2
to retrieve the tool length
offset from tool 1 of the Tool Table. MILLPWR
G2
will then offset the
spindle by this amount. T2 will cause MILLPWR
G2
to retrieve the tool
length offset from tool 2 of the Tool Table, etc. See chapter "4.1 Tool
Table" on page 44 for a complete description about using the Tool
Table.
It is very important not to have any tool length offsets in the Tool Table
if the tooling is not repeatable. The user will need to set the Z datum
after mounting the new tool. This is done before pressing GO to
continue running the program.
Failure to maintain the Tool Table can cause unpredictable results.
Verifying tool length offsets prior to program execution is strongly
recommended.
Starting or Stopping a G-code Program
Always start the program from a place in the program where the feed
rate, X, Y, and Z axes position are known, such as a tool step. Alternate
starting points can be programmed by placing the proper code in the
desired locations.
Pressing the GO button will cause MILLPWR
G2
to begin executing the
G-code program. Always insure the program step highlighted is an
appropriate starting point.
When a program is running, pressing the STOP button or the remote
pendant will cause the program and all axis motion to pause. Pressing
the remote pendant switch again or the GO button will cause the
program to resume. Pressing the STOP button a second time will halt
the program execution.