1 error analysis, Reference junction temperature with cr9050 – Campbell Scientific CR9000X Measurement and Control System User Manual
Page 99
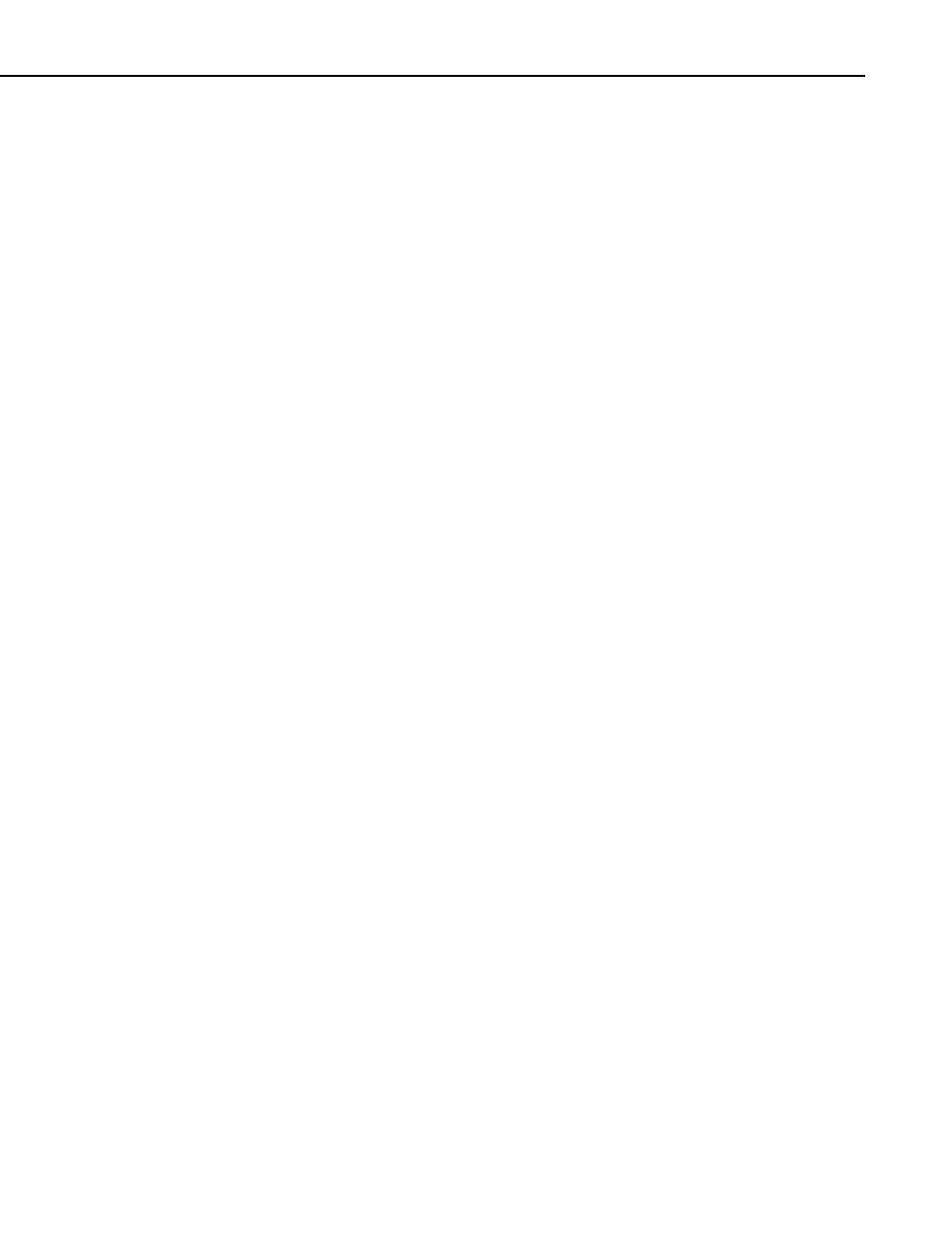
Section 3. CR9000X Measurement Details
would output at the reference junction temperature if its reference junction
were at 0
o
C, and adds this voltage to the measured thermocouple voltage. The
temperature of the measuring junction is then calculated from a polynomial
approximation of the NIST TC calibrations.
3.1.4.1 Error Analysis
The error in the measurement of a thermocouple temperature is the sum of the
errors in the reference junction temperature, the thermocouple output
(deviation from standards published in NIST Monograph 175), the
thermocouple voltage measurement, and the linearization error (difference
between NIST standard and CR9000X polynomial approximations). The
discussion of errors which follows is limited to these errors in calibration and
measurement and does not include errors in installation or matching the sensor
to the environment being measured.
Reference Junction Temperature with CR9050
The PRT in the CR9000X is mounted on the circuit board near the center of
the CR9050 terminal strip. This resistance temperature device (RTD) is
accurate to ±0.1
o
C over the CR9000X operating range.
The error in the reference temperature measurement is a combination of the
error in the thermistor temperature and the difference in temperature between
the module thermistor and the terminals the thermocouple is connected to.
When using the CR9051E, the insulated cover for the CR9051EZ connector
should always be used when making thermocouple measurements. It insulates
the terminals from drafts and rapid fluctuations in temperature as well as
conducting heat to reduce temperature gradients. Also, the foam block that
was supplied with the CR9000X should be utilized to minimize temperature
gradients.
The I/O Module was designed to minimize thermal gradients. It is encased in
an aluminum box which is thermally isolated from the CR9000X fiberglass
enclosure. Measurement modules have aluminum mounting plates extending
beyond the edges of the circuit cards that provide thermal conduction for rapid
equilibration of thermal gradients. Sources of heat within the CR9000X
enclosure exist due to power dissipation by the electronic components or
charging batteries. In a situation where the CR9000X is at an ambient
temperature of approximately 20
o
C and no external temperature gradients
exist, the temperature gradient between one end of an Analog Input module to
the other is likely to be less than 0.1
°C.
The gradient from one end of the I/O Chassis to the other, is likely to be about
4
°C. The end of the enclosure with the CPU Module will be warmer due to
heat dissipated by the processor.
For the best accuracy, use the temperature of each CR9050 module as the
reference temperature for any thermocouples attached to it. Given the above
conditions, this would keep the reference junctions within 0.05
°C of the
temperature of the RTD. When making more thermocouple measurements
than can be accomplished on a single CR9050 module, it is faster to measure
the temperature of one CR9050 module and use it for all thermocouples. If
3-11